BLOG » What Is Copper? Copper in Component Machining
What Is Copper? Copper in Component Machining
Copper is one of the most commonly used non-ferrous metals, rivaling aluminum in its versatility. This article delves into the properties of copper, its applications, the different types of copper alloys, key points for machining copper, and how to read copper alloy designations.
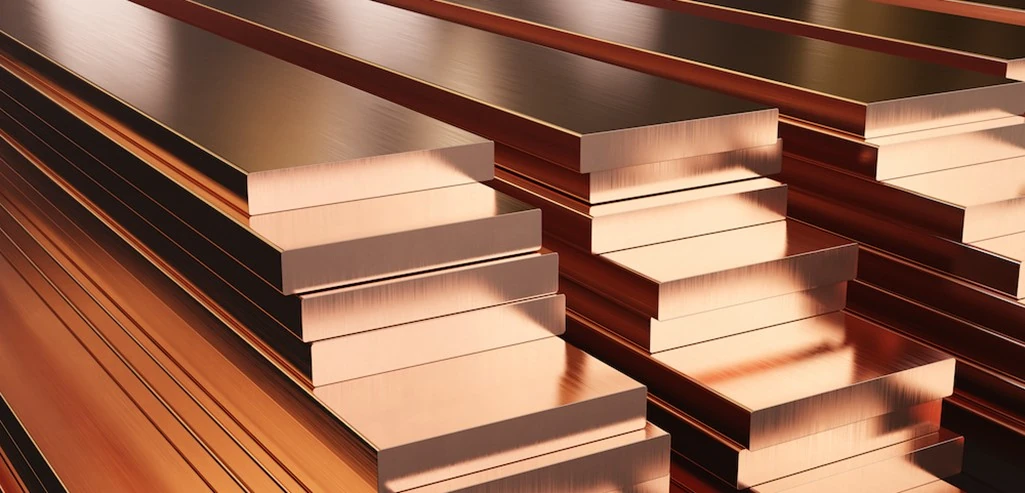
Key Properties of Copper
Copper (Cu) is a vital non-ferrous metal widely used in industrial applications, much like aluminium.
Copper boasts excellent thermal and electrical conductivity. As a relatively soft metal, copper is also highly malleable and easy to work with. It’s environmentally friendly due to its recyclability and has the advantage of not becoming brittle in low-temperature environments. The metal’s distinct, beautiful color makes it popular in decorative building materials, while its ability to form a protective oxide layer enhances its corrosion resistance. Additionally, copper’s antimicrobial properties make it ideal for high-touch surfaces and plumbing.
However, copper is denser and heavier than iron.
What Is Pure Copper?
Pure copper refers to copper alloys with a copper content of 99.90% or higher. Based on the oxygen content, pure copper is classified into three types: oxygen-free copper, tough-pitch copper, and deoxidized copper. Oxygen-free copper has minimal oxygen and is highly pure. Tough-pitch copper contains trace oxygen, enhancing its corrosion resistance and weatherability. Deoxidized copper, which includes small amounts of non-metallic deoxidizers like phosphorus, is less prone to hydrogen embrittlement.
Characteristics of Pure Copper
Pure copper stands out among copper alloys for its superior electrical and thermal conductivity. It is non-magnetic and does not attract magnets.
Mechanical Properties of Pure Copper:
- Specific Gravity: 8.89–8.94
- Tensile Strength: 355 N/mm²
- Hardness: HV 85+
- Young’s Modulus: 117 kN/mm²
- Conductivity: 100% IACS
- Thermal Expansion: 16.8 × 10⁻⁶/°C
- Thermal Conductivity: 398 W/(m·K)
- Melting Point: 1083°C
- Boiling Point: 2360°C
Advantages and Disadvantages of Pure Copper
Advantages:
- Soft and easy to machine
- Relatively resistant to acids and alkalis
- High electrical and thermal conductivity
Disadvantages:
- Heavy
- Requires plating to prevent corrosion
- Softness necessitates careful machining
Types of Copper Alloys
Copper’s high fusibility allows it to be alloyed with other metals. Here are some key copper alloys:
Brass (Yellow Copper)
Brass is an alloy of copper and zinc, known for its excellent ductility, hot forging properties, machinability, and light weight compared to pure copper. Brass has a beautiful metallic sheen similar to gold.
Bronze
Bronze is copper alloyed with tin. It gradually oxidizes in the atmosphere, forming a green patina known as verdigris. Bronze is harder than pure copper but has a lower melting point, making it one of the oldest metals used by humans. It is found in 10-yen coins and everyday items.
High-Copper Alloys
High-copper alloys contain over 96% copper, offering similar thermal and electrical conductivity as pure copper while providing increased strength and heat resistance. These alloys are used in precision instruments like computers and smartphones, as well as in automotive components. The properties of high-copper alloys vary depending on the added metals, such as beryllium copper, which has both electrical conductivity and spring properties.
Machining Tips for Copper Alloys
Copper and its alloys are soft metals, making them easy to cut, but they can also pose challenges due to their softness.
Tackiness and Burr Formation
Copper is soft and has high ductility, which can lead to burrs during machining as the material tends to stick when cut.
Soldering During Machining
Copper’s softness, combined with its low melting point, can cause cuttings to melt during machining, leading to soldering on the tool’s cutting edge. To dissipate the heat generated during machining, coolants are necessary. However, using water-based coolants may cause discoloration due to corrosion, so oil-based coolants are recommended.
Due to copper’s tackiness, reducing cutting resistance is key. Using sharp tools with a large rake angle and increasing cutting speed for high-speed machining are effective strategies.
Conclusion
Copper is a non-ferrous metal widely used alongside aluminum. It features high thermal and electrical conductivity and is easily recyclable. Copper alloys include pure copper, brass, white copper, bronze, and high-copper alloys. While copper is easy to machine, it requires careful handling due to burr formation and potential soldering during cutting. Copper alloy materials are designated with a “C” followed by a four-digit number and symbols.
At meviy, we offer copper as a material for machined round parts. We hope this article helps you consider EN CW614N equiv. as a potential material choice for your CNC turned components.