BLOG » CNC Fräsen vs. 3D-Druck im Prototypenbau – welche Methode ist die richtige?
CNC Fräsen vs. 3D-Druck im Prototypenbau – welche Methode ist die richtige?
Der Prototypenbau ist ein zentraler Bestandteil der Produktentwicklung: Er ermöglicht es Ingenieuren und Konstrukteuren, Form, Passgenauigkeit und Funktion eines Bauteils zu überprüfen, bevor es in die Serienfertigung geht. In einem innovationsgetriebenen Markt, in dem Geschwindigkeit entscheidend ist, kann die Fähigkeit, schnell und zuverlässig Prototypen herzustellen, über den Erfolg eines Produkts entscheiden.
Zu den am weitesten verbreiteten Verfahren im Prototyping zählen die CNC Fräsen und der 3D-Druck. Beide Technologien stehen für grundlegend unterschiedliche Fertigungsansätze – mit jeweils eigenen Vorteilen und Abwägungen, je nach Projektanforderung.
Der entscheidende Unterschied liegt im Herstellungsprinzip: CNC Fräsen ist ein subtraktives Verfahren, bei dem Material aus einem festen Rohling entfernt wird. 3D-Druck hingegen ist ein additives Verfahren, bei dem das Bauteil Schicht für Schicht aufgebaut wird.
In diesem Artikel vergleichen wir CNC Fräsen und 3D-Druck hinsichtlich ihrer Verfahren, Materialien, Eigenschaften, Zeitaufwand, Kosten und Designfreiheit – damit du eine fundierte Entscheidung treffen kannst, welche Methode für deinen Prototyp am besten geeignet ist.
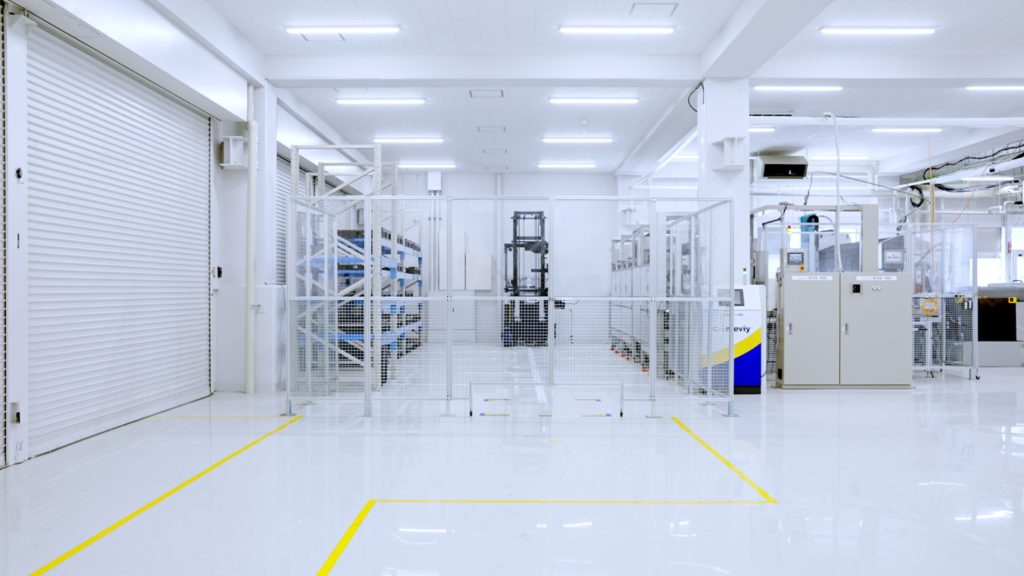
So funktionieren CNC Fräsen und 3D-Druck
CNC Fräsen: Ein subtraktives Verfahren
Bei der CNC Fräsen (Computerized Numerical Control) wird Material mit hoher Präzision durch spanende Werkzeuge wie Fräser, Drehmeißel oder Bohrer abgetragen. Ausgangspunkt ist meist ein massiver Rohling aus Metall oder Kunststoff, der schrittweise in die gewünschte Form gebracht wird. Dieses Verfahren eignet sich besonders für funktionale Bauteile mit hoher Festigkeit und engen Maßtoleranzen.
3D-Druck: Ein additives Verfahren
Im Gegensatz dazu arbeitet der 3D-Druck – auch als additive Fertigung bekannt – mit dem schichtweisen Aufbau von Material. Dabei entstehen Bauteile von Grund auf durch das schrittweise Auftragen einzelner Materiallagen. Zu den gängigen Verfahren zählen FDM (Fused Deposition Modeling), SLA (Stereolithografie) sowie metallbasierte Verfahren wie DMLS (Direct Metal Laser Sintering).
Fazit
Auch wenn beide Verfahren reale Prototypen hervorbringen, wirken sich die unterschiedlichen Ansätze – also Fräsen versus 3D-Druck – deutlich auf Faktoren wie Fertigungszeit, Kosten, Materialwahl und Konstruktionsfreiheit aus.
Materialvielfalt – Welche Werkstoffe sind einsetzbar?
CNC Fräsen
Die CNC Fräsen unterstützt eine breite Palette an Materialien, darunter:
Da bei der Bearbeitung die ursprünglichen mechanischen Eigenschaften der Werkstoffe erhalten bleiben, sind diese Materialien ideal für funktionale Tests geeignet.
3D-Druck
Die im 3D-Druck verwendbaren Materialien variieren stark je nach Verfahren:
- Kunststoffe: PLA, ABS, Nylon, PETG
- Harze: Standard, flexibel, hochtemperaturbeständig
- Metalle: Edelstahl, Aluminium, Titan (z. B. mittels DMLS oder SLM)
Allerdings erreichen gedruckte Bauteile in der Regel nicht die mechanische Leistungsfähigkeit von gefrästen Komponenten – insbesondere aufgrund der Schichtverklebung und möglichen Porosität im Aufbau.
Festigkeit, Dauerhaftigkeit und Oberflächenqualität
CNC-gefertigte Bauteile überzeugen in der Regel durch höhere Festigkeit und bessere Oberflächengüte im Vergleich zu 3D-gedruckten Teilen. Letztere ermöglichen hingegen komplexere Geometrien und generieren weniger Materialabfall. Wenn es um funktionsfähige Prototypen mit hoher mechanischer Belastbarkeit geht, bleibt die CNC Fräsen der Maßstab.
Präzision, Toleranzen und Oberflächengüte
CNC Fräsen
CNC Fräsen ist bekannt für ihre hohe Maßgenauigkeit – Toleranzen von bis zu ±0,01 mm sind möglich. Durch nachgelagerte Verfahren wie Polieren oder Eloxieren lassen sich zudem sehr feine Oberflächen erzielen. Diese Präzision ist insbesondere in der Luft- und Raumfahrt sowie bei der Entwicklung medizinischer Geräte unerlässlich.
3D-Druck
Der 3D-Druck bietet zwar ebenfalls eine gute Genauigkeit, ist aber durch die schichtweise Fertigung in seiner Auflösung begrenzt. Um Maßhaltigkeit und Oberflächenqualität zu verbessern, sind oft Nachbearbeitungsschritte wie Schleifen, Beschichten oder Aushärten erforderlich.
Anwendungsbeispiele: Bei Passprüfungen, Dichtflächen oder beweglichen Komponenten liefert die CNC Fräsen in der Regel die nötige Zuverlässigkeit.
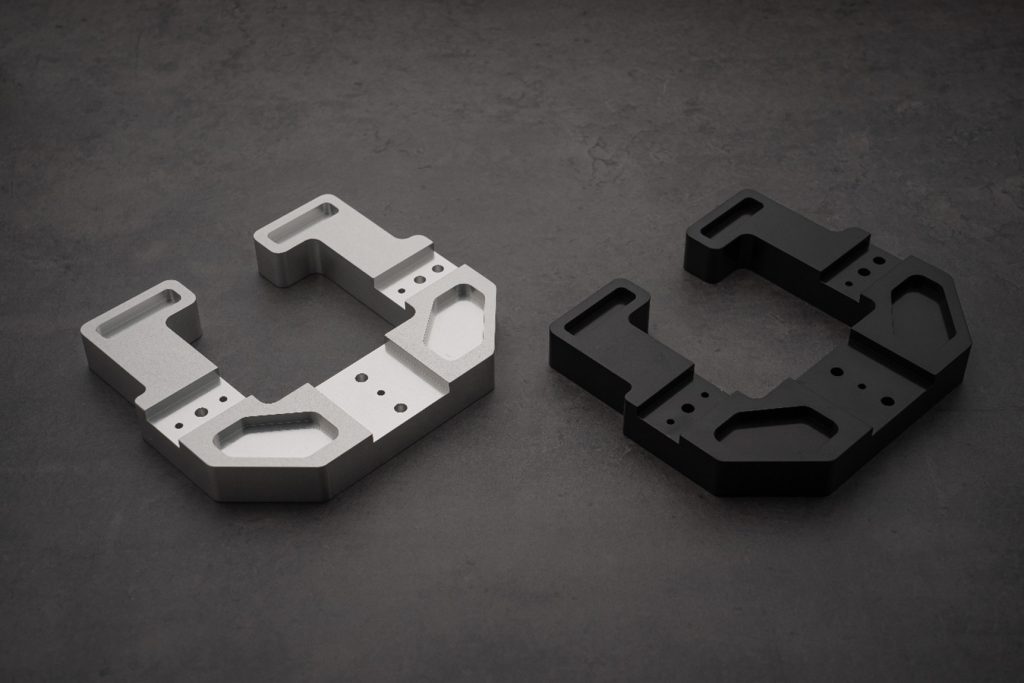
Geschwindigkeit und Fertigungsdauer
CNC Fräsen
- Vorteile: Schnelle Durchlaufzeiten bei einfachen Einzelprototypen
- Nachteile: Längere Rüstzeiten bei komplexen Bauteilen, insbesondere wenn spezielle Spannvorrichtungen oder Sonderwerkzeuge erforderlich sind
3D-Druck
- Vorteile: Optimal für schnelle Iterationen und Übernacht-Fertigung
- Nachteile: Langsamer bei großen oder mehreren Bauteilen – besonders bei metallbasierten Druckverfahren
Für Unternehmen, die ihre Produkte möglichst schnell zur Marktreife bringen wollen, hängt die passende Wahl stark von der Bauteilkomplexität und der Anzahl benötigter Iterationen ab.
Kostenvergleich – Welche Methode ist im Prototyping wirtschaftlicher?
CNC Fräsen
Die CNC Fräsen bringt in der Regel höhere Rüst- und Materialkosten mit sich – insbesondere bei metallischen Werkstoffen. Zudem fällt durch das spanende Verfahren vergleichsweise viel Abfall an, was die Gesamtkosten zusätzlich erhöht.
3D-Druck
Beim 3D-Druck punkten vor allem kleine Stückzahlen und komplexe Geometrien, die sich mit konventioneller Bearbeitung nur schwer oder kostspielig realisieren lassen. Hier ist die Methode oft deutlich effizienter.
Versteckte Kosten, die berücksichtigt werden sollten:
- Werkzeugkosten (CNC)
- Nachbearbeitung (bei beiden Verfahren)
- Wartung und Fehldrucke (3D-Druck)
Für größere Prototypenserien oder bei teuren Materialien kann CNC trotz höherer Einmalkosten langfristig die wirtschaftlichere Lösung sein.
Vorteile der CNC Fräsen
Auch wenn bei der CNC Fräsen gewisse Einschränkungen hinsichtlich Werkzeugzugänglichkeit und Achsenausrichtung bestehen, haben moderne Mehrachsmaschinen und fortschrittliche Werkzeugbahnen den Gestaltungsspielraum erheblich erweitert. Merkmale wie komplexe Konturen, präzise Bohrungen oder feine Oberflächendetails lassen sich heute mit höchster Genauigkeit realisieren. Besonders bei Bauteilen, bei denen es auf enge Toleranzen in funktionskritischen Bereichen ankommt, spielt CNC ihre Stärken voll aus – Anforderungen, mit denen additive Verfahren häufig an ihre Grenzen stoßen.
Für Baugruppen, die eine hohe Wiederholgenauigkeit, passgenaue Verbindungen oder bewegliche Komponenten erfordern, bietet die CNC Fräsen eine ausgezeichnete Maßhaltigkeit und Prozessstabilität.
Gestaltungsmöglichkeiten im 3D-Druck
Der 3D-Druck eröffnet deutlich mehr Freiheiten bei der Konstruktion von innenliegenden Kanälen, Gitterstrukturen oder organisch geformten Geometrien – und das ganz ohne aufwändige Werkzeuge oder Vorrichtungen. Dadurch eignet sich das Verfahren besonders gut für frühe Konzeptmodelle oder leichte, nicht funktionskritische Bauteile.
Diese gestalterische Freiheit geht jedoch oft zulasten von Maßgenauigkeit, Materialhomogenität und Oberflächenqualität – Aspekte, die in späteren Prototypenphasen häufig eine Nachbearbeitung erforderlich machen. Spätestens hier wird CNC Fräsen zur bevorzugten Methode.
Festigkeit und Haltbarkeit von Prototypen
CNC gefräste Bauteile
CNC-Frästeile weisen in der Regel eine höhere Festigkeit und Lebensdauer auf, da sie die volle strukturelle Integrität des Ausgangsmaterials beibehalten. Das ist besonders wichtig bei Tests unter mechanischer Belastung, bei thermischen Anforderungen oder im Kontakt mit Chemikalien.
3D-gedruckte Bauteile
Bauteile aus dem 3D-Druck – insbesondere im FDM- oder SLA-Verfahren – neigen zu Schichtablösungen und bieten eine geringere Schlagzähigkeit. Metallbasierter 3D-Druck liefert zwar bessere Ergebnisse, ist jedoch deutlich kostenintensiver.
Auch die Materialwahl hat großen Einfluss auf die Belastbarkeit: Werkstoffe wie Aluminium oder POM (bei CNC) schneiden in Funktionstests deutlich besser ab als PLA oder Kunststoffe aus dem 3D-Druck.
Aspekt | CNC-Fräsen | 3D-Druck |
---|---|---|
Verfahrenstyp | Subtraktiv | Additiv |
Unterstützte Materialien | Metalle (Aluminium, Stahl, Edelstahl, Kupfer), Kunststoffe (ABS, POM, PPS, MC-Nylon) | Kunststoffe (PLA, ABS, Nylon, PETG), Harze (Standard, flexibel, hochtemperaturbeständig), Metalle (Edelstahl, Aluminium, Titan via DMLS/SLM) |
Materialeigenschaften | Erhält die ursprünglichen mechanischen Eigenschaften und Festigkeiten | Häufig geringere Festigkeit durch Schichtverklebung und Porosität |
Festigkeit & Haltbarkeit | Höhere Festigkeit und Langlebigkeit – geeignet für Funktionstests und mechanische Belastungen | Geringere Stabilität, anfällig für Schichtablösung – besser für leichte oder nicht-funktionale Bauteile |
Präzision & Toleranzen | Hohe Präzision, enge Toleranzen (±0,01 mm), sehr gute Oberflächengüte möglich | Begrenzte Auflösung durch Schichtbauweise, Nachbearbeitung oft erforderlich |
Oberflächenqualität | Hochwertige Oberflächen durch Polieren oder Eloxieren erreichbar | Raue Oberfläche; Verbesserung durch Schleifen, Beschichten oder Aushärten nötig |
Geschwindigkeit & Fertigungszeit | Schnell bei einfachen Teilen; längere Rüstzeit bei komplexen Geometrien oder Sonderwerkzeugen | Ideal für schnelle Iterationen; langsamer bei großen oder mehreren Metallteilen |
Kostenaspekte | Höhere Rüst- und Materialkosten; mehr Materialabfall | Kosteneffizient bei kleinen Stückzahlen und komplexen Formen; potenzielle Zusatzkosten durch Nachbearbeitung oder Fehldrucke |
Designkomplexität | Gut geeignet für komplexe Konturen, präzise Bohrungen und Passungen; begrenzt durch Werkzeugzugang (aber zunehmend verbessert) | Große Gestaltungsfreiheit für organische Formen, innenliegende Kanäle, Gitterstrukturen |
Typische Anwendungsfälle | Funktionale Prototypen mit hohen Anforderungen an Festigkeit, Maßhaltigkeit und Wiederholgenauigkeit | Konzeptmodelle in der Frühphase, Leichtbauteile mit komplexer Geometrie |
Zentrale Vorteile | Überlegene Festigkeit, Maßgenauigkeit und Zuverlässigkeit bei mechanischen, thermischen und chemischen Belastungstests | Große Gestaltungsfreiheit, weniger Materialabfall, schnelle Iterationszyklen |
Einschränkungen | Höherer Aufwand und höhere Kosten bei komplexen Teilen; begrenzt durch Werkzeugzugänglichkeit | Geringere mechanische Eigenschaften, eingeschränkte Oberflächengüte, langsamer bei größeren Metallserien |
Welche Methode passt am besten zu deinem Prototyping-Bedarf?
Hier eine kompakte Entscheidungshilfe:
CNC Fräsen ist die richtige Wahl, wenn:
- hohe Präzision und enge Toleranzen erforderlich sind
- der Prototyp funktionalen oder mechanischen Belastungstests standhalten muss
- du mit metallischen Werkstoffen oder technischen Kunststoffen arbeiten willst
3D-Druck ist ideal, wenn:
- schnelle und kostengünstige Iterationen im Vordergrund stehen
- das Design komplexe oder organische Geometrien umfasst
- Budget und Geschwindigkeit wichtiger sind als maximale Festigkeit
Hybrider Ansatz
In vielen Fällen bietet sich eine kombinierte Strategie an: frühe Iterationen werden im 3D-Druck realisiert, die finale Validierung erfolgt dann über CNC Fräsen – als Vorbereitung für die spätere Serienfertigung.
Fazit
Sowohl die CNC Fräsen als auch der 3D-Druck sind aus dem modernen Prototypenbau nicht mehr wegzudenken – beide Verfahren haben ihre eigenen Stärken, abhängig von den jeweiligen Anforderungen.
CNC überzeugt durch höchste Präzision und Materialfestigkeit und ist damit ideal für leistungsfähige Funktionsprototypen. Der 3D-Druck hingegen punktet mit Flexibilität und Gestaltungsfreiheit – perfekt für schnelle Iterationen und komplexe Geometrien.
Welche Methode die bessere ist? Das hängt ganz von deinem Budget, dem Zeitrahmen und den Zielen deines Designs ab.
Was ist meviy?
meviy ist eine KI-gestützte On-Demand-Fertigungsplattform, entwickelt von MISUMI. Sie ermöglicht es Ingenieurinnen und Ingenieuren, 3D-CAD-Modelle hochzuladen und in Echtzeit Angebote, automatische Fertigbarkeitsanalysen sowie Angaben zu Lieferzeiten zu erhalten.
Unterstützt werden Fertigungsverfahren wie CNC-Fräsen, CNC-Drehen und Blechbearbeitung – wodurch meviy den Beschaffungsprozess deutlich vereinfacht, Kommunikationsaufwände reduziert und die Produktentwicklung spürbar beschleunigt.