BLOG » Surface Roughness Options Available for CNC Milled Parts: Ra3.2, Rz12.5
Surface Roughness Options Available for CNC Milled Parts: Ra3.2, Rz12.5
Surface roughness plays a critical role not only in managing the finish and appearance quality of a machined product but also in determining its overall durability and operational efficiency. To cater to customer demands, meviy has introduced machining services for surface roughness levels of Ra3.2 and Rz12.5 for CNC milled parts on June 5, 2023. These new roughness options are available for both plastic and metal components.
With meviy’s easy-to-use interface, you can now order parts with Ra3.2 or Rz12.5 surface roughness for CNC milling directly from the platform by following a few simple steps.
What is Surface Roughness?
Surface roughness is a critical parameter in engineering and manufacturing that refers to the irregularities or deviations present on the surface of a material. These irregularities are typically caused by the machining or finishing processes used to create the part. Surface roughness is quantified using standardized measurements, most commonly expressed as Ra (Arithmetic Mean Roughness) or Rz (Ten-Point Mean Roughness), and is measured in micrometers (µm).
Ra is the average height of the peaks and valleys on the surface over a specified area, providing a general indication of the smoothness. On the other hand, Rz represents the average height difference between the five highest peaks and the five lowest valleys, making it a more detailed representation of the surface profile. These measurements are essential in determining the functional and aesthetic qualities of a part. For example, a smoother surface (low Ra or Rz) is often required for components that need to reduce friction, improve wear resistance, or ensure proper sealing. Conversely, a slightly rougher surface may be advantageous for applications requiring better adhesion, such as painting or bonding.
Surface roughness impacts not only the appearance of a part but also its functionality, including how parts fit together, how they interact with other components, and their overall performance in mechanical systems. In industries like automotive, aerospace, and medical devices, maintaining the correct surface roughness is critical to ensuring safety, reliability, and efficiency. By understanding and controlling surface roughness, manufacturers can enhance product longevity, reduce maintenance costs, and improve operational efficiency in various applications.
Benefits of Ra3.2 or Rz12.5 Surface Roughness for CNC Milled Parts
Opting for a surface roughness of Ra3.2 or Rz12.5 offers several key advantages, particularly in precision applications where performance, reliability, and durability are critical. A surface roughness of Ra3.2 (Arithmetic Mean Roughness) ensures a smooth yet functional surface, minimizing friction between moving parts, which reduces wear and tear and extends the product’s lifespan. This level of roughness is also ideal for components that require proper sealing, as it provides a balance between smoothness and the ability to retain lubricants, enhancing operational efficiency. For industries like automotive and medical devices, Ra3.2 or Rz12.5 is often the preferred choice for surfaces where high accuracy and consistent performance are required, such as precision machined plates, mounting points, or components used in hazardous or high-precision environments.
In addition, Rz12.5 (Ten-Point Mean Roughness), which measures the height difference between peaks and valleys, provides an optimal profile for applications where slightly textured surfaces improve functional adhesion, such as painting, bonding, or coating. This level of roughness also helps in dispersing stresses evenly across the surface, reducing the risk of material fatigue. Furthermore, achieving Ra3.2 or Rz12.5 through high-precision machining ensures consistent quality and improved aesthetic appearance, making the components suitable for both functional and visible parts. By meeting these standards, manufacturers can deliver products that comply with industry requirements while optimizing performance, reliability, and cost-effectiveness.
How to Select Parts with Surface Roughness Ra3.2, Rz12.5 on meviy
Ordering parts with enhanced surface roughness has never been easier. Follow these steps:
- In the meviy interface, click on the default Ra6.3 surface roughness option in the tree menu.
- Select Ra3.2, Rz12.5 from the dropdown list.
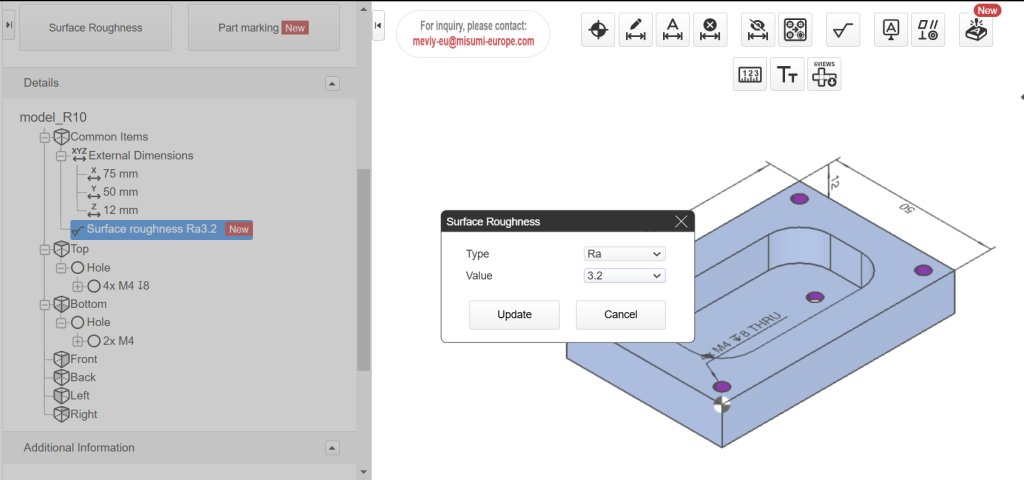
Available Materials for CNC Milled Parts with Ra3.2, Rz12.5
Metals
Material | Specific Material | Surface Treatment |
---|---|---|
Iron | SS400 | No treatment Black oxide coating Electroless nickel |
S50C (equivalent) | ||
SS400 annealed material | ||
S50C (equivalent) (tempered material) | ||
Pre-hardened steel | NAK55 (equivalent) | No treatment |
Aluminum | A2017 | No treatment White anodized Black anodized Black anodized (matte) |
A5052 | ||
A6061 | ||
A7075 | ||
Stainless Steel | EN 1.4305 equiv. (SUS303) | No treatment |
EN 1.4301 equiv. (SUS304) | ||
EN 1.4401 equiv. (SUS316) | ||
EN 1.4016 equiv. (SUS430) |
Plastic
Material | Specific Material | Surface Treatment |
---|---|---|
Plastic | Polyacetal (white) | No treatment |
Polyacetal (black) | ||
MC Nylon (Blue) | ||
MC Nylon (Ivory) | ||
MC Nylon (black/gray) | ||
Fluorine (white) | ||
Ultra-high molecular weight polyethylene (white) | ||
Ultra-high molecular weight polyethylene (black) | ||
ABS (natural color) | ||
PEEK (gray brown) |
Exclusions for Ra3.2, Rz12.5 Surface Roughness
Certain machining methods, material types, and design conditions may prevent achieving Ra3.2 or Rz12.5 surface roughness. Examples of exclusions include:
- Hole bottom surfaces and non-precision hole sidewalls.
- Curved surfaces (R areas) and counterbore sinkhole areas.
If you require these specific surfaces, please consult our customer support team for alternative solutions.
Conclusion
In conclusion, achieving precise surface roughness, such as Ra3.2 or Rz12.5, is a critical factor in delivering high-quality, reliable, and efficient components for a wide range of industries. Whether it’s enhancing the durability and performance of machined parts or ensuring optimal functionality and safety in demanding applications, these surface roughness levels offer tangible benefits that go beyond aesthetics. By utilizing advanced machining techniques, manufacturers can meet these strict surface quality standards while providing customers with parts that align with their specific needs and industry requirements. With the introduction of Ra3.2 and Rz12.5 surface roughness options in our services, we aim to empower our customers to achieve greater efficiency, performance, and longevity in their products. Ready to take your projects to the next level? Explore how these precision surface finishes can optimize your next design today!