BLOG » What is a Mould? Understanding Its Structure and Key Points
What is a Mould? Understanding Its Structure and Key Points
When it comes to manufacturing plastic parts, moulds play a pivotal role in shaping raw materials into finished goods. But what exactly is a mould, and how does it work? In this guide, we will delve into the intricacies of mould structures, their various components, and key terminology associated with injection moulding.
What is a Mould?
A mould is a “form” used to shape molten resin. For plastic processing, moulds are typically made of metal, hence the term “metal mould.”
Moulds are manufactured through a precise and intricate process that involves several key steps. Initially, a mould design is created using CAD (Computer-Aided Design) software, ensuring that the mould will produce parts that meet the required specifications. The design is then translated into a CNC (Computer Numerical Control) program, which directs the machining of the mould components from blocks of metal, typically aluminium or alloy steels like pre-hardened steel and stainless steel.
High-precision milling, drilling, and EDM (Electrical Discharge Machining) are used to shape the mould cavities and cores. Once machined, the mould components are polished and assembled, with additional elements such as cooling channels, ejector pins, and guide pins integrated. Finally, the assembled mould undergoes rigorous testing and fine-tuning to ensure it produces accurate and high-quality parts.
Basic Structure of a Mould
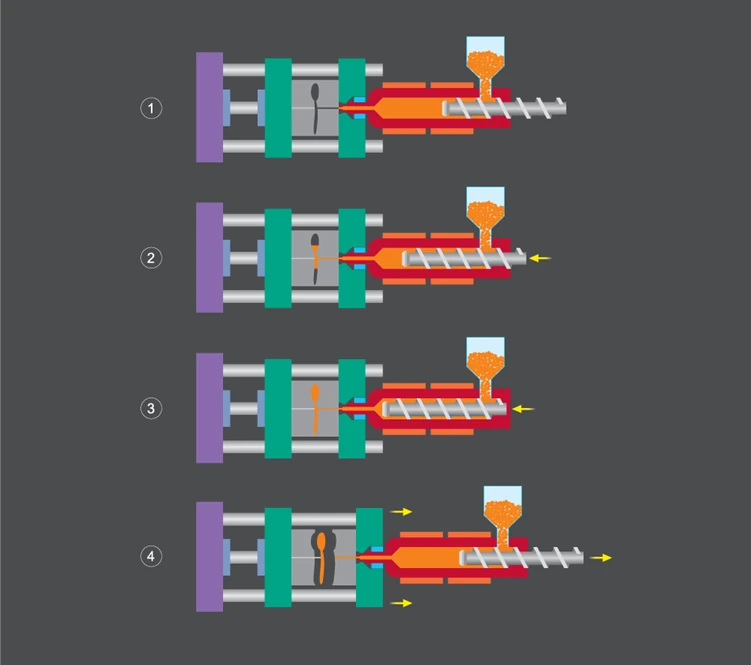
The basic structure of a mould consists of two main components: the cavity and the core. The cavity shapes the exterior of the part and remains stationary. The core forms the interior and features movable elements like ejector pins that push the finished product out of the mould once it has cooled and solidified.
Inside the mould, cooling channels are strategically integrated to regulate the temperature during the injection process, ensuring uniform solidification and minimizing defects. The runners and gates are essential pathways that guide the molten material from the injection nozzle into the mould cavity, designed to fill the mould efficiently and reduce waste.
Furthermore, advanced moulds may include features such as sliders and lifters to create complex geometries and undercuts that a simple two-part mould cannot achieve. These additional components move in coordination with the opening and closing of the mould to form intricate details and then retract to allow the part to be ejected smoothly.
Overall, the design and structure of a mould are critical to the efficiency and quality of the manufacturing process, ensuring that each product meets exact specifications with high repeatability. Understanding these intricate details of mould construction is essential for optimizing production and achieving superior results in injection moulding.
Considerations While Using Moulds
When using moulds to manufacture custom resin materials, several main points of concern must be addressed to ensure high-quality output.
First, the precision of mould design is crucial, as any inaccuracies can lead to defects in the final product. This includes careful consideration of the cavity and core alignment, cooling channels, and the placement of gates and runners to ensure even material flow.
Additionally, the choice of mould material impacts durability and the quality of the finished product, with hardened steel often preferred for its longevity.
Proper maintenance and regular inspection of the mould are also essential to prevent wear and tear that could affect production efficiency.
Temperature control within the mould is another critical factor, as inconsistent cooling can lead to warping or incomplete filling of the resin.
Finally, understanding the properties of the resin used, such as its shrinkage rate and viscosity, helps in adjusting the mould design and process parameters to achieve the desired precision and finish.
Conclusion
Injection Moulds are sophisticated tools with various components working together to shape resin into final products. By understanding the terms and mechanisms involved, you can better appreciate the complexity and precision of mould-making. Observing everyday plastic products with this knowledge can reveal interesting details about their manufacturing process.