BLOG » CNC Machining vs. 3D Printing for Prototyping: Which Should You Choose?
CNC Machining vs. 3D Printing for Prototyping: Which Should You Choose?
Prototyping plays a pivotal role in product development, allowing engineers and designers to validate form, fit, and function before moving into mass production. The ability to quickly create and test prototypes can make or break a product’s success in today’s fast-paced, innovation-driven markets.
Among the most widely adopted methods for prototyping are CNC machining and 3D printing. These technologies represent two fundamentally different manufacturing approaches, offering distinct advantages and trade-offs depending on the project requirements.
At their core, the key distinction lies in their processes: CNC machining is a subtractive method, removing material from a solid block, while 3D printing is additive, building parts layer by layer from the ground up.
In this article, we compare CNC machining and 3D printing methods from process, materials, and characteristics to time, cost, and designability so that you can make an informed decision to select the best method for your production needs.
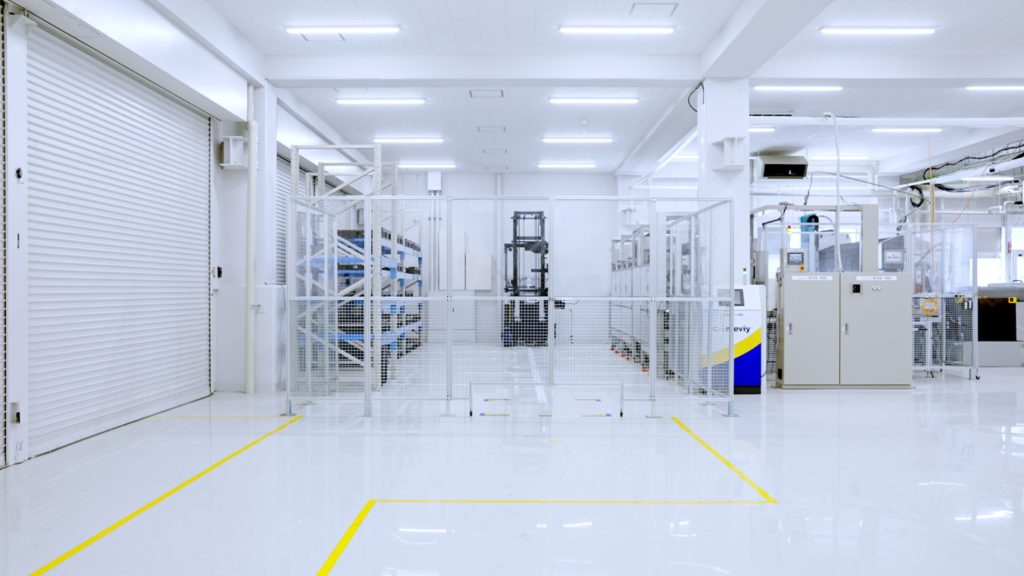
How CNC Machining and 3D Printing Work
CNC Machining: A Subtractive Process
CNC (Computer Numerical Control) machining involves the precise removal of material using cutting tools such as mills, lathes, and drills. The process starts with a solid workpiece—often metal or plastic—that is shaped by subtracting material until the final geometry is achieved. CNC is ideal for producing functional, high-strength components with tight dimensional accuracy.
3D Printing: An Additive Process
In contrast, 3D printing (also known as additive manufacturing) builds objects from scratch by depositing material layer by layer. Techniques include FDM (Fused Deposition Modelling), SLA (Stereolithography), and metal-based methods like DMLS (Direct Metal Laser Sintering).
Summary
While both processes produce tangible prototypes, their methods—cutting versus building—have profound implications on speed, cost, material choice, and design flexibility.
Material Capabilities – What Can You Use?
CNC Machining
CNC supports a vast range of materials, including:
These materials maintain their original mechanical properties, making them ideal for functional testing.
3D Printing
3D printing materials are more varied by process:
- Plastics: PLA, ABS, Nylon, PETG
- Resins: Standard, flexible, high-temperature
- Metals: Stainless steel, aluminium, titanium (via DMLS/SLM)
However, the mechanical performance of printed parts often falls short of machined components due to layer adhesion and porosity.
Strength, Durability, and Finish
CNC-machined parts tend to outperform 3D prints in strength and surface quality, while 3D printing enables more exotic geometries with less waste. For functional prototypes requiring strength and durability, CNC remains the benchmark.
Precision, Tolerances, and Surface Finish
CNC Machining
CNC machining is renowned for its tight tolerances—as low as ±0.01 mm—and fine surface finishes achievable through additional polishing or anodising. This precision is crucial in industries like aerospace and medical device development.
3D Printing
3D printing, while accurate, is inherently limited by layer resolution. Post-processing such as sanding, coating, or curing may be required to improve finish and dimensional accuracy.
Use case: For fitting tests, sealing surfaces, or moving parts, CNC often provides the reliability needed.
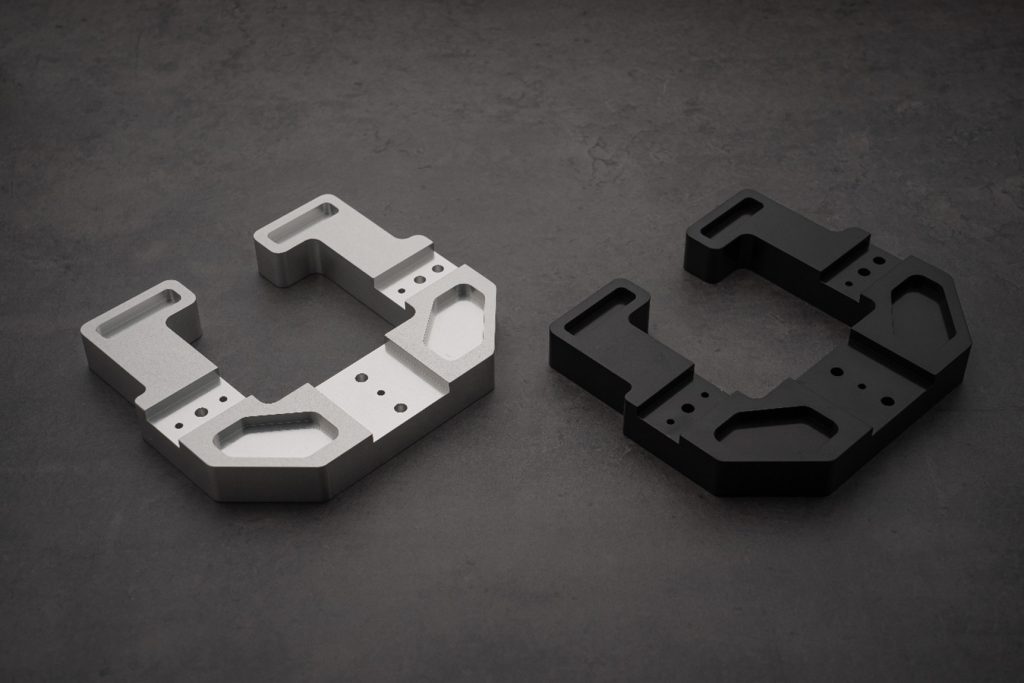
Speed and Production Time
CNC Machining
- Pros: Fast turnaround for single, simple prototypes
- Cons: Longer setup time for complex parts, especially those requiring custom fixturing or tooling
3D Printing
- Pros: Ideal for quick iterations and overnight builds
- Cons: Slower for large or multiple parts, especially in metal printing
For businesses racing to shorten their time-to-market, the right choice depends on part complexity and the number of iterations required.
Cost Comparison – Which is More Affordable for Prototyping?
CNC Machining
CNC machining typically involves higher setup and material costs, particularly with metals. Machining also generates more waste, increasing overall cost.
3D Printing
3D printing shines in cost-effectiveness for short runs and complex geometries that would be difficult or expensive to machine.
Hidden costs to consider include:
- Tooling (CNC)
- Post-processing (both)
- Maintenance and failed builds (3D printing)
For bulk prototyping or when working with expensive materials, CNC may offer better long-term value.
Design Complexity and Geometry Considerations
CNC Machining Advantages
While CNC machining has some constraints related to tool access and axis orientation, modern multi-axis machines and advanced toolpaths have significantly expanded its capabilities. Features such as complex contours, precision holes, and fine surface detailing can now be achieved with exceptional accuracy. CNC is especially advantageous when tight dimensional control over critical features is required—something that additive processes often struggle to deliver.
For assemblies that demand repeatability, tight fits, or moving components, CNC machining offers superior consistency and stability.
3D Printing Capabilities
3D printing allows greater freedom in creating internal channels, lattice structures, and organic geometries without the need for complex tooling. This makes it well suited for early-stage concept models and lightweight, non-functional parts.
However, such design flexibility often comes at the cost of precision, material integrity, and surface finish, which may require further refinement in later prototyping stages—where CNC machining becomes the method of choice.
Strength and Durability of Prototypes
CNC Machined Parts
CNC parts are typically stronger and more durable, as they retain the material’s full structural integrity. This is critical for testing mechanical loads, thermal performance, or chemical resistance.
3D Printed Parts
3D-printed parts—especially from FDM or SLA—can suffer from layer delamination and reduced impact resistance. While metal printing offers better performance, it comes at a significantly higher cost.
Material selection also influences durability: aluminium and POM (CNC) outperform PLA or resin (3D print) in functional tests.
Aspect | CNC Machining | 3D Printing |
---|---|---|
Process Type | Subtractive | Additive |
Materials Supported | Metals (Aluminium, steel, stainless steel, copper), Plastics (ABS, POM, PPS, MC Nylon) | Plastics (PLA, ABS, Nylon, PETG), Resins (standard, flexible, high-temp), Metals (stainless steel, aluminium, titanium via DMLS/SLM) |
Material Properties | Maintains original mechanical strength and properties | Often weaker due to layer adhesion, porosity |
Strength & Durability | Stronger, more durable parts suitable for functional testing and mechanical loads | Weaker, prone to layer delamination, better for lightweight or non-functional parts |
Precision & Tolerances | High precision, tight tolerances (±0.01 mm), smooth finishes possible | Limited by layer resolution, requires post-processing for better finish and accuracy |
Surface Finish | High-quality finish achievable with polishing, anodising | Surface roughness; requires sanding/coating/curing to improve |
Speed & Production Time | Fast for simple parts; longer setup for complex/custom tooling | Fast for quick iterations; slower for large or multiple metal parts |
Cost Considerations | Higher setup and material costs; more waste produced | Cost-effective for short runs and complex geometries; potential hidden costs in post-processing and failed builds |
Design Complexity | Good for complex contours, precision holes, tight fits; limited by tool access but improving | Excellent freedom for complex, organic shapes, internal channels, lattice structures |
Use Cases | Functional prototypes needing strength, durability, tight tolerances, and repeatability | Early-stage models, concept designs, lightweight parts with complex geometries |
Key Advantages | Superior strength, dimensional accuracy, reliability for mechanical/thermal/chemical testing | Greater design freedom, less waste, faster iteration cycles |
Limitations | Setup time and cost for complex parts; limited by tool access | Lower mechanical properties, surface finish issues, slower large-batch metal printing |
Which Method is Best for Your Prototyping Needs?
Here’s a quick decision-making guide:
Choose CNC Machining if:
- You require high precision and tight tolerances
- The prototype must endure functional or stress testing
- You need to work with metallic or engineering-grade materials
Choose 3D Printing if:
- You need to iterate quickly and affordably
- The design involves complex or organic shapes
- Budget and speed outweigh the need for strength
Hybrid Approach
In some cases, a hybrid prototyping strategy works best—using 3D printing for early iterations and CNC machining for final validation before tooling.
Conclusion
Both CNC machining and 3D printing are indispensable tools in the prototyping process, each offering unique strengths depending on your needs.
CNC provides unmatched precision and material strength, making it ideal for high-performance prototypes. 3D printing offers agility and freedom of design, perfect for rapid iteration and complex geometries.
Which is better? It depends—on your budget, your timeline, and your design goals.
What is meviy?
meviy is an AI-powered on-demand manufacturing platform developed by MISUMI. It allows engineers to upload 3D CAD models and receive instant quotations, automatic manufacturability analysis, and lead time estimates. Supporting processes like CNC machining, sheet metal fabrication and CNC turning, meviy streamlines procurement, reduces communication loops, and accelerates product development. Its AI capabilities also enable part recognition, interactive design editing, and compatibility with a wide range of materials—making it a smart, fast, and reliable tool for today’s engineering teams.