BLOG » CNC Machining Prototype Service – Precision Prototyping for Faster Product Development
CNC Machining Prototype Service – Precision Prototyping for Faster Product Development
In today’s fast-paced product development landscape, CNC machining prototype services play a vital role in bringing concepts to life with speed and precision. Whether you’re in the early stages of design or preparing for functional testing, CNC machining offers a reliable path to high-quality, production-grade prototypes.
This subtractive manufacturing method has become a go-to solution for engineers and product developers seeking accurate, repeatable results using real engineering materials. Its advantages lie in exceptional dimensional accuracy, broad material compatibility, and rapid turnaround times—all essential for reducing time-to-market.
CNC prototype machining supports various industries, including aerospace, automotive, medical device manufacturing, robotics, and consumer electronics, where precision and material integrity are paramount. From visual mock-ups to functional assemblies, CNC machining ensures that each prototype meets stringent industrial requirements.
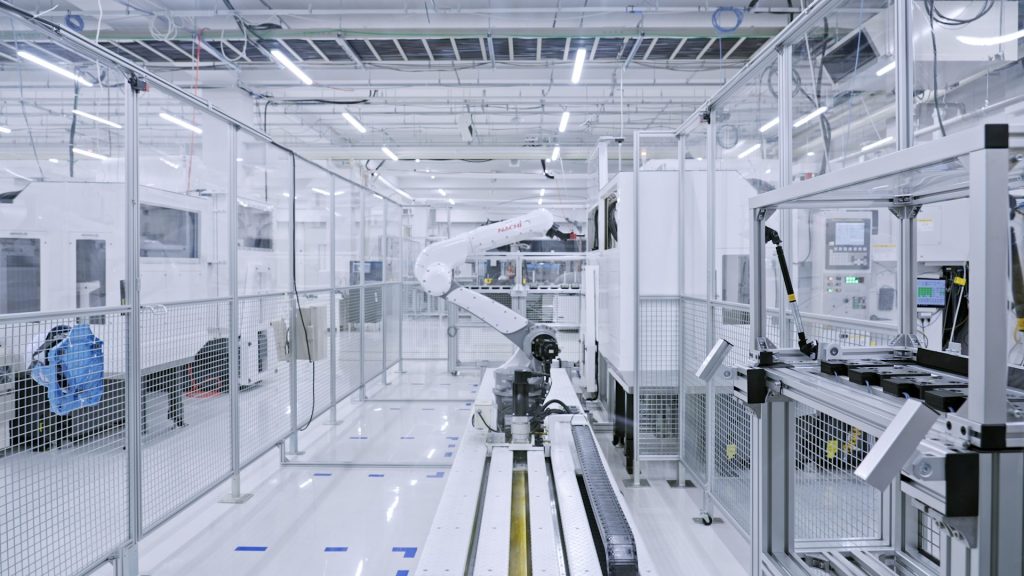
Why Choose CNC Machining for Prototyping?
CNC (Computer Numerical Control) machining is ideal for prototyping due to its exceptional accuracy, repeatability, and consistency. Unlike manual machining or less precise methods, CNC systems operate on CAD/CAM input, ensuring every cut, drill, or surface is produced to tight tolerances.
Material flexibility is another core advantage. CNC machining accommodates a wide array of materials—ranging from metals like aluminium and titanium to plastics such as ABS and nylon. This enables engineers to test prototypes under real-world conditions using production-grade materials.
When it comes to lead times, CNC machining significantly outpaces processes like injection moulding or casting, which require tooling. Even compared to additive methods like 3D printing, CNC machining delivers faster results for high-tolerance parts, especially when post-processing is required for visual or functional accuracy.
How CNC Machining Prototype Services Work
A typical CNC machining prototype service follows a well-defined, engineer-driven workflow:
- CAD Modelling: Everything begins with a 3D design, usually created using CAD software such as SolidWorks or Fusion 360. This model is translated into machine code (G-code) using CAM software.
- Material Selection: Based on part function, aesthetics, or testing requirements, the ideal material is selected. Providers offer a wide choice of metals and plastics.
- Machining Operations: Using milling, turning, or EDM, the CNC machine cuts the raw material into the desired shape, following the G-code instructions with micron-level precision.
- Finishing: Prototypes may undergo secondary processes like deburring, anodising, or plating to meet surface finish requirements or mimic final production parts.
Tolerances and surface finishes are particularly critical during prototyping. For functional parts, tight tolerances (±0.01 mm or better) ensure proper fit, especially in mechanical assemblies. High-quality surface finishes are vital for testing visual prototypes or medical components.
Common challenges include tool wear, complex geometries, or hard-to-machine materials. Professional services overcome these with toolpath optimisation, multi-axis machines, and experienced machinists who fine-tune the process for prototype success.
CNC Machining vs. 3D Printing for Prototyping
While 3D printing has gained popularity in recent years, CNC machining remains indispensable for prototyping under real engineering conditions.
Feature | CNC Machining | 3D Printing |
---|---|---|
Precision | High (±0.01 mm) | Moderate (±0.1 mm) |
Material Range | Extensive (metals, plastics) | Mostly plastics and resins |
Surface Finish | Excellent | Often requires post-processing |
Structural Strength | High | Lower due to layered construction |
Speed | Fast for small batches | Fast for simple designs |
Cost | Higher per unit, lower for functional parts | Lower for conceptual parts |
Choose CNC machining when you require:
- Precise mechanical properties
- High-quality surface finishes
- Functional testing under stress or heat
3D printing may be more appropriate for visual mock-ups, rapid design iterations, or complex internal geometries.
In terms of cost, 3D printing may initially appear cheaper. However, CNC machining proves more cost-effective for functional prototypes that must simulate production performance or withstand mechanical testing.
Best Materials for CNC Prototype Machining
The material selected significantly influences the prototype’s performance and accuracy. Here’s an overview of the most commonly used materials:
Metals
- Aluminium (EN AW-6061 equiv., EN AW−5052 equiv.): Lightweight, corrosion-resistant, and easily machinable. Ideal for aerospace, automotive, and consumer electronics.
- Stainless Steel (EN 1.4301 equiv., EN 1.4401 equiv.): Strong, corrosion-resistant, suitable for medical devices and structural parts.
- Brass: Good electrical conductivity and excellent machinability. Often used for fittings, valves, and decorative parts.
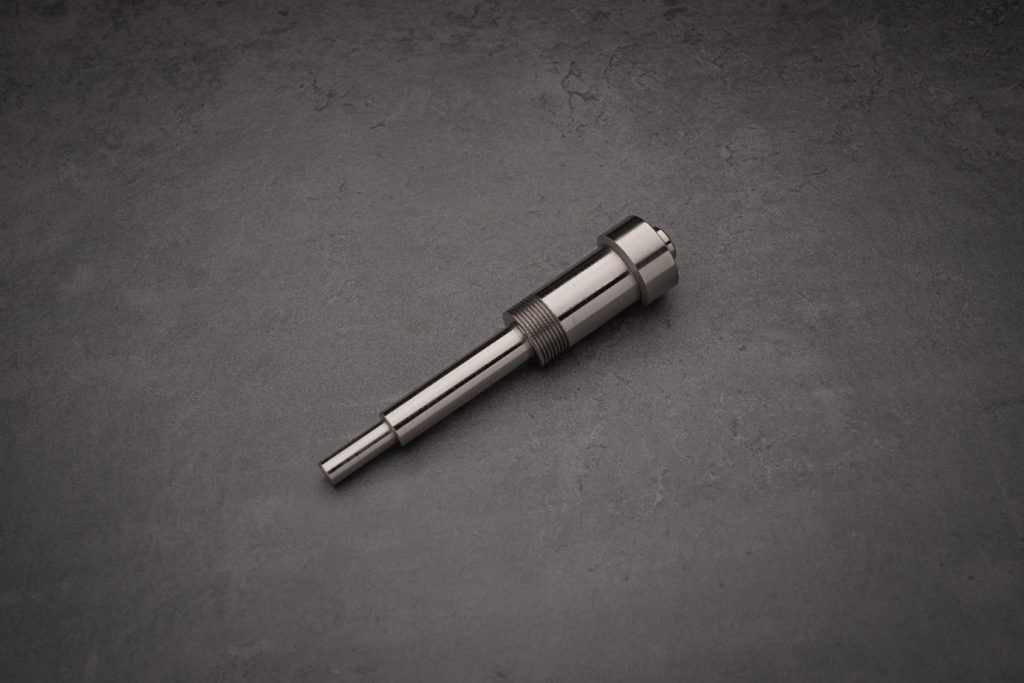
Plastics
- ABS: Durable and impact-resistant. Common in automotive and consumer products.
- PEEK: High-performance thermoplastic with chemical and heat resistance. Perfect for aerospace and medical components.
- Nylon: Tough and wear-resistant. Used for bushings, gears, and functional enclosures.
- Polycarbonate: A transparent plastic known for its impact resistance, clarity, and durability. Ideal for optical parts, safety enclosures, and components requiring both strength and visibility.
Each material’s properties—such as strength, weight, machinability, and thermal resistance—determine its suitability for different prototyping applications.
Choosing the Right CNC Machining Prototype Service Provider
Not all CNC providers are created equal. When selecting a machining prototype service, consider the following factors:
- Expertise & Technical Capabilities: Ensure the provider has experience with your material type and geometry. Multi-axis machines and post-processing options are a plus.
- Lead Times: Fast turnaround is essential for iterative prototyping. Ask about standard and expedited lead times. meviy, for istance, offers an extremely reliable delivery service, with multiple lead time options: from a more relaxed economy shipping, to faster solutions like express and rapid shipping.
- Pricing Transparency: Look for clear quotations that include setup, tooling, material, and finishing costs.
- Quality Assurance: ISO certifications and documented quality control processes ensure consistent results.
How to Reduce CNC Prototype Costs Without Compromising Quality
Prototyping budgets can be optimised by applying several strategic approaches:
- Design for Manufacturability (DFM): Simplify geometry, reduce undercuts, and avoid features that require custom tooling.
- Material Selection: Choose cost-effective alternatives during early testing phases. For instance, aluminium can replace more expensive materials for basic mechanical tests.
- Right Machining Method: Match the process to the part—use turning for cylindrical parts, milling for flat or contoured surfaces, and EDM for intricate internal geometries.
Working with a knowledgeable provider early in the design stage can result in cost-effective, manufacturable prototypes without sacrificing function or appearance.
Conclusion
CNC machining remains a cornerstone of rapid product development, offering unmatched precision, material versatility, and fast turnaround. From single-piece functional parts to fully assembled prototypes, CNC machining bridges the gap between concept and production.
If you’re seeking a reliable, high-precision machining prototype service, partner with experts who understand your industry and engineering challenges.
Ready to get started? Contact us today to discuss your prototyping requirements and get a custom CNC quote tailored to your needs.