BLOG » What is Grinding? Applications, Types, and Features
What is Grinding? Applications, Types, and Features
Grinding is a machining process that uses an abrasive wheel (grinding wheel) to remove material from a workpiece. This process is typically used as a finishing method, improving surface smoothness and dimensional precision. Unlike cutting, grinding allows for high accuracy and is commonly applied to hard materials that are difficult to cut with conventional tools.
In this blog, we’ll explore different types of grinding processes, the benefits and drawbacks, comparisons with other machining methods, and common challenges encountered during grinding operations.
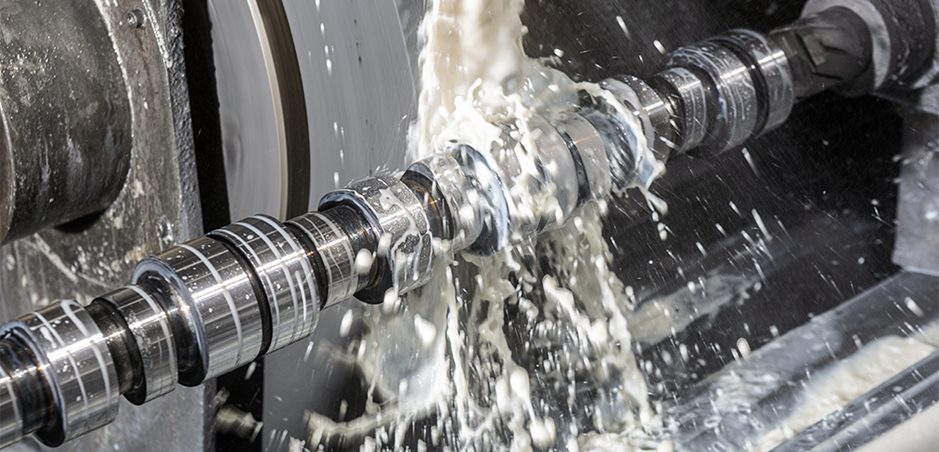
What is Grinding?
Grinding is classified under “subtractive machining” methods. It involves using a grinding wheel to shave off small amounts of material from the workpiece surface through high-speed rotation. While this method is more time-consuming than traditional cutting methods, it offers greater precision and a smoother finish.
Grinding can handle materials that are difficult to machine, such as hardened steels and other tough metals, and is commonly used as a final finishing step after cutting processes.
Advantages of Grinding
- High Dimensional Precision: Grinding allows for precise control over material removal, achieving tolerances in the micrometer range and producing very smooth surfaces.
- Processing Hard Materials: The process can effectively machine hard materials like carbide alloys that are difficult to cut by other means.
- Consistent Surface Finishing: It can improve surface smoothness, giving the workpiece a polished and uniform appearance.
Disadvantages of Grinding
- Longer Processing Time: Grinding, while highly precise, tends to be a slower process, making it less efficient for larger material removals.
- Heat Generation: Grinding generates significant heat due to friction between the abrasive wheel and the workpiece, requiring proper cooling to prevent part damage.
- Potential for Accidents: High-speed rotation of the abrasive wheel presents a risk of accidents if not handled correctly.
Types of Grinding Processes
- 1. Surface Grinding: This is one of the most common methods, primarily used to create a flat surface. The workpiece is fixed, and the grinding wheel rotates across it to remove material.
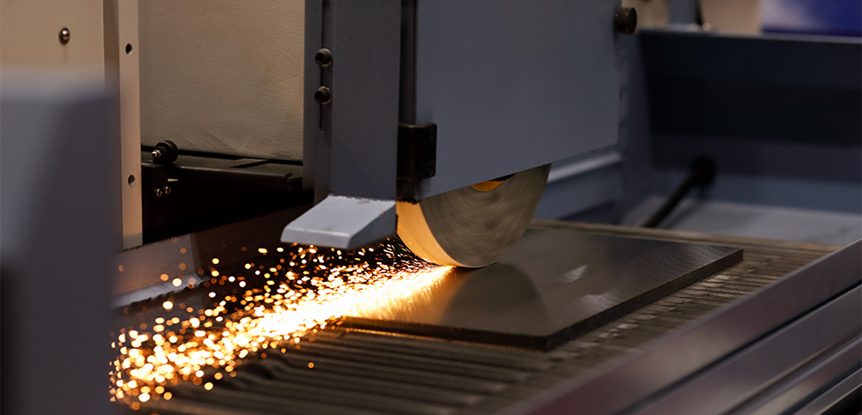
- 2. Cylindrical Grinding: Used to grind the outer surface of cylindrical workpieces. The workpiece rotates, and the abrasive wheel is applied to remove material along the surface.
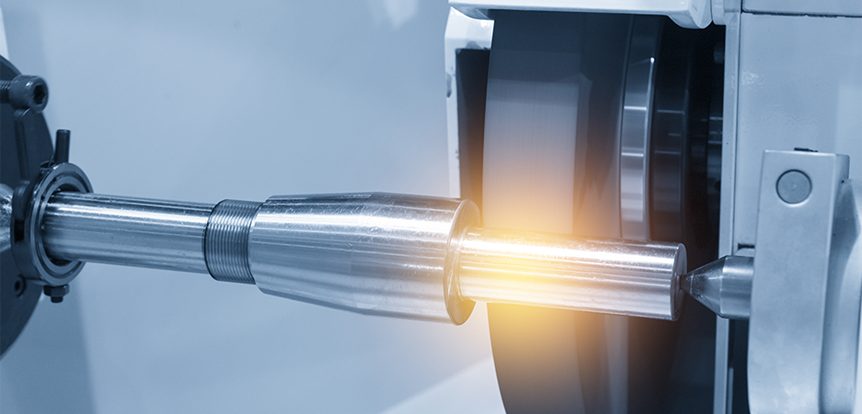
- 3. Internal Grinding: This method is used to grind the inside surfaces of cylindrical workpieces, such as hollow tubes or pipes.
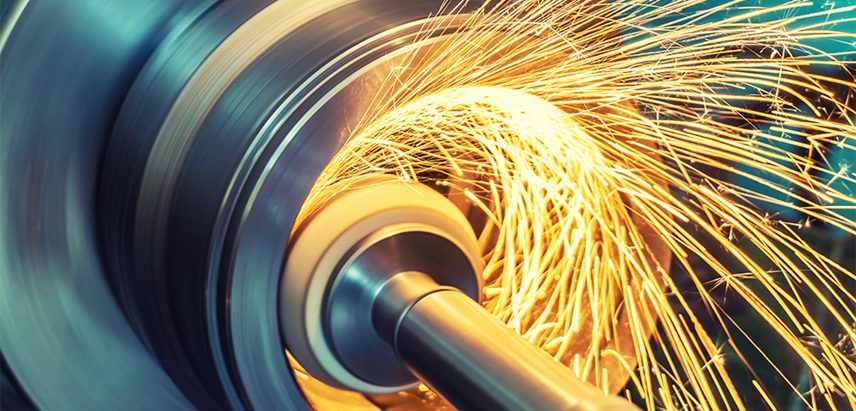
- 4. Centerless Grinding: Unlike cylindrical grinding, this process doesn’t require workpiece support centers. The workpiece is supported by a blade and controlled by a regulating wheel, allowing for continuous high-volume grinding.
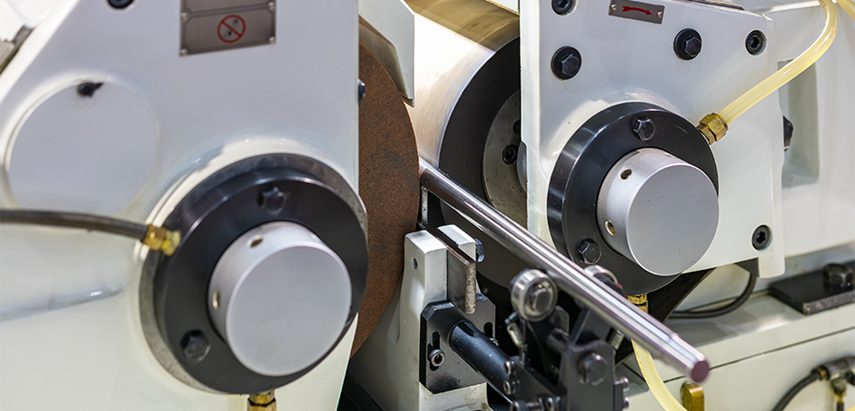
- 7. Gear Grinding: This process is specifically used for shaping gear teeth and involves using special grinding wheels to finish gears for enhanced accuracy and performance.
- 6. Cutting: Using thin abrasive wheels similar to those on grinders, cutting is applied to divide hard materials or large cylindrical parts that are difficult to machine with traditional tools.
Difference Between Cutting and Grinding
Both cutting and grinding are machining processes used to remove material, but they differ significantly in method and precision.
- Cutting vs. Grinding: Cutting uses a blade or tool to quickly remove large amounts of material, shaping the workpiece. It’s faster but less precise than grinding, which uses an abrasive wheel to refine and smooth the surface with high accuracy. Grinding is ideal for hard-to-cut materials and intricate details, making it the go-to process for finishing touches.
- Polishing vs. Grinding: Grinding changes the shape of the material, while polishing is more about surface refinement, focusing on giving it a smooth, mirror-like finish. Polishing can use abrasive particles or electrolysis for delicate metal surfaces.
Common Grinding Challenges
- Clogging: Soft metals like aluminum may clog the grinding wheel, reducing effectiveness.
- Blunt Wheel: Prolonged use can wear down the wheel’s abrasive particles, requiring adjustments to maintain sharpness.
- Chipping: Weak bonding agents in the wheel can cause abrasives to chip off prematurely, affecting performance.
Conclusion
Grinding is an essential finishing process in machining, valued for its precision and ability to work with hard materials. While slower than other methods, it produces superior surface finishes and accuracy. Grinding processes come in various forms, each suited for different applications, and understanding the benefits and limitations can help manufacturers choose the right grinding method for their specific needs.