BLOG » Understanding Metal Hardness – How It Affects Machinability and Performance
Understanding Metal Hardness – How It Affects Machinability and Performance
Metal hardness is a fundamental property that significantly influences how materials behave during machining and in end-use applications. Whether you’re selecting the right cutting tool or deciding how a component will perform under stress, understanding hardness is essential.
In this article, we’ll explore what metal hardness really means, how it’s measured, and why it’s critical for CNC machining and manufacturing performance.
What Is Metal Hardness?
Metal hardness refers to a material’s resistance to deformation—typically measured through indentation or scratching. It’s not a single property but rather an umbrella term that reflects how a metal responds to mechanical stress, wear, and cutting forces.
Harder metals tend to resist wear and abrasion, making them suitable for demanding environments. However, they’re also more difficult to machine, requiring careful planning, specialised tooling, and optimised cutting parameters.
Metal Hardness Scales and Tests
There are several standardised scales used to measure metal hardness, each suited to different materials and applications.
Brinell Hardness (HB)
The Brinell hardness test uses a steel or tungsten carbide ball pressed into the surface of the metal under a specified load. It’s ideal for softer metals and provides an average value over a relatively large area.
- Commonly used for: Aluminium alloys, mild steel, cast iron
- Example: Mild steel typically has a Brinell hardness around 120–180 HB.
Rockwell Hardness (HR)
The Rockwell test measures the depth of indentation using various scales (e.g., HRC for harder materials, HRB for softer). It’s fast, simple, and widely used in industry.
- HRC is typically used for: Hardened steels, tool steels
- HRB is used for: Copper alloys, soft steels, aluminium
- Example: Tool steel may exceed 60 HRC, indicating high wear resistance.
Vickers Hardness (HV)
The Vickers test uses a diamond-shaped indenter and measures the diagonal length of the resulting impression. It’s highly accurate and useful for testing thin materials and surface coatings.
- Often used in labs and for microhardness testing
- Suitable for a wide range of materials, from soft to very hard
- Example: Hardened chromium may measure over 900 HV
Conversion Between Scales
While there’s no perfect formula to convert between hardness scales, approximate conversions are available in engineering references. For CNC machining, knowing the hardness value in context of the specific scale is crucial to selecting appropriate tools and settings.
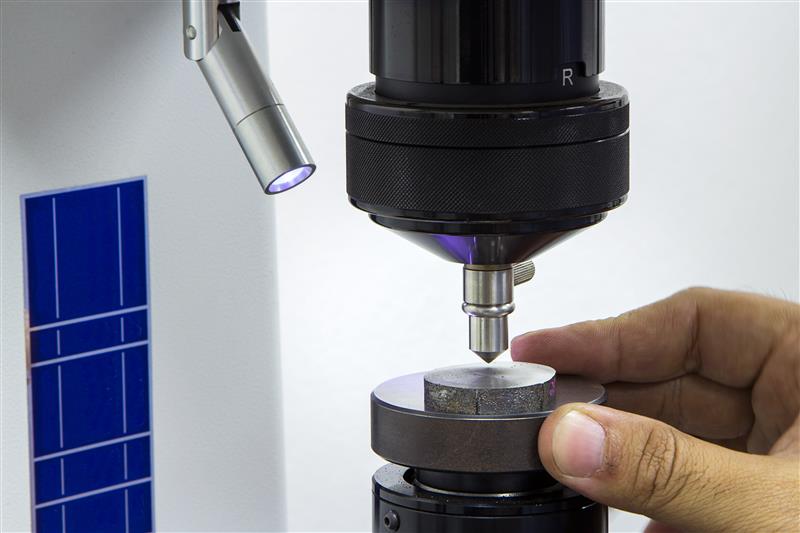
How Metal Hardness Affects Machining
Tool Selection
Harder metals require more robust cutting tools—typically made from carbide, CBN (Cubic Boron Nitride), or ceramic materials. These tools can withstand higher temperatures and resist wear during cutting operations.
- Soft metals (e.g., aluminium, brass): High-speed steel (HSS) or uncoated carbide tools work well.
- Medium hardness (e.g., mild steel): Coated carbide tools improve tool life and finish.
- Hard metals (e.g., tool steel, titanium, Inconel): Require CBN or advanced ceramic tooling.
Cutting Parameters
As metal hardness increases, machining parameters must be adjusted accordingly:
Hardness | Cutting Speed | Feed Rate | Depth of Cut | Tool Wear |
---|---|---|---|---|
Low (e.g., <150 HB) | High | Moderate | Moderate | Low |
Medium (150–300 HB) | Moderate | Moderate | Moderate | Moderate |
High (>300 HB / >40 HRC) | Low | Low | Shallow | High |
- Higher hardness = slower cutting speed, reduced feed, and shallower passes
- Improper parameters lead to tool chipping, overheating, and dimensional inaccuracies
Hard vs. Soft Metals in CNC Machining
Soft Metals: Easier to Machine, Lower Strength
Examples: Aluminium, copper, mild steel
- Advantages:
- Faster machining
- Longer tool life
- Excellent surface finish
- Disadvantages:
- Lower wear and corrosion resistance
- Not suitable for high-stress or high-heat environments
Hard Metals: Stronger, But More Challenging to Machine
Examples: Tool steels, hardened stainless steel,
- Advantages:
- High strength and thermal resistance
- Excellent wear resistance
- Disadvantages:
- Slower machining speeds
- Greater tool wear and risk of tool failure
- Requires advanced cutting strategies and cooling systems
Application Matters:
- Aerospace and automotive industries often favour harder materials for structural and performance-critical parts.
- Consumer electronics may lean towards softer metals for fast prototyping and cosmetic components.
Design Considerations Based on Metal Hardness
When designing parts for CNC machining, metal hardness should influence your decisions on geometry, tolerances, and intended application. Harder materials, while offering superior strength and wear resistance, are more prone to causing tool deflection and increased stress during machining. As a result, designers should avoid overly intricate features, deep pockets, or thin walls when specifying components made from hardened steels or exotic alloys. Fillets and chamfers can help distribute stress more evenly and reduce the risk of cracking or thermal distortion. Additionally, tolerances should be realistic—ultra-tight tolerances on very hard materials significantly increase machining time and cost. If high hardness is critical for the final part, consider machining in a softer, pre-hardened state and applying heat treatment afterward, followed by a finishing operation. This balance between machinability and mechanical performance is key to efficient, cost-effective design.
Conclusion
Understanding metal hardness is essential to achieving successful results in CNC machining. It affects everything from tool selection and cutting parameters to cycle time and surface quality. While softer metals offer ease of machining, harder metals provide superior strength and performance—albeit with added complexity in processing.
By choosing the right approach and following best practices, manufacturers can machine high-hardness materials with precision and reliability, ensuring the final product meets its mechanical and functional requirements.
What is meviy?
meviy is an AI-powered on-demand manufacturing platform developed by MISUMI. It allows engineers to upload 3D CAD models and receive instant quotations, automatic manufacturability analysis, and lead time estimates. Supporting processes like CNC machining, sheet metal fabrication and CNC turning, meviy streamlines procurement, reduces communication loops, and accelerates product development. Its AI capabilities also enable part recognition, interactive design editing, and compatibility with a wide range of materials—making it a smart, fast, and reliable tool for today’s engineering teams.