BLOG » How to Choose the Best Corrosion Resistance Metals
How to Choose the Best Corrosion Resistance Metals
When selecting materials for parts used in environments where corrosion resistance is critical, do you always pick the same metal? If so, it might be time to reconsider your choices. Corrosion resistance plays a key role in reducing maintenance costs and preventing a decline in durability, which can shorten the lifespan of your products.
Various methods exist to prevent corrosion, such as using metals that are inherently resistant to rust or applying surface treatments that form a protective layer on the metal.
In this guide, we’ll introduce you to nine different metals, with and without surface treatments, and explain their unique characteristics, advantages, and considerations. You might discover some lesser-known features of these materials that could make a big difference in your next project.
Metals that Rust vs. Metals that Resist Corrosion
All metals are prone to rusting, but the degree to which they rust depends on their type and the environmental conditions they’re exposed to. For example, metals exposed to moisture or saltwater environments tend to corrode faster.
Rust Formation
Rust occurs when metal reacts with oxygen in the air to form an oxide. When metal comes into contact with water, it ionizes, making it more susceptible to oxidization. The ease with which metal rusts is determined by its tendency to ionize (a concept known as ionization tendency). Simply put, metals with a higher ionization tendency, such as lithium or potassium, rust more easily, while metals like gold or platinum, which have a lower ionization tendency, are more resistant to corrosion.
3 Types of Corrosion-Resistant Metals
Although most metals rust, some metals are more resistant to corrosion due to their natural properties. Generally, there are three types of “corrosion-resistant” metals:
- Metals That Do Not Rust (e.g., Gold, Platinum)
These metals have low ionization tendencies, making them inherently resistant to rust. However, they are often expensive, so using them requires careful consideration. - Metals that Form a Passive Oxide Layer (e.g., Aluminium, Titanium, Nickel, Stainless Steel)
Some metals, like aluminium and titanium, form a passive oxide layer on their surface when exposed to oxygen. This layer prevents further reaction with oxygen, protecting the underlying metal from corrosion. Stainless steel, for instance, benefits from the chromium added to it, which forms a protective oxide film. - Metals Where Rust Acts as a Protective Layer (e.g., Copper, Zinc)
Like metals that form a passive oxide layer, these metals protect their inner layers from further corrosion. However, the oxide film on these metals is not as strong, and it can be easily removed by acidic substances such as vinegar.
Types of Anti-Corrosion Surface Treatments
To prevent corrosion in metals that are more susceptible to rust, surface treatments are applied. The most common method is to form a protective layer on the metal’s surface, preventing exposure to air and moisture. There are two main categories of surface treatments: organic and inorganic coatings.
Organic Coatings (e.g., Paint, Oil)
Painting is a classic example of organic coating. Applying oils or wrapping parts with rubber or plastic are other common organic methods used to protect metal surfaces.
Inorganic Coatings (e.g., Plating, Chemical Treatment)
Plating is a method of applying a thin metal layer, such as chrome or zinc, to protect the base metal. These coatings are either passivating metals (like chromium) or sacrificial metals (like zinc), which corrode first, protecting the underlying metal. Chemical treatments, like chromate or anodizing (for aluminum), are also common for enhancing corrosion resistance.
5 Surface Treatments for Corrosion Resistance and 4 Highly Corrosion-Resistant Metals
Let’s rank the corrosion resistance of nine different metals from highest to lowest and compare their strength, wear resistance, and magnetic properties. Clicking on “Surface Treatment” or “Materials” will provide more detailed information on each. Use this guide to make informed decisions for your next material selection.
- Surface Treatments for Corrosion Resistance
- Surface treatments effectively shield metals from oxidation, which occurs when they come into contact with oxygen. Keep in mind that surface treatments add cost and increase production time.
Material | Surface Treatment | Corrosion Resistance | Coating Strength | Abrasion Resistance | Magnetic | Features |
---|---|---|---|---|---|---|
Iron-based (SPCC/SPHC/SS400) | Trivalent chromate (white/black) | Strong | Strong | Strong | Good | Has a self-repair function for small scratches etc. |
Electroless Nickel | Strong | Good | Strong | Ok | The plating layer is hard and scratch-resistant, with high electrical resistance | |
Coating | Strong | Ok | Ok | Good | Various colors and glosses available depending on the type of paint | |
Aluminum (A5052) | Anodized (white/black) | Strong | Ok | Not Good | Not Good | Less discoloration over time compared to painting or plating |
Iron-based (SPCC/SPHC/SS400) | Black Oxide | Ok | Not Good | Ok | Strong | Minimal effect on dimensions, improved rust prevention |
Corrosion-Resistant Metals
Metals that don’t require surface treatments reduce both costs and production time. However, they typically offer less corrosion resistance than treated metals.
Material | Surface Treatment | Corrosion Resistance | Material Strength | Abrasion Resistance | Magnetic | Features |
---|---|---|---|---|---|---|
Stainless steel EN 1.4301 equiv. (SUS304) | – | Good | Strong | Good | Ok | It is also tough and can be used in a wide range of applications. |
Aluminum A5052 | – | Good | Not Good | Not Good | Not Good | Excellent seawater resistance |
Stainless steel SUS430 | – | Ok | Strong | Good | Good | Less workable than SUS304 |
Steel-based SECC (Electro-galvanized steel sheet) | Electro-galvanized (※2) | Ok | Good | Good | Good | Depending on the type, it goes well with paint. |
Example: Black Oxide Coating
- Material: SPCC (SPHC)
- Size: W150 × D150 × H4.5
- Surface Treatment: Black Oxide Coating
- Corrosion Resistance: Ok
- Magnetic Properties: Strong
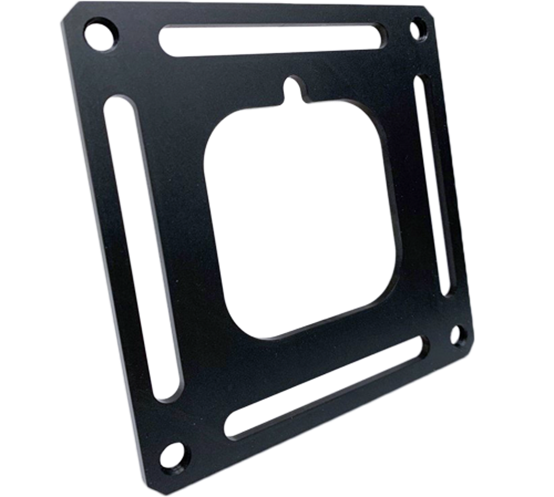
This iron-based SPCC/SPHC with blackened surface is affordable and commonly used for temporary protection during assembly. Adding oil can further enhance corrosion resistance, making this method useful for automotive and industrial applications. However, color variations can occur due to surface imperfections, and it’s recommended for indoor use only, as it has lower corrosion resistance compared to other treatments.
Example: Stainless Steel (EN 1.4301 equiv. - SUS304)

- Material: EN 1.4301 equiv. (SUS304)
- Size: W117 × D48 × H53
- Surface Treatment: None
- Corrosion Resistance: good
- Magnetic Properties: Ok
EN 1.4301 equiv. stainless steel (SUS304) is widely used for its excellent corrosion resistance and strength. Its semi-glossy finish makes it suitable for products that require both aesthetic appeal and durability, such as kitchen equipment and decorative items. However, it tends to attract fingerprints and may corrode when in contact with rusted iron particles.
Conclusion
Selecting the right material for corrosion resistance involves more than just considering cost and lead times. Understanding the properties of different metals and surface treatments can help you make informed decisions that extend the lifespan of your products while maintaining their performance. For instant quotes on surface treatments or materials, upload your 3D CAD data to meviy FA Mechanical Parts today!