BLOG » Neu bei meviy: Neue Kunststoffplatten-Anwendungen mit Gewindebohrungen und Gewindeeinsätzen
Neu bei meviy: Neue Kunststoffplatten-Anwendungen mit Gewindebohrungen und Gewindeeinsätzen
Plastic plates are widely used in various industries due to their lightweight, versatility, and cost-effectiveness. To further enhance their functionality, two important features—tapped holes and threaded insert holes—are now available in sheet metal fabrication services. These new options open up possibilities for plastic plates to be utilised in more demanding applications, such as equipment covers, partitions, and lightweight structural components, where precise fastening solutions are required.
Both tapped holes and threaded insert holes provide convenient methods for attaching fasteners to plastic plates, offering durability, ease of assembly, and reliability. Understanding the difference between these two features and their applications will help you choose the right option for your project.
What Are Tapped Holes?
A tapped hole is a pre-drilled hole that has been threaded to allow a screw or bolt to be securely fastened into it. In plastic plates, tapped holes are particularly useful for lightweight and medium-duty applications where direct threading into the material is sufficient to hold components together.
Tapped holes are advantageous because they eliminate the need for additional components like nuts or inserts, streamlining the assembly process and reducing the overall cost of the design. However, because plastic is a softer material, the threads created within the tapped hole may wear out over time if subjected to frequent use or high torque. This makes tapped holes ideal for applications where fasteners will not need to be repeatedly removed or tightened.
What Are Threaded Insert Holes?
A threaded insert hole is a pre-drilled hole designed to accommodate a threaded insert (threaded bushing), which is typically made of a harder material such as stainless steel. The threaded insert is installed into the plastic plate, creating a reinforced threaded surface that can withstand repeated fastening and unfastening without degrading the material.
Threaded insert holes are particularly beneficial for applications where durability and longevity are critical. For example, in industrial equipment or machinery that requires regular maintenance, the use of threaded inserts ensures that the fastening points remain reliable and secure over time.
Additionally, threaded inserts provide greater resistance to torque and shear forces compared to tapped holes, making them suitable for high-stress environments.
By offering both tapped holes and threaded insert holes, sheet metal fabrication services empower designers to customise plastic plates for a wide range of applications, balancing cost, durability, and performance. Whether you need a simple fastening solution or a robust option for high-frequency use, these features provide the flexibility you need for your projects.
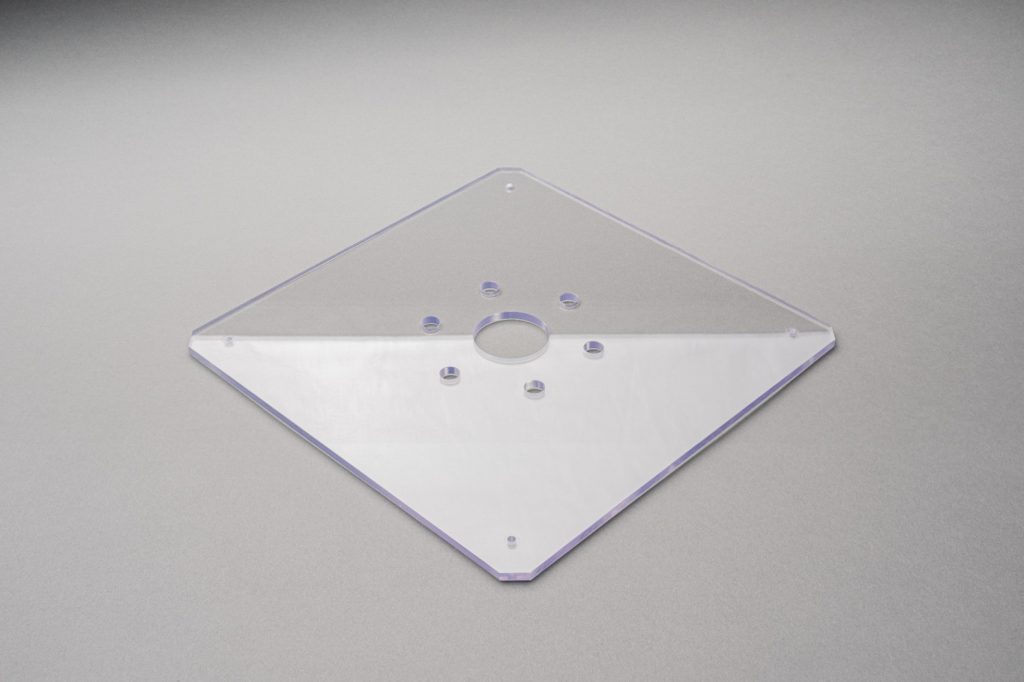
Thread Insert Nominal Diameter and Length (D) Available at meviy
The nominal length (D) for each nominal diameter is available in three options: „1D,“ „1.5D,“ and „2D.“
Material | Plate Thickness | Nominal Length | Nominal Diameter | ||||
---|---|---|---|---|---|---|---|
M3 | M4 | M5 | M6 | M8 | |||
|
3.0 | – | |||||
5.0 | 1D | 〇 | 〇 | ||||
1.5D | 〇 | ||||||
2D | |||||||
8.0 | 1D | 〇 | 〇 | 〇 | 〇 | ||
1.5D | 〇 | 〇 | 〇 | ||||
2D | 〇 | ||||||
10.0 | 1D | 〇 | 〇 | 〇 | 〇 | ||
1.5D | 〇 | 〇 | 〇 |
What is Plastic in Mechanical Components?
Plastic materials are a cornerstone in the manufacturing of mechanical components due to their versatility, lightweight properties, and cost-effectiveness. Unlike metals, plastics are less dense and exhibit excellent resistance to corrosion, making them suitable for various applications in industries such as automotive, electronics, and medical devices. Additionally, plastics can be easily moulded into complex shapes, offering design flexibility while reducing production costs.
Applications of Plastic Plates
Plastic plates find wide use in mechanical and industrial components due to their unique properties. These plates are commonly utilised for lightweight structural supports, insulation panels, and machine guards. Their softer nature allows for easy machining, cutting, and drilling, making them an ideal choice for projects requiring customised dimensions. Plastic plates are also resistant to chemicals, making them a preferred material for environments with exposure to oils, solvents, or other corrosive substances.
Don’t miss the chance to try out this convenient solution for reinforcing plastic plates today!