BLOG » How to design holes for components – useful tips
How to design holes for components – useful tips
Sharing a common understanding on how components are manufactured is indeed the key to improving the procurement process for designers. This is why we are enriching our “meviy guide” for components design. This blog post focuses on the basic design considerations on hole machining. Let’s see what the different types of holes are and how to design holes for your custom mechanical parts avoiding some of the most common mistakes.
Basic information of Hole Machining
In the case of machining, holes are generally processed in the following steps:
- Drilling a center hole.
- Drilling a pilot hole (drilling process).
- Performing specific machining operations based on the intended use. Examples are reaming, tapping, counterboring.
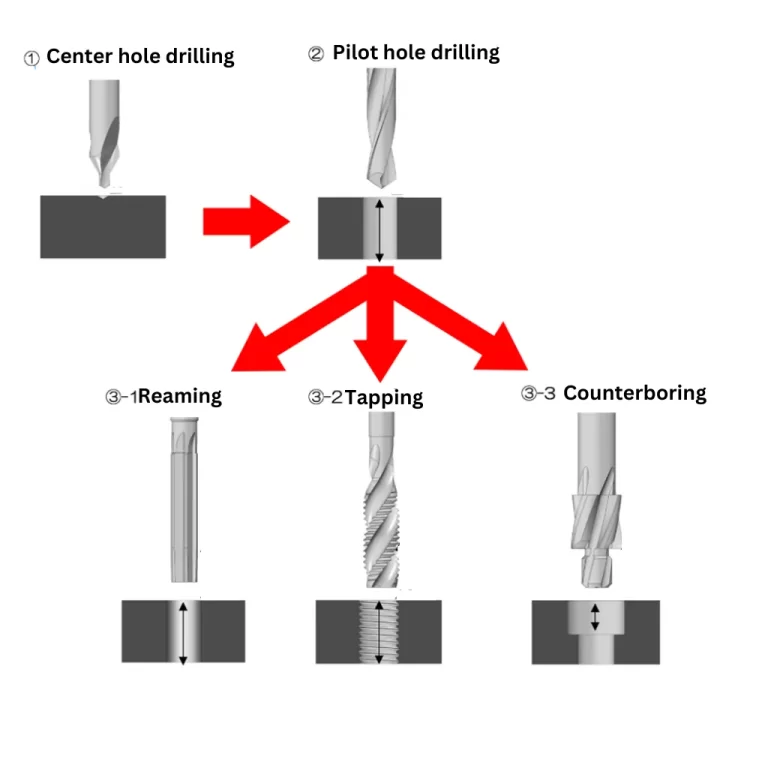
Center drilling
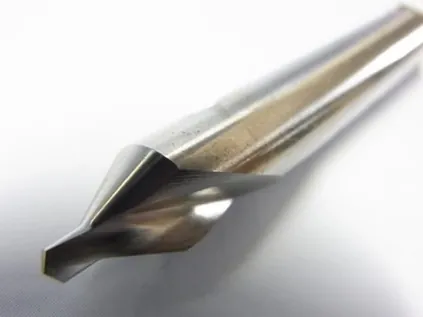
Counterboring
Counterboring is the technique performed to ensure that the screw head does not protrude from the surface. While it is possible to perform counterboring using a regular end mill, for standardized screw counterboring, dedicated cutting tools for counterboring are often used.
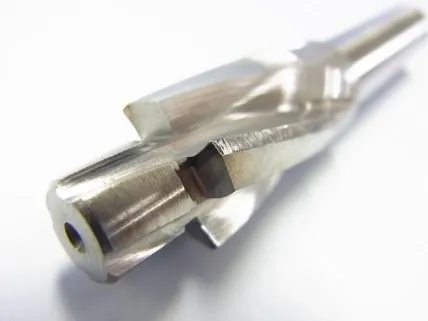
Tapping
When creating holes for fastening parts with screws, tap machining is the best option. After the initial drilling process, tap machining is performed to create the threaded hole. A specialized cutting tool is used for this purpose, and in the case of CNC machining, a dedicated program called a tap cycle is used.
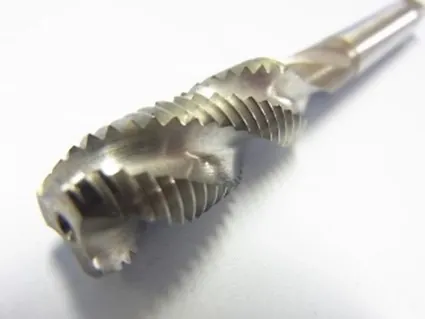
Reaming
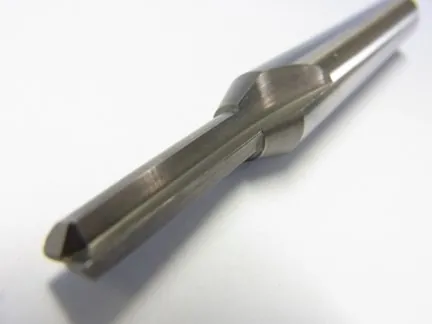
Drill machining
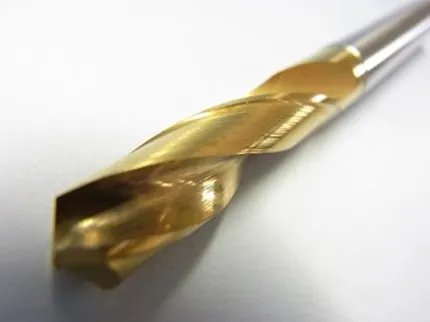
How to design holes guide - common issues
Now, let’s discuss some common problems that arise from hole machining. There might indeed be misunderstandings and misalignments between the designer’s needs and the supplier’s capacity. Here, we will introduce common troubles related to holes, and we hope you find them helpful to learn better how to design holes for your custom parts.
Hole is too close to the edges - troubleshooting
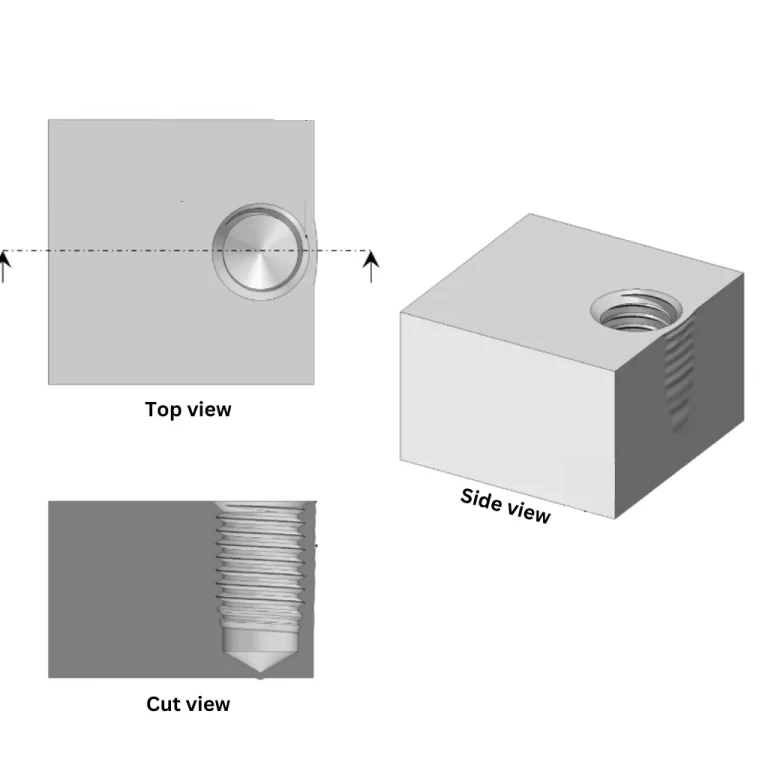
Indeed, holes near the edge are structurally weak, and it is generally not recommended to design them that way.
To avoid such situations, it is advisable to maintain a minimum distance from the edge of at least the diameter of the hole. This is particularly important for threaded holes, as they are more prone to these issues, requiring extra attention.
If it is impossible to maintain the necessary distance in the design, an alternative approach is to perform additional machining on the side after the hole drilling process. This can help mitigate the “bulging” effect caused by the initial machining. However, introducing an additional machining step can increase costs and complexity.
Hole is too deep - troubleshooting
In hole machining, precision can be achieved for depths up to approximately 8 times the diameter. Beyond that depth, specialized processes are required to avoid any issues and errors in manufacturing.
With such deep holes, the tendency is for them to bend and the hole diameter to widen. Although high-precision deep-hole machining methods like honing are available, there are still limitations if the initial hole is bent. In such cases, another option is to use shape carving electrical discharge machining. Nonetheless, it’s important to remember that there are still limits to machining deep holes with high precision, depending on the shape. As a general rule, a depth of approximately 8 times the diameter is a good starting point.
For example, let’s imagine a part similar to the one shown in the figure below. It features small-diameter through-holes along the length of the block.
If you were to drill the hole from one direction only, it would bend. The drill gradually bends as it goes in, resulting in larger errors the further it moves away from the entrance.
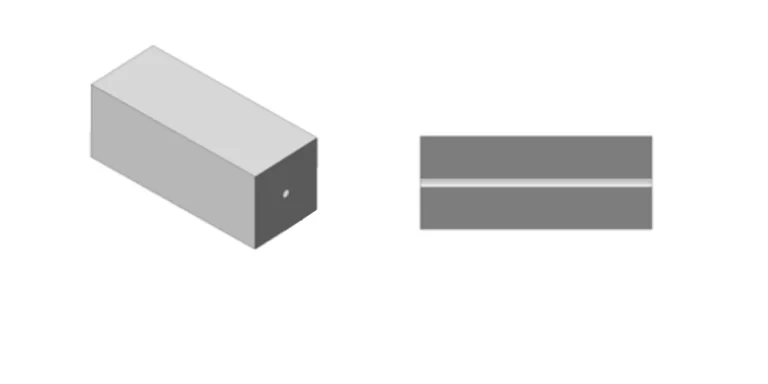
Conclusions
As we’ve seen, there are various considerations on the manufacturing side depending on the purpose and shape of the hole. While there are still deeper aspects to holes, if you can firmly grasp the fundamental principles we discussed today, it is likely that you will be able to design in a way that can be easily accommodated by the manufacturing process.
Design has its own pain-points, and manufacturing also has its own requirements. It is important for both sides to understand each other’s perspectives and work together to achieve better product development.