BLOG » What is Plastic Deformation Processing? Process Overview
What is Plastic Deformation Processing? Process Overview
Plastic deformation processing is a widely-used metalworking method alongside machining, cutting and casting. By applying force to a material and deforming it, this technique enables the creation of diverse products ranging from everyday tools to specialized industrial components. In this blog article, we’ll talk about the fundamentals of plastic deformation processing, exploring its various methods and showcasing examples of its applications in modern manufacturing. Whether you’re a seasoned professional or new to the field, understanding this process is key to appreciating its impact and potential in the industry.
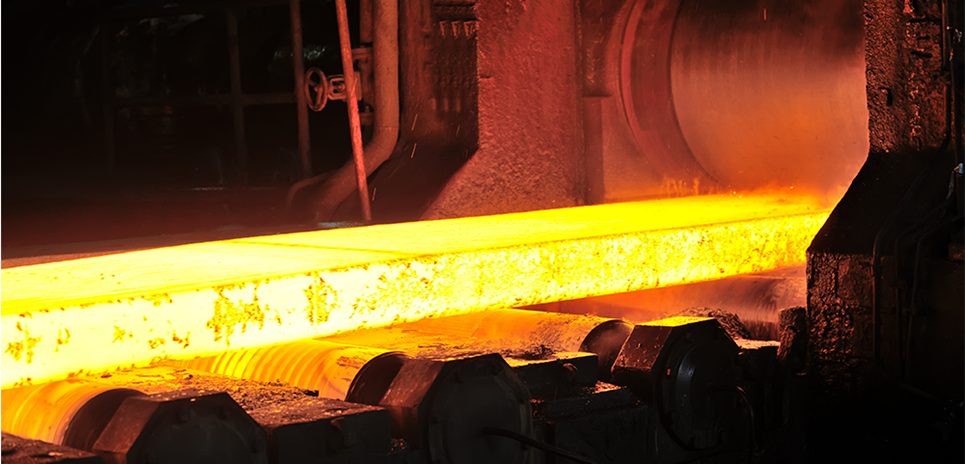
What is Plastic Deformation Processing? One of Humanity’s Oldest Metalworking Techniques
Plastic deformation refers to the property of a material to retain a new shape after a force is applied and then removed. Initially, when a force is applied to a material, it deforms elastically. This elastic deformation is not permanent, and if the force is removed at this stage, the material reverts to its original shape. However, if the force is increased beyond a certain threshold, plastic deformation occurs, and the material retains the new shape even after the force is removed. This property is utilized in plastic deformation processing to shape products.
The forging process used to create Japanese swords is a prime example of plastic deformation processing. This method dates back to ancient times, with artifacts from around 3000 BC in ancient Egypt showing evidence of forging. Today, it is used in a wide range of applications, from everyday items like golf club heads to specialized components like engine crankshafts and rocket parts.
Advantages of Plastic Deformation Processing
Improvement of Material Properties:
The large deformation of the material reduces defects like residual stresses and improves strength through work hardening. Unlike machining, plastic deformation does not cut through the material’s structure, resulting in stronger final products suitable for high-stress applications.
Shorter Processing Time:
Using molds allows for faster production, making it ideal for mass production.
High Material Yield:
Unlike machining, which generates a lot of waste material, plastic deformation minimizes scrap. This reduces the amount of raw material needed, lowering costs.
Unique Products:
Certain products, such as steel plates produced in steel mills, can only be made through plastic deformation.
Disadvantages of Plastic Deformation Processing
High Equipment Costs:
The need to apply significant force to deform materials requires large-scale machinery and heating equipment. There are also costs associated with producing and maintaining molds.
Lower Dimensional Accuracy:
Depending on the type of plastic deformation and the shape of the parts, dimensional accuracy is generally lower than machining. Therefore, plastic deformation is often used to create rough shapes, followed by additional machining for precise dimensions.
Types of Plastic Deformation Processing and Product Examples
Plastic deformation processing encompasses various methods, each with unique applications and advantages. Here are the main types:
Forging
Forging involves shaping a product using molds and tools, often utilizing forging presses or air hammers. This method is particularly suited for creating high-strength components. Examples of forged products range from household tools like wrenches to critical automotive engine parts and large components for rockets.
Rolling
Rolling involves passing material between rotating rolls to compress and elongate it. Rolling mills are used for this process. Typical products include steel plates, relatively thick bars, and pipes produced in steel mills.
Pressing
Pressing uses molds to shape sheet metal into desired forms. Press machines facilitate this process, producing items like steel furniture, cases, and automotive bodies.
Extrusion
Extrusion compresses material in a chamber and forces it through a die to create long products with a constant cross-sectional shape. Extrusion presses are employed for this method. Examples include aluminum window frames and aircraft components.
Drawing
In contrast to extrusion, drawing pulls material through a die to reduce its cross-sectional area, forming long products with specific shapes. Wire drawing machines and drawing benches are used. Products include wires, square bars, and pipes.
Rrolling
Thread rolling, or rolling in general, involves pressing rotating tools called rolling dies against rotating materials to shape them. Rolling machines perform this process, commonly used for producing threaded bolts and gears, which require high strength and mass production.
Conclusion
This overview covers the basics of plastic deformation processing, its types, and product examples. The unique advantages of plastic deformation processing, such as achieving near-final shapes with fewer steps, high-strength products, and cost-effective mass production, distinguish it from other methods. When selecting a processing method, consider the shape and function of the components to include plastic deformation processing as a viable option.