BLOG » PPS Resin in Mechanical Engineering: Material Overview
PPS Resin in Mechanical Engineering: Material Overview
PPS (Polyphenylene Sulphide) resin is gaining ground in mechanical engineering as a high-performance alternative to more commonly used materials such as MC Nylon, ABS, and PP. Known for its outstanding chemical resistance, dimensional stability, and heat tolerance, PPS is being adopted in applications where other engineering resins fall short. As manufacturers demand greater durability and performance under extreme conditions, PPS resin is proving itself as a reliable solution in industries ranging from automotive to electronics.
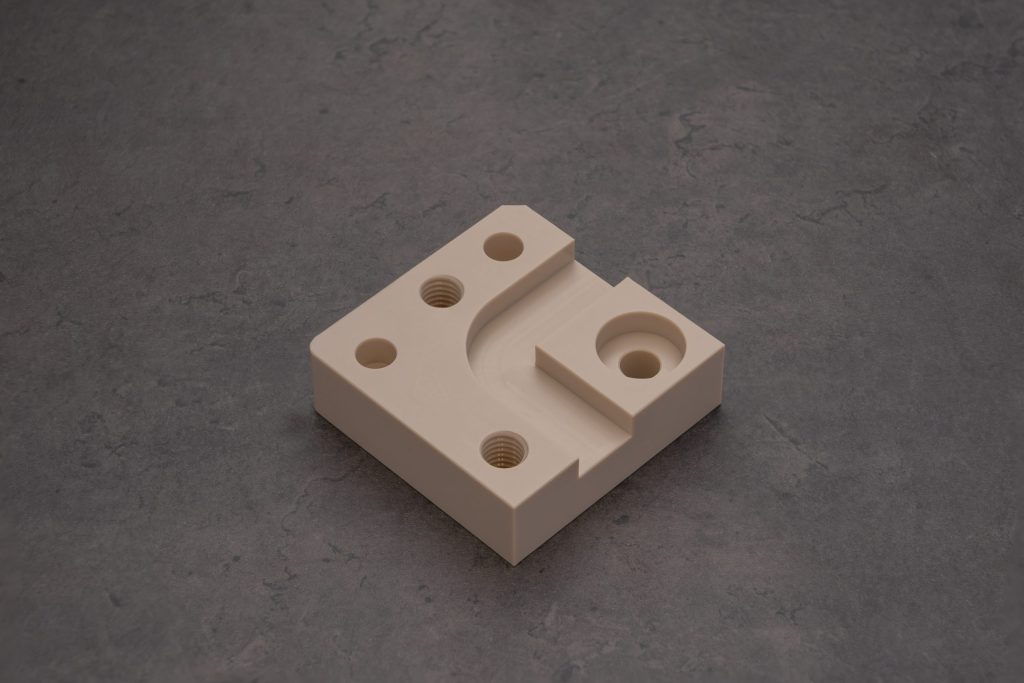
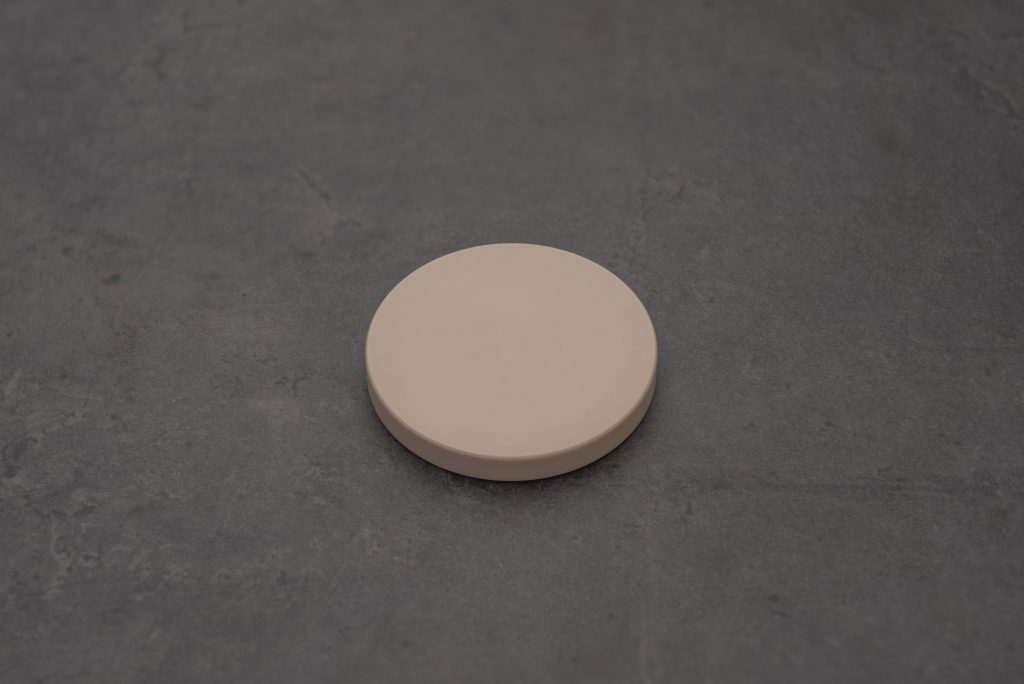
PPS is a semi-crystalline, high-performance thermoplastic resin known for its rigidity, flame retardancy, and resistance to solvents and chemicals. It performs reliably in high-temperature environments, withstanding continuous service temperatures of 220°C or more without losing structural integrity. PPS is available in several grades, including glass-fibre reinforced versions for enhanced strength and creep resistance. Thanks to its stable molecular structure, it exhibits minimal moisture absorption and exceptional dimensional precision.
PPS vs MC Nylon: Key Performance Differences
While MC Nylon (monomer casting nylon) is widely used due to its low cost, high machinability, and good wear properties, it has limitations in high-temperature and chemically aggressive environments. In comparison:
- Thermal Resistance: PPS can handle temperatures above 200°C, while MC Nylon softens at around 120°C.
- Chemical Resistance: PPS resists fuels, oils, and acids, unlike MC Nylon, which is more susceptible to degradation.
- Moisture Absorption: MC Nylon absorbs water and can swell or deform over time; PPS maintains dimensional stability even in humid environments.
- Mechanical Stability: PPS maintains its rigidity and tensile strength over a wider temperature range.
For components requiring long-term stability in harsh operating conditions, PPS is often the superior choice.
PPS vs ABS and PP: Performance and Applications
Compared to general-purpose resins like ABS (Acrylonitrile Butadiene Styrene) and PP (Polypropylene), PPS offers dramatically enhanced performance:
- Heat Resistance: ABS deforms around 100°C, and PP around 90°C. PPS outperforms both with its high-temperature endurance.
- Chemical Resistance: PPS withstands aggressive solvents and industrial fluids, unlike ABS which is sensitive to many chemicals.
- Strength and Rigidity: PPS is significantly stiffer and stronger than both ABS and PP, making it suitable for structural applications.
- Dimensional Accuracy: PPS resists warping and creep, making it ideal for precision mechanical parts where tolerance is critical.
While ABS and PP remain cost-effective for less demanding applications, PPS resin is a go-to material when performance cannot be compromised.
Material Properties Comparison
Property | PPS (Polyphenylene Sulfide) | ABS (Acrylonitrile Butadiene Styrene) | MC Nylon | PP (Polypropylene) |
Thermal Resistance | Up to 260°C | Up to 100°C | Up to 150°C | Up to 100°C |
Chemical Resistance | Excellent (Acids, Bases, Solvents) | Moderate (Acids, Bases) | Good (Organic Solvents, Acids) | Good (Alkaline Solutions, Acids) |
Tensile Strength | >100 MPa | 40–70 MPa | 50–80 MPa | 30–50 MPa |
Impact Strength | Low | High | Moderate | Low |
Flexibility | Low | Moderate | High | Moderate |
Moisture Absorption | Very Low | Moderate | High | Low |
Electrical Insulation | Excellent | Good | Moderate | Good |
Common Applications | Electrical Components, Automotive, Aerospace | Consumer Goods, Automotive, Electrical Enclosures | Automotive, Industrial Applications, Wear-resistant Parts | Packaging, Consumer Goods, Medical Devices |
CNC Machining of PPS Resin
PPS is well-suited for CNC machining thanks to its stability, minimal thermal expansion, and low moisture uptake. Engineers should be aware that some grades, especially unfilled PPS, may be brittle and require care when clamping or during sharp transitions.
For optimal results:
- Use sharp, coated tools to minimise friction and heat build-up.
- Apply adequate cooling and chip evacuation to prevent surface burning.
- Consider annealing for parts with tight tolerances or complex geometries.
PPS machining enables the production of high-precision parts with excellent consistency and surface quality.
Applications of PPS Resin
PPS is used extensively across industries where heat, chemical resistance, and dimensional accuracy are critical:
- Automotive: fuel system components, sensors, and electrical connectors
- Aerospace: lightweight, high-performance structural parts
- Electronics: insulating components, switches, and terminal blocks
- Mechanical Engineering: gears, bushings, and wear-resistant sliding parts
Its reliability under stress and extreme temperatures makes it ideal for performance-critical applications.
When to Choose PPS Resin
Engineers should consider PPS resin when the application demands:
- Long-term exposure to high temperatures or chemicals
- Tight dimensional tolerances with minimal post-machining distortion
- Enhanced strength and rigidity in confined spaces
- Flame retardant properties
Though more expensive than basic engineering resins, PPS provides cost-effectiveness in the long term due to its durability and reduced failure rates.
Conclusion
PPS resin is an advanced material option for engineers seeking high-performance alternatives to MC Nylon, ABS, or PP. It offers superior heat resistance, dimensional stability, and chemical durability—qualities essential for next-generation applications. As manufacturing moves towards more demanding environments and tighter tolerances, PPS stands out as a resin that meets both performance and reliability requirements.
What is meviy?
meviy is an AI-powered on-demand manufacturing platform developed by MISUMI. It allows engineers to upload 3D CAD models and receive instant quotations, automatic manufacturability analysis, and lead time estimates. Supporting processes like CNC machining, sheet metal fabrication, and 3D printing, Meviy streamlines procurement, reduces communication loops, and accelerates product development. Its AI capabilities also enable part recognition, interactive design editing, and compatibility with a wide range of materials—making it a smart, fast, and reliable tool for today’s engineering teams.