BLOG » What is Electrical Discharge Machining: Process Overview
What is Electrical Discharge Machining: Process Overview
Electrical Discharge Machining (EDM) is a unique machining method that uses thermal energy instead of mechanical energy for material removal. While it may take time, EDM is a convenient method capable of processing any material that conducts electricity.
In this article, we’ll delve into the principles, types, advantages, and disadvantages of EDM, as well as the differences from Electrochemical Machining (ECM).
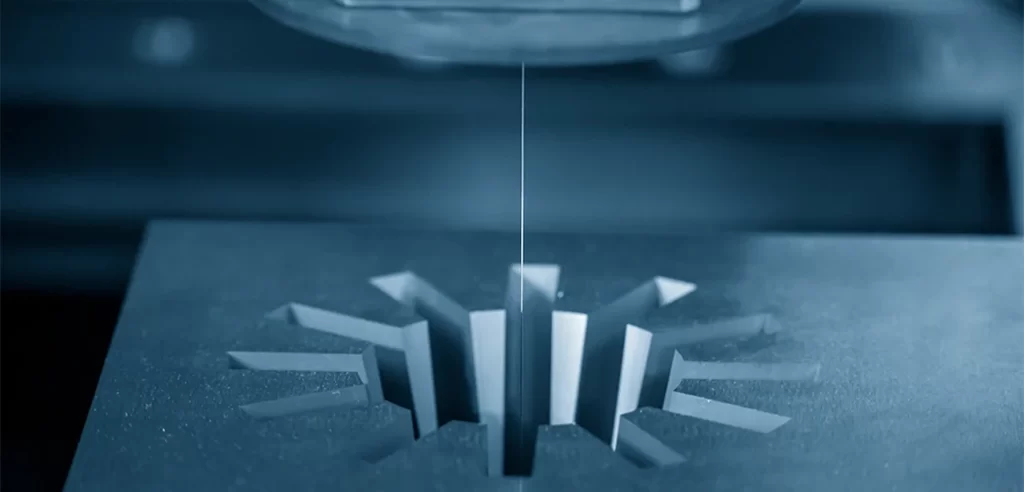
What is Electrical Discharge Machining?
Electrical Discharge Machining (EDM) utilizes the heat generated by the discharge phenomenon to melt workpieces. The workpiece is submerged in an insulating machining fluid (deionized water or oil), and a pulsed voltage is applied between the workpiece and the electrode. This creates an arc discharge (with temperatures exceeding 3000°C) between the workpiece and the electrode, causing the workpiece to melt. As the machining fluid boils and expands, the melted portions of the workpiece (such as metal powder) are flushed away, eliminating concerns about short circuits. Additionally, the machining fluid helps cool the melted portions of the workpiece. This cycle is repeated at a frequency of 1000 to 100,000 times per second to gradually melt the workpiece.
Because this is a chapter explaining what EDM is, and the target keyword is “electrical discharge machining” not “EDM”, let’s spell it out in here.
EDM selectively melts only the workpiece near the electrode, allowing for the machining of various shapes by changing the shape of the electrode. Moreover, as long as the workpiece conducts electricity, even hard materials can be machined. Although EDM takes more time compared to other machining methods, its high precision is a notable feature, making it ideal for manufacturing components requiring high accuracy for industries like aerospace, medical devices, and mold-making.
Materials Suitable for EDM
Any material that conducts electricity can be machined using EDM. Hard materials such as cemented carbide, titanium, stainless steel, molybdenum, and Inconel can be machined without issues. However, it’s essential to note that machining time varies depending on the size and material of the workpiece.
How EDM Works
Electrical Discharge Machining (EDM) operates through a complex interplay of core components, each playing a crucial role in the process. At its core are the electrode and workpiece, positioned in close proximity within a dielectric fluid bath. The dielectric fluid serves multiple purposes: it acts as a medium for the electrical discharge, provides cooling to prevent thermal damage, and flushes away debris generated during machining. As the power supply applies voltage between the electrode and workpiece, an electrical field is created. When the voltage reaches a critical point, the dielectric fluid ionizes, forming a conductive path or spark channel between the electrode and workpiece. This ionization process leads to the generation of intense heat, causing the material in the workpiece to melt and vaporize. Simultaneously, the dielectric fluid rapidly flows into the spark gap, carrying away the molten material and debris, ensuring precise and controlled material removal. This intricate spark process lies at the heart of EDM, enabling the machining of intricate shapes and hardened materials with unparalleled precision and efficiency.
Main Types of EDM
EDM can be broadly classified into two main types, distinguished by the shape of the electrode:
Wire EDM (WEDM)
Wire EDM uses a wire-shaped, elongated electrode (approximately 0.2mm in diameter). By applying discharge while the taut wire electrode is close to the workpiece, the workpiece is cut (or melted) like with a wire saw. The trajectory of the wire electrode can be numerically controlled, allowing for precise cutting of the workpiece into any desired shape. The advantages of wire EDM include the absence of the need to machine the electrode and the ability to process complex shapes that cannot be achieved by cutting.
However, the machining precision depends on the wire diameter. Thinner wire electrodes allow for finer machining, but the machining speed decreases due to lower current values. Conversely, thicker wire electrodes enable faster machining but reduce machining precision. When using thick wire electrodes, it is possible to complete the machining in the first cut, but depending on the application, multiple cuts with different wire diameters may be necessary, resulting in variations in machining time and precision. Wire EDM (WEDM) is used in the manufacture of press molds and the machining of carbide tool tips, among other applications.
Die-sinker EDM (or Conventional EDM)
Die-sinker EDM involves using an electrode machined to the desired shape, which functions as a mold. By bringing the mold and the workpiece close together and applying discharge, the workpiece melts according to the shape of the mold. In other words, the shape of the mold is transferred to the workpiece.
Using die-sinker EDM allows for bottomed machining, which is impossible with wire EDM. Additionally, by refining the shape of the “mold,” complex shapes such as deep grooves and corners can be achieved. On the other hand, since an electrode must be made each time to match the desired shape, it can be costly and time-consuming.
Hole-drilling EDM
Hole-drilling EDM, also known as EDM drilling or EDM hole drilling, is a machining process used to create precise, small, and deep holes in metal workpieces that are difficult to machine using traditional methods, such as hardened steels or exotic alloys. It offers high accuracy, good surface finish, and the ability to create complex shapes and features.
Advantages of Electrical Discharge Machining
– Machining Hard Materials: Can process regardless of material hardness
– Complex Geometries: Able to achieve high precision even with complex shapes
– No Contact Forces: Minimal stress on workpieces
– High Precision and Accuracy: Capable of machining shapes difficult to achieve with cutting processes
EDM can process materials that conduct electricity, making it suitable for manufacturing components such as molds that require high strength. Furthermore, EDM enables precise machining down to the micron level. Compared to cutting processes, EDM offers extremely high accuracy and can realize shapes like threading and spirals. Additionally, it’s possible to finely adjust the surface roughness of the machining by changing the electrical conditions.
Another advantage of EDM is the minimal stress it imposes on workpieces since there is no physical contact between the electrode and the workpiece. This reduces the risk of machine failure compared to other machining methods. Workpieces are constantly cooled by the machining fluid, eliminating concerns about deformation due to discharge heat.
Moreover, in the case of die-sinking EDM, it’s possible to machine shapes that are difficult with milling or cutting processes. For example, it’s possible to approach angles of holes or depressions as close to right angles as possible and to process undercut areas.
Disadvantages of Electrical Discharge Machining
– Slower Speed: Time-consuming process
– High cost
– Conductivity Requirement: Unable to process materials that do not conduct electricity
– Wear on Electrodes: Surface becomes rough after machining
EDM requires more time for processing, typically at a rate of 2 to 5 mm per minute. Some companies strategically plan machining by prioritizing parts that can be processed quickly during daytime when workers are present, and parts with longer processing times during nighttime when workers are absent. Furthermore, EDM equipment is expensive, and consumables like wire electrodes contribute to the overall cost. Considering processing time and cost, EDM is suitable for producing high-precision components in small batches but may not be ideal for mass production.
Additionally, materials that do not conduct electricity cannot be machined with EDM. It’s also important to note that the machined surface can become rough, which differs from surfaces produced by cutting processes and requires attention during machining.
Differences Between Electrical Discharge Machining and Electrochemical Machining
While both electrical discharge machining and electrochemical machining (ECM) involve applying voltage between the workpiece and the electrode, the energy used to dissolve the workpiece differs between the two methods.
As explained earlier, EDM induces arc discharge in an insulating machining fluid, using its “thermal energy” to melt the workpiece. In contrast, ECM involves electrolyzing the workpiece in an electrolyte solution, ionizing atoms in the anode (workpiece) for removal. This is a method that utilizes “chemical reaction (chemical energy).” It can also be said that there is a difference between causing discharge in a non-conductive liquid and moving electrons in a conductive liquid.
ECM, unlike EDM, is often used for deburring workpieces. Additionally, it features characteristics such as improved machining accuracy, speed, and surface roughness with higher current density.
Conclusion
Electrical discharge machining artificially generates discharge phenomena between the workpiece and the electrode, gradually melting the workpiece with discharge heat. It is used in the production of molds for resin injection molding, nested molds, and machine parts made of difficult-to-machine materials. There are two main types of electrical discharge machining: wire EDM and die-sinking EDM, each offering different types of electrodes and machinable shapes.
Electrical discharge machining offers advantages such as the ability to machine hard materials as long as they conduct electricity and high machining accuracy. However, it also has disadvantages such as long processing times. Let’s utilize electrical discharge machining after understanding its advantages and disadvantages.