BLOG » PP Resin vs. ABS vs. MC Nylon: Which Plastic is Best for Your Engineering Needs?
PP Resin vs. ABS vs. MC Nylon: Which Plastic is Best for Your Engineering Needs?
When it comes to selecting materials for engineering projects, choosing the right plastic is crucial. Plastics are often preferred for their versatility, cost-effectiveness, and durability. Among the many options available, PP Resin, ABS, and MC Nylon are popular choices due to their distinct properties and applications.
In this article, we’ll compare PP Resin, ABS, and MC Nylon based on their properties, benefits, applications, and suitability for different engineering needs.
What is PP Resin?
PP Resin (Polypropylene) is a thermoplastic polymer known for its robustness and resistance to chemical degradation. It’s lightweight, has a high melting point, and offers excellent resistance to fatigue, which makes it ideal for applications requiring longevity and durability.
Key features include:
- High chemical resistance, especially to acids and bases.
- Lightweight and relatively low cost.
- Good impact strength at room temperature.
- High resistance to fatigue.
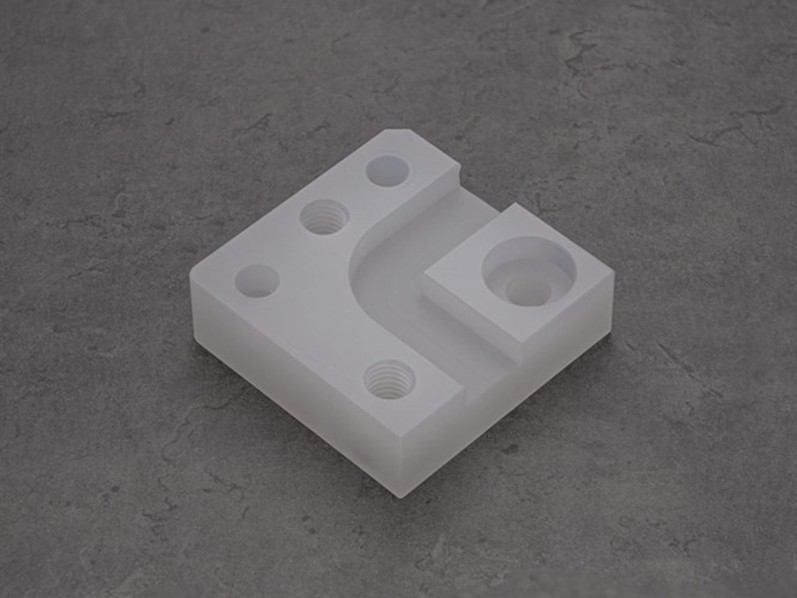
Applications of PP Resin in Engineering
PP Resin is widely used in applications where durability, chemical resistance, and cost-effectiveness are paramount. Common industries that utilise PP Resin include:
- Automotive: Used for interior components, bumpers, and fuel tanks.
- Packaging: Containers, bottles, and films.
- Medical: Medical device components such as syringes, containers, and diagnostic equipment.
What is ABS?
ABS (Acrylonitrile Butadiene Styrene) is a strong, tough, and versatile thermoplastic known for its excellent impact resistance. It has a smooth finish, making it easy to process and mould. ABS is also known for its good electrical insulation properties.
Key features include:
- High impact resistance and strength.
- Excellent surface finish with good paintability.
- Good dimensional stability.
- Resistance to heat and low temperatures.
Applications of ABS in Engineering
ABS is widely used in engineering applications requiring high impact resistance and strength, as well as aesthetic appeal. Common uses include:
- Automotive: Dashboard panels, interior components, and exterior parts.
- Electronics: Housings for consumer electronics like televisions, computers, and mobile phones.
- Industrial: Machine parts, tools, and housings for machinery.
What is MC Nylon?
MC Nylon (Moulded Cast Nylon) is a high-performance plastic known for its exceptional wear resistance and low friction properties. It’s often used in applications where parts need to withstand heavy wear or operate in harsh environments. MC Nylon has better dimensional stability than other nylons, making it suitable for precision components.
Key features include:
- Excellent wear resistance and self-lubricating properties.
- High mechanical strength and toughness.
- Good chemical resistance, though less than PP Resin and ABS.
- Exceptional resistance to abrasion and moisture.
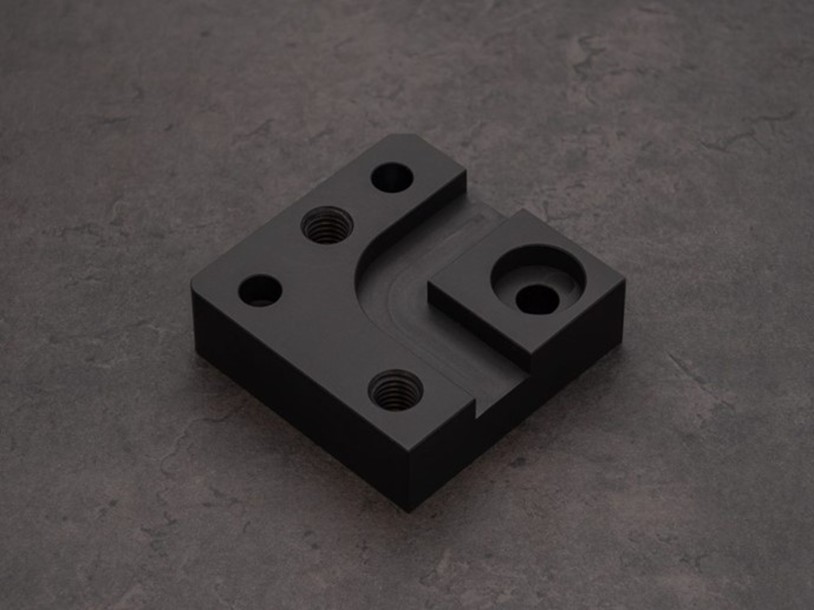
Applications of MC Nylon in Engineering
MC Nylon is a preferred material for applications that require low friction, high wear resistance, and long-lasting performance. Some typical applications include:
- Automotive: Bearings, bushings, and gears.
- Industrial: Conveyor belts, wear strips, and cutting blades.
- Aerospace: Components that need to withstand high mechanical stress and wear.
Comparing PP Resin, ABS, and MC Nylon
Durability and Strength
When comparing the durability and strength of these plastics, MC Nylon stands out for its superior wear resistance and toughness, making it ideal for high-stress and high-wear applications. ABS offers excellent impact resistance but is generally less resistant to wear than MC Nylon. PP Resin, while durable, is more commonly used in applications where chemical resistance and fatigue resistance are more important than mechanical strength.
- MC Nylon: Best for wear-resistance, toughness, and long-lasting performance.
- ABS: Superior impact resistance, good for structural components.
- PP Resin: Great for chemical resistance and light-duty applications.
Cost-Effectiveness
In terms of cost, PP Resin is the most cost-effective option due to its lower production cost. ABS is generally more expensive than PP Resin but still relatively affordable. MC Nylon, on the other hand, tends to be the most expensive due to its enhanced performance properties and the cost of its manufacturing process.
- PP Resin: Most cost-effective.
- ABS: Mid-range cost.
- MC Nylon: Highest cost due to superior wear and performance features.
Processing and Moulding Ease
All three plastics are relatively easy to process, though ABS is often the easiest to mould due to its excellent flow properties and low melting point. PP Resin requires a higher processing temperature, making it slightly more challenging to mould. MC Nylon, while easy to machine, requires more precise control in the moulding process due to its dimensional stability.
- ABS: Best for ease of moulding and processing.
- PP Resin: Requires higher processing temperature.
- MC Nylon: Ideal for machining, but needs careful moulding for precision.
Environmental Impact and Sustainability
In terms of environmental sustainability, PP Resin is often considered the most eco-friendly of the three due to its recyclability and low environmental impact. ABS and MC Nylon are both less biodegradable and more challenging to recycle, but they can still be processed for reuse in certain applications.
- PP Resin: Most eco-friendly and recyclable.
- ABS: Moderate environmental impact, recyclable.
- MC Nylon: Less eco-friendly, more challenging to recycle.
How to Choose the Right Plastic for Your Engineering Project
Factors to Consider
Selecting the right plastic depends on several key factors:
- Mechanical properties: Consider the load-bearing capacity and impact resistance required.
- Chemical exposure: Determine which material offers the best resistance to the chemicals in your environment.
- Cost limitations: Choose a plastic that fits within your budget while meeting performance needs.
Applications Best Suited for Each Plastic
- PP Resin: Best for chemical-resistant applications, packaging, and medical components.
- ABS: Ideal for products requiring high impact resistance and excellent surface finish.
- MC Nylon: Perfect for heavy-duty engineering components that experience wear and friction.
Property | PP Resin | ABS | MC Nylon |
Full Name | Polypropylene | Acrylonitrile Butadiene Styrene | Monomer Casting Nylon (typically Nylon 6) |
Type | Semi-crystalline thermoplastic | Amorphous thermoplastic | Semi-crystalline engineering plastic |
Structure | Homopolymer or copolymer | Terpolymer | Cast polymer, often self-lubricating |
Tensile Strength | Low to moderate (~30 MPa) | Moderate (~40–50 MPa) | High (~70–90 MPa) |
Impact Resistance | Good | Very good | Very good |
Hardness (Shore D) | ~70 | ~100 | ~80–85 |
Stiffness | Low | Moderate | High |
Wear Resistance | Moderate | Moderate | Excellent |
Heat Resistance (HDT) | ~100–110°C | ~90–100°C | ~120–130°C |
Melting Point | ~160–170°C | No true melting point (amorphous) | ~220°C |
Thermal Stability | Moderate | Moderate | Good |
Durability & Strength | Good fatigue resistance, lower mechanical strength | High impact resistance, good structural strength | Exceptional wear resistance, high mechanical strength |
Chemical Resistance | Excellent, resistant to acids and bases | Moderate, less resistant to strong acids/bases | Good, but less resistant than PP Resin |
Wear & Friction Resistance | Moderate | Moderate | Excellent, self-lubricating |
Processing & Moulding Ease | Requires high processing temperature | Easiest to mould and process | Requires precision machining |
Cost | Low (most affordable) | Moderate | High (most expensive) |
Environmental Impact | Highly recyclable, eco-friendly | Recyclable but less sustainable | Less recyclable, higher environmental impact |
Common Applications | Automotive, packaging, medical | Electronics, automotive, industrial parts | Heavy-duty engineering, aerospace, automotive gears |
Conclusion
Each of these plastics has its own unique set of advantages, making them suited to specific engineering needs. PP Resin is best for cost-effective, chemical-resistant applications; ABS excels in high-impact, aesthetic applications; and MC Nylon is the material of choice for high-wear, precision components. The best plastic for your engineering project will depend on your specific requirements, including strength, durability, cost, and environmental impact. By considering these factors, you can ensure you choose the right material for your needs.