BLOG » What is Bakelite: Material Overview
What is Bakelite: Material Overview
Thermosetting resins, comparatively produced in smaller quantities than thermoplastic resins, are often considered somewhat of a “supporting actor.” However, did you know that the first synthetic resin created by humans wasn’t a thermoplastic resin but a thermosetting resin? The name of this oldest synthetic resin known to humankind is “Bakelite.” But what is Bakelite? In this we will delve into the types, characteristics, advantages and disadvantages, as well as the applications of Bakelite.
Bakelite is a thermosetting resin with a well-balanced set of properties, and it is currently sold in the form of laminated sheets where the resin is interwoven with a base material. Continuously contributing to various fields, including cutting-edge materials, Bakelite can be considered a resin that silently supports our lives from behind the scenes.
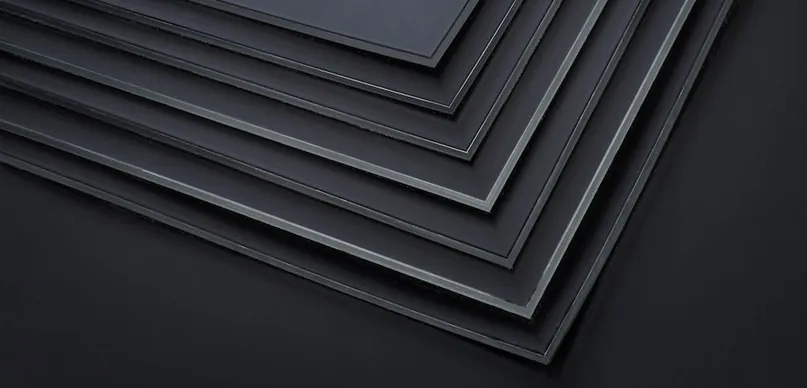
What is Bakelite?
Bakelite, also known as “phenolic resin,” is a thermosetting resin developed in 1872 by German chemist Adolf Bayer. In industrial applications, it is recognized as a heat-cured, sheet-like material applied to paper or cloth. Beyond this, Bakelite finds uses in adhesives, coatings, and electrical insulating materials. Its raw materials include phenol and formaldehyde. By heating these with an acid or base catalyst and adding curing agents as needed, three-dimensional Bakelite with a mesh structure is obtained.
Bakelite, being a relatively inexpensive thermosetting resin, boasts excellent heat resistance, strength, and electrical insulation properties. Over time, it has been employed in various scenarios. Although the advent of thermoplastic resins has altered its landscape, Bakelite continues to evolve uniquely to meet the demands of new markets. Even today, applications that leverage Bakelite’s inherent characteristics are being developed, and its utilization is expected to expand in the future.
Types of Bakelite
Currently, Bakelite is commonly distributed not as a standalone resin but as laminated sheets formed by interweaving a resin with a base material (paper or cloth). These are manufactured by applying resin to each base material and curing it through a heat process. Laminated sheets with paper as the base material are referred to as “Paper Bakelite,” while those with cloth as the base material are called “Cloth Bakelite.” Here are the distinctive features of each product:
Paper Bakelite
Paper Bakelite is characterized by being less expensive (approximately half the cost) and lighter than Cloth Bakelite. When electrical insulation is the primary concern, the use of Paper Bakelite is recommended. However, due to the use of paper as the base material, its high water absorption should be noted.
Cloth Bakelite
This type of Bakelite excels in mechanical properties compared to Paper Bakelite, making it well-suited for applications where strength is crucial. However, like Paper Bakelite, it has a high water absorption characteristic, requiring usage in environments with low humidity.
Advantages of Bakelite
While Bakelite has numerous advantages, some representative ones include:
High Heat Resistance
Bakelite is a thermosetting resin, making it notable for its resistance to heat. It exhibits high heat resistance with a temperature range of 150 to 180°C, maintaining strength even under elevated temperatures.
Excellent Electrical Insulation
Bakelite’s high electrical insulation property makes it valuable for applications in electrical insulation materials such as printed circuit boards, breakers, and coatings for distribution boards.
High Mechanical Strength
The impressive mechanical strength is a significant advantage of Bakelite. Particularly, Cloth Bakelite has higher strength than Paper Bakelite and is often used in applications requiring impact resistance.
Processable through Injection Molding
When molding Bakelite as a standalone resin, it can be processed using injection molding, similar to thermoplastic resins. After heating Bakelite to a temperature just below its curing point (approximately 50°C), it is injected into a mold and then cured by heating to 150 to 180°C.
Disadvantages of Bakelite
When working with Bakelite, it’s crucial to be aware of the following drawbacks:
High Water Absorption
Bakelite laminated sheets contain base materials such as paper or cloth, making them highly absorbent. Hence, Bakelite is unsuitable for use in environments with water or high humidity.
Low Weather Resistance and Susceptibility to Alkaline Solvents
Bakelite is vulnerable to ultraviolet radiation, so caution is required when using it outdoors. Additionally, it can dissolve in alkaline solvents, presenting a weakness in certain chemical environments.
Major Applications of Bakelite
Since its industrial production began in 1907, Bakelite has been widely used in everyday products such as tableware, kitchenware, buttons, watches, and accessories. However, with subsequent inventions of many thermoplastic resins like nylon and fluorine-based resins, some applications of Bakelite were gradually replaced by thermoplastic resins. While the direct molding of Bakelite as a product has become less common, its unique properties continue to drive various applications.
For instance, leveraging its excellent electrical insulation, Bakelite finds applications in printed circuit boards, distribution boards, breakers, and more. Printed circuit boards are essential not only in IT devices like computers and tablets but also in various electronic appliances today. Thus, Bakelite is extensively used in all fields requiring electricity. Additionally, it serves as an adhesive, shell molding material, and paint. Bakelite is employed as an adhesive in applications such as sand molds for casting and binders for 3D printer materials. Exploiting its solubility in alkali and its ability to absorb light in the range of 200–300nm, Bakelite is also used as a photoresist material. Besides these, Bakelite is utilized as a high-performance material in various fields, including metal replacement parts, negative electrode material for lithium-ion batteries, and raw material for pharmaceutical activated carbon. In 2010, Bakelite was even used as insulation material in the capsule that brought back samples from the asteroid “Itokawa.”
Conclusion
Bakelite, also known as phenolic resin, is the world’s first synthetic resin developed over a century ago. As a thermosetting resin, it strikes a balance between being relatively inexpensive and exhibiting excellent heat resistance, strength, and electrical insulation. Presently, Bakelite is available in the form of laminated sheets, incorporating a base material (paper or cloth) interwoven with resin.
Bakelite’s merits include high heat resistance, excellent electrical insulation, high mechanical strength, and processability through injection molding. On the flip side, drawbacks such as recycling challenges, high water absorption, and vulnerability to UV radiation exist.
In current applications, Bakelite is widely used in printed circuit boards, distribution boards, adhesives, paints, photoresist materials, negative electrodes for lithium-ion batteries, and more. The development of its applications is expected to continue in the future.