BLOG » What is Positional Accuracy in Mechanical Design
What is Positional Accuracy in Mechanical Design
Positional accuracy stands as a cornerstone in mechanical design, embodying a fundamental principle that underpins the functionality and efficiency of countless engineered systems. In this blog post, we delve into the intricacies of positional accuracy, exploring its significance, methods of evaluation, and techniques for enhancement.
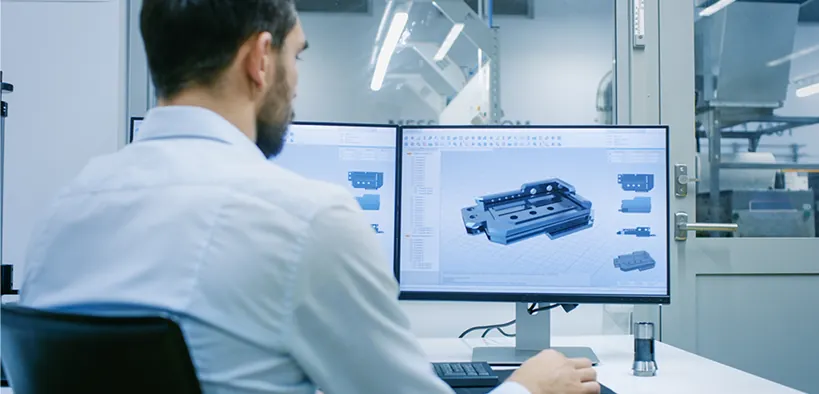
What is Positional Accuracy?
Positional accuracy defines the ability of components within a mechanical system to attain and maintain their intended positions relative to one another. It encompasses the precision with which parts align, mate, and interact, ultimately shaping the performance, reliability, and longevity of the overall assembly.
Machines are typically composed of multiple parts. Whether it’s automobiles, home appliances, or even small smartphones, they all consist of numerous components. When assembling these parts, it’s critical to ensure the accurate positioning of each component relative to others.
“Good positional accuracy” refers to the ideal positioning of each part relative to others. Conversely, “poor positional accuracy” means that the parts are not ideally positioned. Since the dimensions of each part rarely match the ideal size precisely, they often have variations within tolerance ranges. These dimensional variations can lead to misalignment when assembling the parts.
The importance of positional accuracy
So, what happens if the positional accuracy is poor? Let’s explore some examples of potential issues that may arise:
- 1. Assembly failure: For instance, consider the battery cover of a remote control. If the cover is too large and the casing is too narrow, it won’t fit properly, resulting in a defective product that cannot be assembled.
- 2. Generation of abnormal noise or wear: Two adjacent gears with the correct center-axis distance can smoothly transmit power. However, if there is a misalignment in the center-axis position, the meshing of gears becomes poor, leading to abnormal noise or wear.
- 3. Damage: Attempting to forcefully assemble poorly positioned parts can result in damage. Even if assembly is successful, there’s a risk of parts interfering with each other during machine operation, potentially leading to damage.
Methods for Improving Positional Accuracy
Let’s discuss three methods for improving positional accuracy.
Designing Shapes for Positioning:
Positioning shapes are designed to guide parts to the correct positions. For example, if there is a hole in one part and a protrusion in the mating part, inserting the protrusion into the hole aligns the parts correctly. These holes are called positioning holes, and the protrusions are called bosses. Positioning is crucial for assembling parts and is a commonly used design feature.
Tightening Dimensional Tolerances on Drawings:
This method aims to reduce variations in part dimensions. It’s a simple approach that’s often used since it can be implemented with drawing instructions alone. However, tightening tolerances for entire parts can significantly increase costs. Therefore, it’s common to impose strict dimensional tolerances only on the parts that determine positioning, like the positioning holes and bosses mentioned earlier. Care must be taken not to exceed the feasible tolerances for machining.
Fixture Assembly:
Using fixtures during assembly is another method. Fixtures secure two parts in ideal positions during assembly, contributing to improved positional accuracy. While fixtures require sufficient precision, they simplify tasks and can increase work efficiency. However, it’s important to note that if a product is disassembled, reassembly may not be possible without the fixture.
Conclusion
Considering positional accuracy in mechanical design is fundamental and critical. It affects both assembly and functionality since machines consist of various combinations of parts. When designing machines, it’s essential to be mindful of positional accuracy from the outset. The poor positional accuracy may cause noise, tears and other damage as well as assembly failures. There are several ways to improve poor positional accuracy.