BLOG » Turning Process of Mechanical Parts: An Overview
Turning Process of Mechanical Parts: An Overview
Turning process is a machining method that uses a lathe machine to achieves the intended shape by removing material through cutting process.
In this article, we’ll introduce the characteristics and processing procedures of turning process
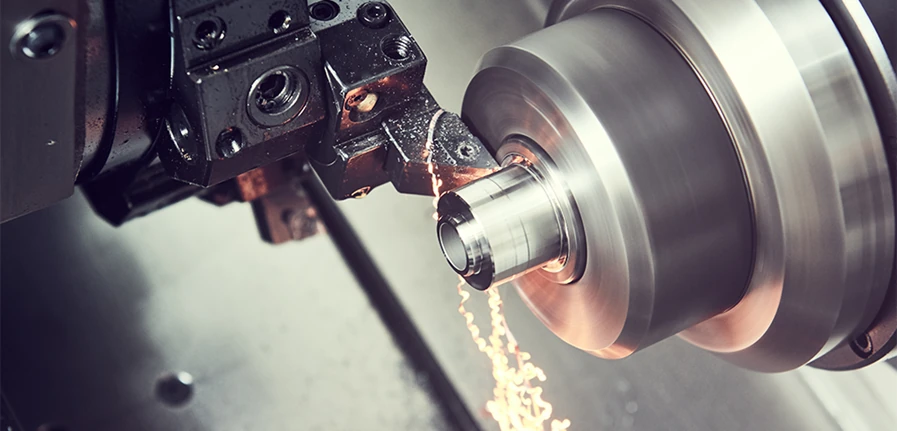
Turning Process of Mechanical Parts
Turning process of mechanical components, also known as lathe process, is a subtype of cutting processing that involves shaping materials by cutting away unwanted portions. While cutting processes also include milling and hole-drilling, turning process revolves around rotating the material and using cutting tools to shape it as per the desired form.
Turning process and milling, both falling under cutting processes, share similarities but differ in what gets rotated. In turning, the material being processed rotates, while in milling, the material is fixed, and the cutting tool rotates
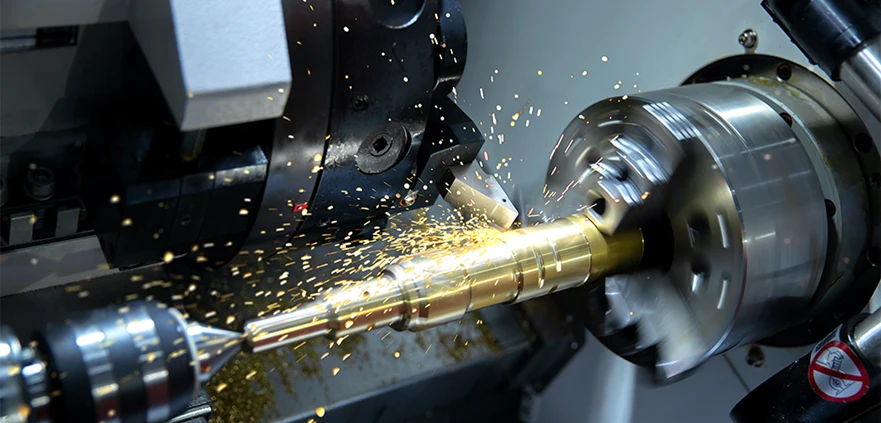
Basic Turning process Methods
External Diameter Processing:
Cutting tools are applied from the outside of the rotating material. Widely used for finishing surfaces and rough shaping in the early stages of processing, external diameter processing might encounter chip entanglement. Adjusting the cutting tool’s angle is necessary for more precision.
Internal Diameter Processing:
Internally expanding material by cutting from the inside, commonly used for adjusting hole sizes and refining internal surfaces. Due to tool length requirements related to hole depth, attention is needed to prevent tool bending, and frequent removal of chips is necessary.
Thread Cutting:
Creating thread pitches, turning process utilizes specialized threading tools to produce both male and female threads. This stands out as an advantage compared to milling, which often only handles female threads.
Facing:
Facing involves cutting off unwanted parts by pressing the tool against the material. It requires a degree of skill due to the use of thin blades, with precautions like using flexible blades and applying oil during cutting for high precision.
Hole-Drilling:
Drilling into the rotating material using a drill, commonly employed when creating holes for internal processing. While drilling lacks high precision, subsequent finishing is often done using internal diameter processing.
Processing Machines Used in Turning process and Their Features
Various types of processing machines are used in turning process, depending on the size of the material and the method of processing. Let’s introduce the representative types of processing machines and their features.
Universal Lathe:
This lathe involves manual movement of tools or tool replacement by operators. It proves valuable when dealing with complex shapes that are challenging to program, one-of-a-kind pieces, or prototypes that require fine adjustments.
NC-Lathe:
In NC lathes, processing conditions are programmed and stored, enabling automatic processing. As it moves according to the programmed instructions, even beginners can achieve a certain level of precision. It is well-suited for mass production where repetitive tasks are necessary.
Facing Lathe:
A horizontal lathe used for processing large materials. It features a horizontal layout that allows chips to fall down without accumulating, preventing a decrease in precision due to chip interference. As chip removal is not necessary, it facilitates continuous and efficient workflow.
Bench Lathe:
As the name suggests, it consists of a compact lathe placed on a table. Its usage is similar to a universal lathe and is essential for creating small parts.
Vertical Lathe
A lathe where tools move vertically, used for processing large materials. It reduces swing caused by the center of gravity and centrifugal force, enabling high processing precision.
Advantages and disadvantages of turning process.
Advantages
Production of Cylindrical Products: Turning process enable the fabrication of cylindrical products by rotating the material and cutting away the unnecessary parts, achieving a high dimensional accuracy.
Adjustable Rotation Speed and Methods: The rotation speed and methods can be adjusted depending on the situation and needs. With a variety of tools designed for specific applications, complex-shaped products can be fabricated by combining different processing methods.
Disadvantages
Tool Change Frequency: While turning process allow for the realization of complex shapes by combining various tools and processing methods, frequent tool changes can increase the time required to complete a single product.
Skillful Operators Needed: To master multiple processing methods, skilled operators are required. Not everyone can produce high-precision products, and the choice of processing methods depends on the complexity of the product and the skill level of the operator.
Turning Operation Procedure
The procedure for turning process varies depending on the product being fabricated. Here, we introduce the typical steps:
Tool and Material Attachment: Attach the cutting tool and material to be used in turning process. Secure them tightly to prevent movement during processing. Accurate positioning during attachment is crucial as misalignment can degrade precision.
Rough Machining: Rough machining is performed to cut away the general shape of the desired product. Precision is not critical at this stage, but caution is needed to avoid excessive cutting. Pay attention to the rotation state of the material and the generation of chips.
Finish Machining: Once the rough machining has shaped the basic product form, finish machining is performed. Since high precision is required, careful attention must be paid to rotation speed and feed rate. If burrs occur, use a file to remove them without damaging the machined surface.
Conclusion
Turning process, a type of cutting process, involves applying cutting tools to a rotating material to shape it. It offers various methods such as external machining, internal machining, thread cutting, hole drilling, and facing. Different types of lathes, including universal lathes, NC lathes, bench lathes, facing lathes, and vertical lathes, cater to specific purposes. While turning process allow for high-precision machining, the need for skilled operators and the time-consuming nature of the process make knowledge-sharing crucial.