BLOG » The Benefit of Red Coating in Manufacturing: Enhancing Functionality and Safety
The Benefit of Red Coating in Manufacturing: Enhancing Functionality and Safety
When it comes to manufacturing, functionality and safety are two crucial aspects that guide material and coating.
One topic that has sparked particular interest is the application of red anodising for CNC milled parts and red wet paint for sheet metals.
This article delves deeper into the specifics of the benefits of red coatings, why they matter, and how customers can apply these coatings to enhance safety, organization, and functionality in their equipment and processes.
The Psychology and Benefits of Red
Red is one of the most powerful and attention-grabbing colors in the spectrum. Its use in industrial and manufacturing applications is rooted in psychology and practicality:
- Universally Recognized Warning Signal:
Red is associated with danger, caution, and prohibition across cultures and industries. It’s the color of stop signs, fire extinguishers, and emergency buttons, making it ideal for hazardous or high-risk areas.
- Enhanced Visibility:
The vibrant hue of red stands out against most backgrounds, ensuring that components coated or painted in red are easily identifiable, even in busy or cluttered environments.
- Improved Organization and Clarity:
In complex equipment or systems, red can help designate critical areas, stopping points, or restricted zones. This makes workflows more efficient and reduces confusion among operators.
- Durability and Longevity:
Red anodising or wet painting not only adds the symbolic value of the color but also provides protective benefits to the underlying material. These coatings improve corrosion resistance, wear resistance, and overall durability of the parts.
Applications of Red Coatings and Paints
Red Anodised Coatings for CNC Machined Plates:
Red anodising is a popular surface treatment for aluminum CNC milled parts. The process creates a durable, oxide layer on the surface, resulting in:
- Corrosion resistance: Ideal for outdoor or high-moisture environments.
- Scratch resistance: Ensures long-term visual and functional performance.
- Aesthetic appeal: The vibrant red finish is clean, professional, and highly visible.
Use Case Examples:
- Safety barriers in manufacturing equipment.
- Control panels for emergency stop systems.
- Highlighting machine edges to prevent accidental contact.
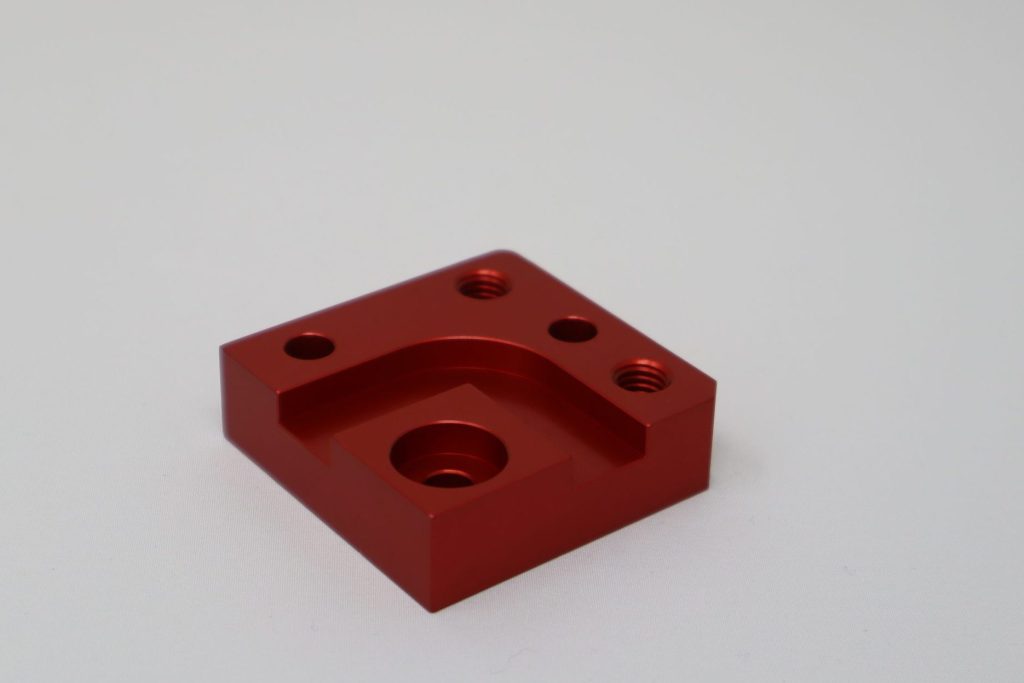
Red Wet Paints for Sheet Metals:
Wet painting offers a versatile and cost-effective option for adding red coatings to sheet metals. Key advantages include:
- Customizability: Wet paints are available in a variety of shades and gloss levels.
- Adherence to diverse substrates: Ideal for materials that cannot undergo anodising, such as steel or composite metals.
- Resistance to chemicals and wear: Protects against environmental factors and frequent use.
Use Case Examples:
- Marking access points on enclosures.
- Indicating “restricted zones” on production floors.
- Creating visual contrasts in medical or precision instruments.
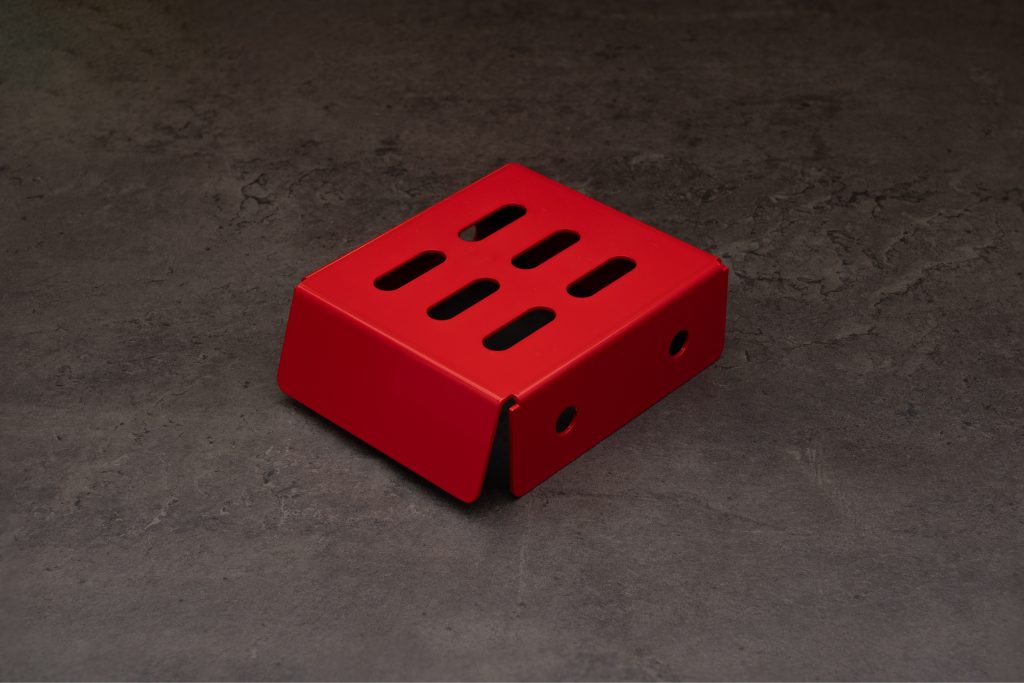
How to Apply Red Coatings – Best Practices
To ensure the red coatings and wet paints deliver optimal functionality, consider the following application tips:
Select the Right Coating:
- Use red anodising for aluminum parts that require a protective, durable, and decorative coating.
- Use red wet paint for materials like steel or where cost-effectiveness is a priority.
Match the Coating to the Environment:
- For outdoor use or corrosive environments, prioritize anodised coatings for their superior corrosion resistance.
- For indoor environments, wet paint may provide sufficient protection while being budget-friendly.
Incorporate Red Strategically:
- Place red-coated components in areas requiring immediate attention, such as safety zones, stopping points, or hazard areas.
- Use red in combination with other color-coded components to create a coherent system of visual guidance.
Conclusion: Why Red Coatings Matter
Red coatings and paints for machined plates and sheet metals are more than just a design choice—they are essential for safety, functionality, and efficiency. By providing clear visual cues, improving organization, and enhancing the durability of components, red coatings play a critical role across industries.
At meviy, we specialize in delivering high-quality red coating solutions tailored to your needs. Our red anodising for CNC-milled components offers superior durability, corrosion resistance, and a vibrant finish ideal for precision parts. For sheet metal applications, our red wet paint services provide excellent coverage and a professional-grade appearance, ensuring both aesthetics and functionality.
Whether you’re in the automotive, medical, or industrial sector, the right red coating can make all the difference in creating a safer and more functional work environment. If you’re looking to incorporate red anodised or painted parts into your equipment, consult with us to explore the best options for your application. At meviy, we’re committed to providing coatings that enhance both the performance and visual impact of your components.