BLOG » New at meviy: meviy launches new stainless steel materials and surface treatments
New at meviy: meviy launches new stainless steel materials and surface treatments
As we move into the final quarter of the year, we’re excited to announce the launch of new materials and surface treatments coming this October. These innovative options are designed to offer enhanced performance, durability, and versatility across a range of CNC-machined and fabricated components. Whether you’re looking for improved corrosion resistance, higher strength, or aesthetic enhancements, these new offerings will broaden the possibilities for customization and optimization in your production processes. Stay tuned as we introduce advanced alloys, cutting-edge treatments, and specialized finishes aimed at meeting the most demanding industrial needs.
In this blog, we’ll explore the details of our upcoming material releases and treatments, explaining how they can elevate your components to the next level in terms of performance, functionality, and appearance.
New Stainless Steel Materials
We are thrilled to announce the release of three new high-performance stainless steel materials that are now available for your CNC machining and engineering projects: EN 1.4305 equiv. (annealed material), EN 1.4301 equiv. (annealed material), and EN 1.7220 equiv. (heat-treated to 26-32 HRC). These materials bring a unique set of properties and advantages, making them ideal for a wide variety of applications. Let’s take a closer look at the features and benefits of each material.
EN 1.4305 equiv. (Annealed Material) – equivalent to SUS303
EN 1.4305, equivalent to SUS303, is a free-machining austenitic stainless steel. The material is designed to have enhanced machinability due to its sulfur content, which allows for easy cutting and shaping, making it an ideal choice for applications that require high-precision machining. In its annealed form, EN 1.4305 equiv. exhibits increased softness and ductility, which helps to further improve its machinability. It is commonly used in the production of screws, bolts, fasteners, and other components where ease of machining is crucial. Additionally, it offers good corrosion resistance in mild environments, although it is slightly lower than other stainless steels due to the higher sulfur content.
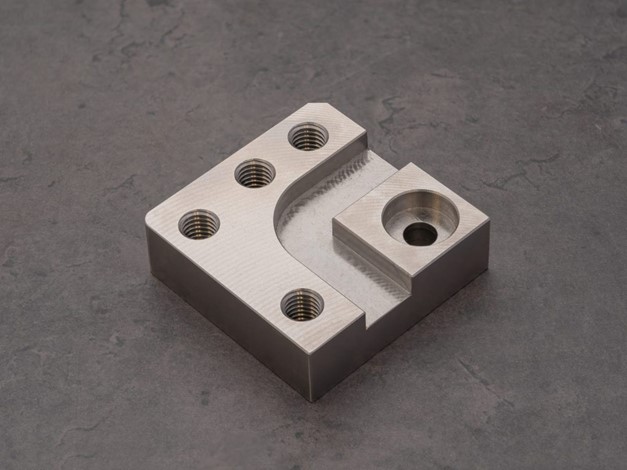
EN 1.4301 equiv. (Annealed Material) – equivalent to SUS304
EN 1.4301, equivalent to SUS304, is one of the most widely used types of stainless steel due to its excellent balance of corrosion resistance, formability, and strength. The annealed version of EN 1.4301 equiv. provides enhanced ductility and toughness, making it easier to work with during the manufacturing process. This material is widely used in applications where both strength and corrosion resistance are required, such as in kitchen equipment, chemical containers, and architectural structures. It is also suitable for use in environments where the material will be exposed to moisture or other corrosive agents, offering excellent durability over time.
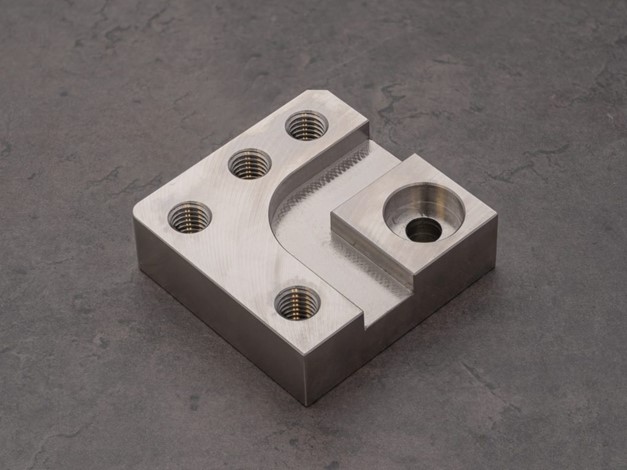
EN 1.7220 equiv. (26–32 HRC) – equivalent to SCM440
EN 1.7220, equivalent to SCM440, is a high-strength alloy steel known for its excellent mechanical properties, especially after heat treatment. When treated to a hardness level of 26 to 32 HRC, EN 1.7220 equiv. exhibits an excellent balance of toughness, wear resistance, and machinability. This makes it ideal for high-stress applications like gears, shafts, and other heavy-duty components where high strength and wear resistance are paramount. The heat-treated version of this material is commonly used in the automotive and aerospace industries due to its ability to withstand high stress and fatigue.
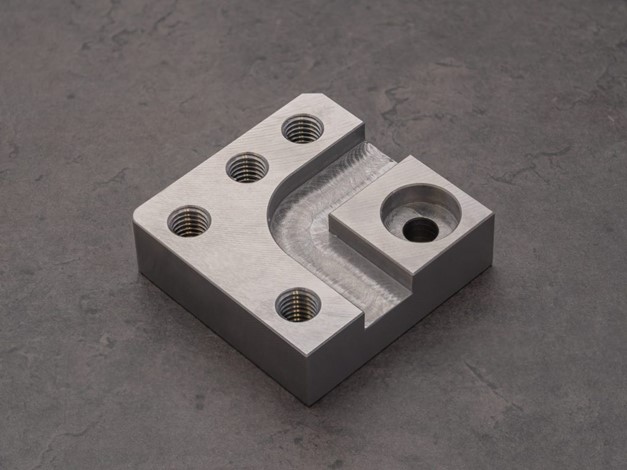
New Surface Treatments
We are excited to announce the release of three new surface treatments designed to enhance the performance, durability, and longevity of metal components: Hard Anodise (Clear), LTBC-Surface Treatment, and Phosphating. Each of these treatments offers distinct advantages for various industrial applications, providing increased resistance to wear, corrosion, and environmental factors. Let’s explore the details of each surface treatment and how they can improve your machining and manufacturing processes.
Hard Anodise (Clear)
Hard anodising creates a dense, wear-resistant surface layer on aluminum parts, significantly boosting their hardness and resistance to abrasion. Our Hard Anodise (Clear) treatment goes a step further by offering this enhanced durability without affecting the natural color of the aluminum, maintaining a sleek, clear finish. This makes it ideal for applications where both aesthetics and performance matter, such as aerospace, automotive, and high-performance industrial components. In addition to its hardness, this treatment offers excellent corrosion resistance, making it suitable for harsh environments.
LTBC-Surface Treatment
The LTBC-Surface Treatment is a low-temperature black chrome coating that provides exceptional wear resistance and low friction. This surface treatment is ideal for components that operate under extreme mechanical stress or frictional contact. The LTBC treatment offers a sleek black finish while enhancing surface hardness and extending the lifespan of components in high-load or high-velocity applications. Additionally, the treatment ensures superior anti-corrosive properties, making it perfect for automotive, aerospace, and industrial applications where precision and reliability are paramount.
Phosphating
Phosphating, also known as phosphate conversion coating, is a surface treatment that enhances the corrosion resistance of metal components by applying a thin phosphate layer. This layer not only protects the metal from rust and oxidation but also serves as an excellent base for further coatings, such as paint or powder coatings. Phosphating is commonly used in the automotive and heavy machinery industries to protect steel parts, bolts, and fasteners from environmental wear. Additionally, it improves lubrication during assembly and provides better adhesion for additional coatings, making it a versatile and cost-effective surface treatment for mass production.
Conclusion
Our newly released materials and surface treatments represent significant advancements in the realm of precision machining and manufacturing. From the high-strength and corrosion-resistant qualities of EN 1.4305 equiv. and EN 1.4301 equiv., to the wear-resistant EN 1.7220 equiv. material, these additions offer robust solutions for a wide array of applications. Similarly, the introduction of advanced surface treatments like Hard Anodise (Clear), LTBC-Surface Treatment, and Phosphating ensures that your components will benefit from superior durability, corrosion protection, and performance enhancement.
Whether you’re seeking materials for high-stress environments or surface treatments to extend the lifespan of your parts, our latest offerings have you covered. By combining the right materials with tailored surface treatments, you can significantly improve the efficiency, performance, and durability of your products across various industries.