BLOG » Hard Anodising Process: How to Enhance Aluminium
Hard Anodising Process: How to Enhance Aluminium
Aluminium is one of the most versatile and widely used metals across industries, known for its light weight, corrosion resistance, and excellent conductivity. However, its natural surface can sometimes fall short when it comes to extreme conditions. That’s where hard anodising comes in. This advanced surface treatment process enhances the properties of aluminium, making it more durable, wear-resistant, and ready for high-performance applications. In this article, we’ll explore what hard anodising is, its benefits, applications, and how it compares to regular anodising.
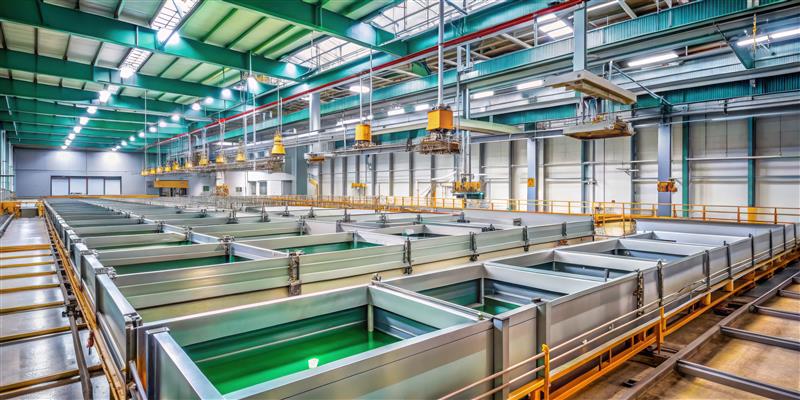
What is Anodising?
Anodising is an electrochemical process that enhances the natural oxide layer on the surface of aluminium. During this process, aluminium parts are submerged in an electrolytic bath and exposed to an electric current, triggering oxidation that thickens the surface layer. This protective oxide coating significantly improves resistance to corrosion, wear, and environmental factors. The anodised surface is also porous, allowing it to be dyed in a variety of colours, making it both functional and aesthetically versatile.
There are several types of anodising, each with distinct characteristics. Chromic Acid Anodising produces the thinnest oxide layer (typically 1–10 microns) and is often used in aerospace applications where fatigue resistance and a low-friction surface are required. It offers good corrosion protection while minimally altering dimensions. Sulphuric Acid Anodising, the most commonly used method, creates a slightly thicker layer (5–25 microns) and is valued for its balance of cost, corrosion resistance, and colourability—frequently used in decorative or consumer applications.
In contrast, Hard Anodising generates a much thicker and denser oxide layer, typically ranging from 25 to 150 microns. This makes it ideal for high-performance applications where durability, wear resistance, and electrical insulation are essential, such as in the aerospace, automotive, and military sectors. Hard anodising not only strengthens aluminium but also extends its service life in harsh environments.
What is Hard Anodising?
Hard anodising, or hardcoat anodising, is a specialized type of anodising that produces a thicker, harder oxide layer compared to regular anodising. The process involves submerging aluminium into an acid electrolyte solution and applying a higher voltage and lower temperature than in standard anodising. This creates an oxide layer that is significantly thicker, typically ranging from 25 to 150 microns, as compared to the 5-20 microns in regular anodising. As a result, hard anodising increases the metal’s surface hardness, improving its wear and scratch resistance, and providing greater protection against corrosion.
Benefits of Hard Anodising
- Increased Durability and Hardness:
Hard anodising significantly enhances the surface hardness of aluminium, making it more resistant to scratches, abrasion, and other forms of mechanical wear. The resulting oxide layer is harder than the base aluminium, offering protection in even the harshest operating environments.
- Superior Corrosion Resistance:
One of the primary benefits of hard anodising is its enhanced corrosion resistance. The thicker oxide layer provides a formidable barrier against environmental elements, preventing oxidation even in aggressive environments such as saltwater or acidic conditions.
- Aesthetic and Functional Qualities:
Hard anodised aluminium maintains the aesthetic versatility of regular anodising, allowing for colour finishes while retaining superior strength and durability. The surface can be dyed or left natural, providing both functional and visual benefits.
- Electrical Insulation:
The oxide layer created during hard anodising is non-conductive, making hard anodised aluminium a good choice for applications where electrical insulation is required, such as in electrical components or machinery parts.
- Eco-friendly Process:
Hard anodising is an environmentally friendly process. The anodised coating is non-toxic, and the process generates minimal waste, making it a more sustainable alternative to other coating techniques.
Disadvantages and Considerations of Hard Anodising
While hard anodising offers superior durability and wear resistance, it’s not without its drawbacks. One key consideration is dimensional change—the oxide layer adds thickness to the part and can penetrate the surface, which may affect tight tolerances and require compensation in the design stage. Additionally, colour options are limited compared to other anodising methods, as the dense, dark oxide layer does not absorb dyes as readily. The process also requires higher voltages and lower temperatures, making it more energy-intensive and potentially more expensive than regular sulphuric or ch ain casting alloys may not yield consistent or high-quality results. Finally, the oxide layer, while hard, can be brittle, making it susceptible to cracking under high impact or deformation. These factors should be carefully considered when selecting hard anodising for your application. romic acid anodising. Furthermore, not all aluminium alloys are suitable for hard anodising; high-silicon or certain casting alloys may not yield consistent or high-quality results. Finally, the oxide layer, while hard, can be brittle, making it susceptible to cracking under high impact or deformation. These factors should be carefully considered when selecting hard anodising for your application.
Applications of Hard Anodising
- Aerospace:
Hard anodising is widely used in the aerospace industry, where components need to withstand extreme temperatures, high wear, and exposure to corrosive substances. The hard anodised coating ensures that aluminium parts can maintain their integrity under harsh conditions, such as in aircraft engines or landing gear.
- Automotive:
In the automotive sector, hard anodised parts are used in high-performance engine components, suspension systems, and various other parts exposed to friction, wear, and corrosion. The durability of hard anodised aluminium makes it ideal for components that need to perform at their best under constant stress.
- Military and Defence:
Military and defence applications often require materials that can endure extreme wear and exposure to harsh environments. Hard anodising provides aluminium with enhanced strength, corrosion resistance, and the ability to withstand high-impact conditions, making it perfect for military equipment, vehicle parts, and protective casings.
- Other Industries:
Hard anodising is also used in industries like electronics, medical devices, and consumer goods. For example, it can be found in the production of high-end cookware, industrial machinery, and precision tools, all of which benefit from the process’s strength and durability.
Comparison: Hard Anodising vs. Chromic Acid and Sulphuric Acid Anodising
Hard anodising stands apart from both chromic acid and sulphuric acid anodising primarily in the thickness and durability of the oxide layer it produces. While chromic acid anodising and sulphuric acid anodising typically create thinner oxide layers (ranging from 1-25 microns), hard anodising generates a much thicker oxide layer (25-150 microns), significantly enhancing the surface hardness and wear resistance. This makes hard anodising ideal for high-performance applications in demanding industries such as aerospace, automotive, and military, where extreme durability and protection from wear are crucial.
In contrast, chromic acid anodising offers moderate corrosion resistance and is often used in aerospace and military applications where a thinner, less abrasive oxide is sufficient. It is also known for being more environmentally friendly with a lighter grey finish. Sulphuric acid anodising, on the other hand, is commonly used for decorative purposes or in less harsh environments, providing a variety of finishes, from matte to glossy, but with a lower level of wear resistance compared to hard anodising.
Each process has its own niche depending on the desired strength, appearance, and environmental considerations, with hard anodising being the top choice for applications requiring maximum durability.
Comparison of Anodising Types
Property | Hard Anodising | Chromic Acid Anodising | Sulphuric Acid Anodising |
Electrolyte | Sulphuric acid with higher voltage and lower temperature | Chromic acid solution | Sulphuric acid solution |
Oxide Layer Thickness | 25–150 microns | 1–10 microns | 5–25 microns |
Surface Hardness | High (up to 60–70 HRC) | Moderate (up to 40 HRC) | Moderate (up to 40 HRC) |
Corrosion Resistance | Excellent | Excellent (especially for mild environments) | Good to Excellent |
Wear Resistance | Very High | Moderate | High |
Aesthetic Finish | Matte or natural (can be dyed) | Light grey, matte finish | Can be glossy or matte, often used for decorative purposes |
Electrical Insulation | Excellent | Good | Moderate |
Environmental Impact | Minimal, process is generally eco-friendly | Low environmental impact, used for aerospace applications | Moderate, some toxic by-products |
Applications | Aerospace, automotive, military, industrial | Aerospace, military, lightweight components | Consumer goods, decorative items, electronics |
Cost | High (due to thicker oxide and process conditions) | Moderate to High | Low to Moderate |
How to Choose Hard Anodising for Your Project
Choosing hard anodising depends on the specific needs of your project. If your aluminium components will be subjected to high stress, frequent friction, or harsh environmental conditions, hard anodising is the best choice to ensure long-term durability and performance. The thicker oxide layer created through hard anodising offers superior wear resistance and corrosion protection, making it an ideal solution for aerospace parts, automotive components, and military equipment.
However, it’s important to consider the cost implications, as hard anodising can be more expensive than regular anodising due to the more intense process. Still, the long-term benefits, including reduced maintenance and improved product lifespan, often outweigh the initial investment.
Conclusion
Hard anodising is a powerful surface treatment process that enhances the properties of aluminium, making it suitable for the most demanding applications. Whether in aerospace, automotive, or military industries, hard anodising provides increased durability, superior corrosion resistance, and an overall longer lifespan for aluminium components. By understanding the benefits and applications of hard anodising, you can make informed decisions for your next project, ensuring that your parts stand up to the test of time and performance.
What is meviy?
meviy is an AI-powered on-demand manufacturing platform developed by MISUMI. It allows engineers to upload 3D CAD models and receive instant quotations, automatic manufacturability analysis, and lead time estimates. Supporting processes like CNC machining, sheet metal fabrication, and 3D printing, Meviy streamlines procurement, reduces communication loops, and accelerates product development. Its AI capabilities also enable part recognition, interactive design editing, and compatibility with a wide range of materials—making it a smart, fast, and reliable tool for today’s engineering teams.