BLOG » How to Choose the Best Heat Treatment – Process Guide
How to Choose the Best Heat Treatment – Process Guide
In the process of designing equipment components, key considerations like hardness and impact resistance play pivotal roles in defining their functionality. Certain components necessitate specific levels of hardness or resilience, particularly those engaged in sliding interactions with other parts or subjected to impact forces.
In cases where special properties are required, relying solely on the inherent characteristics of the material may be insufficient. In such situations, heat treatment is the solution that can achieve the characteristics needed for the custom parts. However, selecting the appropriate material and heat treatment method to achieve the desired properties can be challenging due to the variety and complexity of heat treatment options available.
Heat treatment comes in various types and is tailored to different materials and purposes. As a result, many designers may not be familiar with it unless they have specific requirements.
In this article, we have compiled basic information and key points for choosing and applying heat treatment commonly used for equipment components.
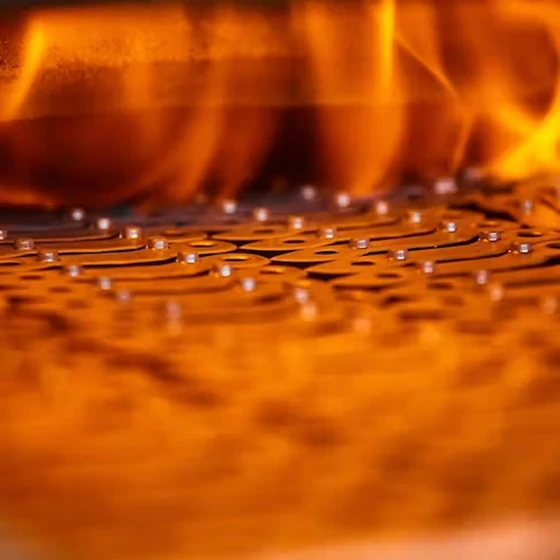
Common Heat Treatments
Heat treatment involves subjecting components to controlled heating and cooling processes to induce alterations in their overall or surface structure. Particularly with carbon-containing steels, heat treatment can significantly modify properties such as hardness, corrosion resistance, wear resistance, and impact toughness.
These methods are broadly classified into “bulk heat treatment,” which treats the entire component, and “surface heat treatment,” primarily targeting the component’s surface. Bulk heat treatment encompasses processes like quenching and tempering, annealing, and normalizing, whereas surface heat treatment methods include induction hardening, carburizing, and nitriding.
The effects of heat treatment are contingent upon factors such as the heating temperature, cooling rate, and cooling medium employed. Rapid cooling, as seen in quenching, generally results in heightened hardness albeit with increased brittleness. Conversely, slower cooling methods, such as annealing and normalizing, aim to refine the structure of the material.
Various cooling techniques, including water quenching, oil quenching, air cooling, and furnace cooling, are chosen based on the desired outcomes of the heat treatment process.
It is imperative to carefully consider the subsequent content to determine the optimal material and heat treatment combination for achieving the desired functionality and performance of your equipment components.
Basics of Bulk Heat Treatment
Steel compositions containing varying carbon levels exhibit distinct transformation temperatures, particularly around the critical threshold of 0.8% carbon content. Steels with precisely 0.8% carbon content fall under the category of eutectoid steels, while those below this threshold are categorized as hypoeutectoid steels, and those exceeding it are termed hypereutectoid steels.
Heat treatment Types and Process
Heat treatment entails subjecting steel components to controlled heating and subsequent cooling processes, inducing alterations in their overall or surface structure. This transformative process influences crucial properties of steel, including hardness, corrosion resistance, wear resistance, and impact resistance.
Heat treatment methodologies are broadly categorized into two streams: bulk heat treatment, which addresses the entire component, and surface heat treatment, which primarily targets the surface layers. Bulk heat treatment encompasses processes like quenching and tempering, annealing, and normalizing. Conversely, surface heat treatment methods comprise induction hardening, carburizing, and nitriding.
The efficacy of heat treatment is contingent upon several factors, including the temperature and rate of heating and cooling. Rapid cooling post-heating, as observed in quenching, typically enhances hardness albeit with a potential trade-off in brittleness. Conversely, slower cooling methods, exemplified in annealing and normalizing, aim to refine the material’s structure without compromising its integrity.
Various cooling techniques, such as water quenching, oil quenching, air cooling, and furnace cooling, are meticulously selected based on the desired outcomes of the heat treatment process.
Understanding the subsequent sections will provide invaluable insights into determining the optimal material and heat treatment combinations tailored to achieve the desired properties and performance levels.
Quenching/Tempering: Understanding the Process
Steel, when heated to temperatures around 800°C, transforms into a structure known as “austenite.” This transformation is crucial for preparing the material for further processing. Subsequently, the material is rapidly cooled, a process called “quenching,” to induce the formation of a hardened structure known as “martensite.”
While quenching enhances hardness, it often introduces brittleness, making the material unsuitable for immediate use. To address this, the material undergoes a process called “tempering,” where it is reheated to a lower temperature than during quenching and then slowly cooled. During tempering, the temperature of reheating plays a crucial role. Reheating at higher temperatures reduces hardness and increases ductility, known as “high-temperature tempering.” Conversely, reheating at lower temperatures prioritizes hardness over ductility, termed “low-temperature tempering.”
Typically, quenching and tempering are performed as a set, ensuring the optimal balance of hardness and ductility in the final product.
Quenching involves a carefully controlled heating and subsequent cooling process.
Heating is carried out in specialized furnaces, raising the material’s temperature to the point where it transforms into austenite. The temperature varies depending on the type of steel, with hypoeutectoid steels requiring temperatures around A3 and hypereutectoid steels needing temperatures slightly higher than A1 (approximately 30-50°C).
Careful temperature control is crucial during the quenching process to ensure effective transformation. Exceeding or falling short of the optimal temperature range can result in incomplete transformation or undesirable properties in the final product.
After heating, the material undergoes rapid cooling to induce the formation of martensite. Various cooling methods, such as water quenching, oil quenching, air cooling, water solutions, and salt bath cooling, are employed based on the desired outcome and material characteristics.
Each cooling method offers unique advantages and challenges. For example, water quenching provides rapid cooling rates at a low cost but may lead to deformation if not executed properly. In contrast, oil quenching offers more uniform cooling but at a slower rate.
Annealing
Annealing is a heat treatment process where metals are gradually cooled after being heated, resulting in a uniform and softer structure. This technique relieves internal stresses and enhances machinability. Annealing encompasses various methods such as full annealing, softening annealing, stress relief annealing, diffusion annealing, and spheroidizing annealing, each tailored to specific temperature ranges depending on the desired outcome. While commonly applied to carbon steel, annealing is also utilized for stainless steel, aluminum alloys, and other materials.
Annealing is often associated with the concept of “softening” the material, making it more workable.
Furthermore, annealing eliminates residual stresses from components and improves their machinability by applying heat. For thin-cutting machining products, timely annealing treatment may enhance the final product’s accuracy.
Annealing can be carried out either on raw materials or on partially machined components. Particularly for materials like EN 1.4301 equiv. (SUS304), prone to deformation due to machining stress, annealing offers improved accuracy, such as in flatness.
Engaging in active information exchange with the manufacturing floor can help determine the feasibility and timing of annealing processes.
Normalizing
Normalizing is a heat treatment method used to homogenize and refine the structure of steel components produced under conditions such as casting, forging, or rolling, which may introduce internal stresses. Normalizing aligns the structure, ensuring desired mechanical properties.
High-Frequency Induction Hardening
High-frequency induction hardening is a surface treatment method that selectively heats only the surface portion of a component to temperatures above 800°C using alternating current induction heating. Primarily employed to enhance the hardness and fatigue resistance of shaft-shaped or gear-shaped components, this method involves placing the component near an electric heating coil and passing high-frequency induced currents through the coil to rapidly heat the surface of the component via resistive heating. Subsequent tempering at low temperatures restores ductility.
High-frequency induction hardening treats only the surface, resulting in improved hardness and wear resistance while retaining toughness in the interior. As heating occurs only partially, deformation and dimensional changes are minimized.
For shaft-shaped components, post-heat treatment distortion such as bending may occur, necessitating straightening using presses. Surface hardening through high-frequency induction hardening induces compressive residual stresses on the surface, enhancing fatigue resistance. Additionally, the surface hardness achieved through high-frequency induction hardening is slightly higher than that obtained through conventional quenching and tempering.
Considered environmentally friendly due to its short heating time, high-frequency induction hardening offers the advantage of specifying the areas and depth of hardening. While it is a form of surface hardening, other methods include flame hardening (HQF), electron beam hardening, and laser hardening.
Carburizing Treatment
In order to harden steel through quenching, carbon is essential. While steel with high carbon content, such as carbon steel, is amenable to quenching, steel with low carbon content, like low-carbon steel, does not respond well to this process. In such cases, carburizing treatment is employed to increase the carbon content on the surface, facilitating quenching.
Low-carbon steel, although cost-effective and possessing excellent workability compared to high-carbon steel, often lacks hardness. Carburizing treatment enhances surface hardness selectively, leveraging the strengths of low-carbon steel while reinforcing its weaknesses.
During carburizing treatment, the component is heated together with a carburizing agent, allowing carbon to diffuse and permeate the surface. Different methods of carburizing treatment include solid carburizing (charcoal), liquid carburizing (cyanide salt), and gas carburizing (hydrocarbon gas), depending on the type of carburizing agent used.
Because carburizing treatment involves prolonged heating at high temperatures, the structure in the central part of the component undergoes transformation. Therefore, quenching and tempering processes are typically conducted after carburizing treatment. Primarily used for low-carbon steel, this treatment results in a surface with enhanced hardness and wear resistance, while maintaining a flexible interior structure.
Nitriding Treatment
Nitriding treatment involves enhancing the hardness of a component’s surface by introducing nitrogen compounds. Methods include gas nitriding, salt bath nitriding, gas soft nitriding, and ion nitriding. By exposing the surface to an atmosphere containing ammonia or nitrogen at temperatures below the austenitizing temperature, nitrogen permeates the surface, resulting in hardening.
Nitriding treatment does not require an increase in treatment temperature, eliminating the need for post-treatment heat treatment and minimizing deformation. It is divided into nitriding treatment, which achieves a hardness of approximately 1000HV, and soft nitriding treatment, which reaches around 600HB and aims to improve fatigue resistance.
Due to the low treatment temperature, even quenched and tempered steels can achieve increased surface hardness while retaining internal hardness. It is also known to be utilized for austenitic stainless steels such as EN 1.4301 equiv. (SUS304) and EN 1.4401 equiv. (SUS316). The thickness and hardness of the nitrided layer vary with the treatment temperature, typically ranging from 0.1 to 0.5mm.
Conclusion - Key Points to Consider in Designing for Heat Treatment
In this blog article we covered common heat treatments used in equipment components. It’s evident that heat treatment is a highly effective means of hardening surfaces, improving wear resistance, and enhancing impact resistance in components. However, it’s crucial to be mindful of certain design considerations when employing heat treatment.
One significant aspect to note is that heat treatment can lead to deformation and dimensional changes due to the application of heat. Precision areas may require leaving allowances for post-treatment finishing processes to achieve accurate shapes.
Components hardened through heat treatment may pose challenges for machining with end mills, especially when hardness exceeds HRC60. Therefore, it’s essential to determine the extent and location of allowances and finishing methods beforehand.
Grinding is relatively straightforward for surfaces and cylindrical shapes. However, for shapes with steps, special grinding methods such as relief grinding (e.g., relief grooves) are necessary to prevent contact between the grinding wheel and the surface.
For complex shapes where conventional machining is difficult, finishing may require specialized grinding machines, potentially increasing processing costs. Minimizing the areas requiring finishing can help reduce costs, so strive for designs that require minimal finishing.
If deformation is a concern, opting for nitriding treatment may be a viable alternative. Additionally, if surface hardness is needed, consider alternatives like hard chromium plating or nickel plating, which were introduced previously.
Utilizing the heat treatment methods discussed here effectively in your designs can lead to rational and efficient designs.