BLOG » Ein Leitfaden zu CNC-Bearbeitungstoleranzen
Ein Leitfaden zu CNC-Bearbeitungstoleranzen
In der CNC-Bearbeitung spielen Toleranzen eine entscheidende Rolle, um sicherzustellen, dass Bauteile den funktionalen Anforderungen und den Anforderungen an die Montage entsprechen. Eine Toleranz definiert die zulässige Abweichung von den Maßen und beeinflusst die Genauigkeit sowie die Leistung des Endprodukts. Das Verständnis von Toleranzen ist für Ingenieure, Konstrukteure und Hersteller unerlässlich, um die Produktion zu optimieren und gleichzeitig die Kosteneffizienz zu wahren.
Toleranzen geben die zulässige Abweichung von einer nominalen Dimension vor und stellen sicher, dass ein Bauteil innerhalb der erforderlichen mechanischen und funktionalen Grenzen passt. Diese Abweichungen werden in der Regel in Mikrometern (µm) oder Millimetern (mm) gemessen und hängen von Faktoren wie Materialeigenschaften, Bearbeitungsverfahren und Konstruktionsanforderungen ab. Diese Spezifikationen sind in technischen Zeichnungen von entscheidender Bedeutung, in denen Ingenieure die Maßtoleranzen mit einer standardisierten Notation angeben. Durch das Festlegen präziser Toleranzen können Hersteller ein Gleichgewicht zwischen Kosten, Materialeffizienz und Leistung finden und so sicherstellen, dass CNC-bearbeitete Bauteile den Industriestandards und funktionalen Anforderungen entsprechen.
Wie bereits erklärt, werden Toleranzen verwendet, um zu steuern, wie stark ein fertiges Bauteil von den nominalen Maßen abweichen kann, ohne die Funktionalität zu beeinträchtigen. Diese Toleranzen sind entscheidend, um die Austauschbarkeit, Passgenauigkeit, Funktion und Fertigbarkeit sicherzustellen.
Hier sind die wichtigsten Toleranzarten, die häufig beim Konstruieren von Bauteilen verwendet werden:
1. Maßtoleranzen
gilt für die Größe von Merkmalen wie Längen, Durchmessern, Dicken usw.
- Lineartoleranzen: z. B. 50 ± 0,1 mm
- Winkeltoleranzen: z. B. 90° ± 0,5°
- Werden häufig unter Verwendung der ISO 2768-1 für allgemeine Toleranzen definiert, wenn keine explizite Angabe erfolgt.
2. Geometrische Toleranzen
Definiert durch BS 8888 (britische Norm, die mit ISO 1101 übereinstimmt)
Diese Toleranzen regeln die Form, Ausrichtung und Position von Merkmalen über die bloße Größe hinaus.
Hauptarten:
- Formtoleranzen
- Ebenheit
- Planheit
- Rundheit
- Zylindrizität
- Ausrichtungstoleranzen
- Rechtwinkligkeit
- Parallelität
- Winkligkeit
- Lagertoleranzen
- Position
- Exzentrizität
- Symmetrie
- Läuftoleranzen
- Kreisrundlauf
- Gesamtläuftoleranz
Jede Toleranzart hat ein spezifisches Symbol, das im Merkmalsteuerrahmen auf der technischen Zeichnung verwendet wird.
3. Oberflächenbeschaffenheitstoleranzen
- Gibt die Rauheit oder Oberflächenbeschaffenheit eines Bauteils an.
- Wird mit Symbolen wie Ra (Durchschnittsrauhigkeit) angegeben.
- Reguliert durch EN ISO 1302.
4. Passungs- und Grenztoleranzen (Bohrungs/Wellen-System)
- Gibt an, wie eng oder locker zwei passgenaue Bauteile zusammenpassen.
- Reguliert durch EN ISO 286.
- Verwendet Toleranzklassen (IT01–IT16) sowie Buchstabencodes für Bohrungen (H, G usw.) und Wellen (h, g usw.)
- Beispiel: H7/g6 = gleitende Passung
Arten von Passungen:
- Lagerspielpassung
- Übergangspassung
- Presspassung
5. Positions- und Bezugstoleranzen
- Steuert, wo Merkmale in Bezug aufeinander oder auf einen Bezugspunkt positioniert werden müssen.
- Wird häufig zusammen mit GD&T verwendet.
Zusammenfassungstabelle
Typ | Merkmal | Beispiel / Norm |
---|---|---|
Dimensional | Größe (Länge, Durchmesser) | ISO 2768-1 |
Geometrisch (GD&T) | Form, Position | ISO 1101 |
Oberflächenbeschaffenheit | Oberflächenbehandlung, Rauheit | ISO 1302 |
Grenzen und Passungen | Passende Bauteile | ISO 286 |
Positionell | Relative Lage | GD&T Merkmalsteuerrahmen |
Wichtige Begriffe bei Maßtoleranzen
Ein Missverständnis von Toleranzbegriffen kann zu Konstruktionsfehlern führen. Um Genauigkeit zu gewährleisten, geben wir die folgenden Definitionen basierend auf internationalen Standards an:
Begriff | Definition |
Maßgeometrie | Die geometrische Form, die durch Längen- oder Winkelmessungen definiert wird. |
Nominalmaß | Die theoretische perfekte Dimension, wie sie in einer Zeichnung angegeben ist. |
Toleranzgrenzen | Die maximal und minimal zulässige Größe für ein Merkmal. |
Obere Grenze | Die größtmögliche zulässige Größe. |
Lower Limit | Die kleinstmögliche zulässige Größe. |
Toleranzwert | Die Differenz zwischen der oberen und unteren Grenze. |
Obere Abweichung | Die Abweichung vom Nominalmaß zur oberen Grenze. |
Untere Abweichung | Die Abweichung vom Nominalmaß zur unteren Grenze. |
Toleranzklasse | Eine Kombination von grundlegenden Toleranzen und Basisgrößenklassen. |
Warum das Verständnis von Toleranzen wichtig ist
Die Auswahl der richtigen Toleranz ist entscheidend, um Präzision, Fertigbarkeit und Kosten in Einklang zu bringen. Zu enge Toleranzen können die Komplexität der Bearbeitung und die Kosten erhöhen, während zu weite Toleranzen zu Montageproblemen führen können. Durch die Beachtung von Industriestandards und die korrekte Festlegung von Toleranzen können Ingenieure die Produktionseffizienz steigern und die Bauteilkompatibilität sicherstellen.
Allgemeine Toleranzen: Der Standard für Maßabweichungen
Wenn eine Dimension mit einer Toleranz von ±0,1 angegeben wird, achten die Hersteller besonders auf Abweichungen. Aber was passiert, wenn eine Dimension ohne Toleranz angegeben wird? Wie bestimmen wir den zulässigen Bereich der Abweichung?
Die Antwort liegt in den allgemeinen Toleranzen, die auch als Standardtoleranzen oder gewöhnliche zulässige Abweichungen in der Konstruktion und in der Fertigung bekannt sind. Dies sind vordefinierte Toleranzen, die angewendet werden, wenn keine expliziten Toleranzen angegeben werden, und helfen, technische Zeichnungen übersichtlich und frei von Unordnung zu halten.
Verständnis von allgemeinen Toleranzen
Wenn eine Dimension ohne Toleranz angegeben wird, geht die allgemeine Praxis davon aus, dass der Toleranzbereich sowohl auf der positiven als auch auf der negativen Seite gleich ist und um das Nominalmaß zentriert ist. Das bedeutet, dass ein Bauteil, egal ob es etwas größer oder kleiner produziert wird, solange es innerhalb des zulässigen Bereichs bleibt, als akzeptabel gilt.
Die spezifischen Werte der allgemeinen Toleranzen variieren je nach Fertigungsmethode. Im Folgenden konzentrieren wir uns auf die gängigen allgemeinen Toleranzen für Bearbeitungsprozesse, basierend auf den ISO 2768 Standards.
Tabelle 5-2 Allgemeine Toleranzen für Längenmaße ohne Fasen (ISO 2768 ~ Im Falle von Schnittverfahren)
Toleranzgrad | Klassifikation der Standardmaße | |||||||||
Erklärung | 0,5 bis ≤ 3 | 3 und ≤ 6 | 6 und ≤ 30 | 30 und ≤ 120 | 120 und < 400 | 400 und < 1000 | 1000 und < 2000 | 2000 und < 4000 | ||
Toleranz | ||||||||||
Feiner Grad | ±0.05 | ±0.05 | ±0.1 | ±0.15 | ±0.2 | ±0.3 | ±0.5 | – | ||
Mittlerer Grad | ±0.1 | ±0.1 | ±0.2 | ±0.3 | ±0.5 | ±0.8 | ±1.2 | ±2 | ||
Grober Grad | ±0.2 | ±0.3 | ±0.5 | ±0.8 | ±1.2 | ±2 | ±3 | ±4 | ||
Sehr grob | – | ±0.5 | ±1 | ±1.5 | ±2.5 | ±4 | ±6 | ±8 |
Tabelle 5-3 Allgemeine Toleranz der Fasenlänge (ISO 2768 ~ Für Schnittverfahren)
Toleranzklasse | Klassifikation der Standardmaße | ||
---|---|---|---|
Erklärung | ≥ 0,5 | ≥ 3 | ≥ 6 |
≤ 3 | ≤ 6 | ||
Toleranz | |||
Feiner Grad | ±0.2 | ±0.5 | ±1 |
Mittlerer Grad | |||
Grober Grad | ±0.4 | ±1 | ±2 |
Tabelle 5-4 Allgemeine Toleranzen für Winkelmaße (ISO 2768 – für Schnittverfahren)
Toleranzklasse | Länge der kürzeren Seite des betreffenden Winkels | ||||
Erklärung | ≤ 10 | > 10 – ≤ 50 | > 50 – ≤ 120 | > 120 – ≤ 400 | > 400 |
Toleranz | (Angaben in Grad und Minuten) | ||||
Feiner Grad | ±1° | ±30′ | ±20′ | ±10′ | ±5′ |
Mittlerer Grad | |||||
Grober Grad | ±1°30′ | ±1° | ±30′ | ±15′ | ±10′ |
Sehr grob | ±3° | ±2° | ±1° | ±30′ | ±20′ |
Bearbeitungstoleranzgrade
Die allgemeinen Toleranzen für die Bearbeitung werden in vier Grade unterteilt:
- Feiner Grad (f) – Hohe Präzision
- Mittlerer Grad (m) – Standardpräzision
- Grobe Klasse (c) – Geringere Präzision
- Sehr grober Grad (v) – Grobe Bearbeitung
Wie man Maßtoleranzen korrekt angibt
In Fällen, in denen allgemeine Toleranzen nicht ausreichen, müssen engere Toleranzen angegeben werden, um funktionale und montagetechnische Anforderungen zu erfüllen. Unnötig strenge Toleranzen erhöhen jedoch die Bearbeitungskosten exponentiell, da nur wenige Hersteller in der Lage sind, extreme Präzision zu erreichen.
1. Wie man Maßtoleranzen angibt
Für Maßtoleranzen wird die zulässige Abweichung direkt neben dem nominalen Maß angegeben. Wenn die oberen und unteren Abweichungen nicht symmetrisch sind, werden sie übereinander geschrieben, jeweils über und unter dem nominalen Wert.

Die Maßtoleranz muss nicht unbedingt gleichmäßig um das nominale Maß verteilt sein. Es ist möglich, die Toleranz entweder auf die positive oder die negative Seite zu verschieben (dies wird in Konstruktionskontexten oft als unilaterale Toleranz bezeichnet).
Auf diese Weise drücken Konstrukteure ihre Konstruktionsabsicht in Zeichnungen aus, indem sie den Zielbereich auf den mittleren, oberen oder unteren Bereich relativ zum nominalen Maß ausrichten. Es ist jedoch wichtig zu beachten, dass Fertiger in der Regel das Mittel der zulässigen Toleranzspanne während der Fertigung anstreben.
2. Angabe von Winkeltoleranzen
Die Notation für Winkeltoleranzen folgt demselben Format wie die Maßtoleranzen. Allerdings erfordern Winkeldimensionen Einheitenzeichen, und das sexagesimale (60er) System wird in der Regel verwendet, dargestellt in Grad (°), Minuten (′) und Sekunden (″).
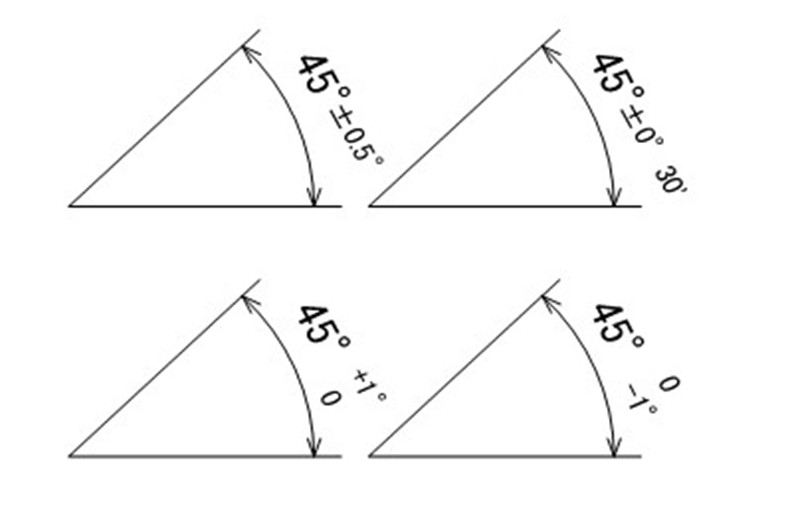
Wie sollten Minuten (′) und Sekunden (″) interpretiert werden?
Dies funktioniert ähnlich wie bei einer Uhr: Wenn 60 Minuten vergehen, bilden sie 1 Grad und wechseln zur nächsten Einheit. Diese Zählweise ist als das sexagesimale System bekannt.
Im Gegensatz dazu folgt die reguläre Zahlennotation dem Dezimalsystem, bei dem 9 auf 10 ansteigt. Die folgende Tabelle zeigt eine Umrechnung zwischen Winkeln in Minuten (′) im 60er-System und Dezimalgraden.
Winkelumrechnungstabelle (Minuten zu Dezimalgraden)
Minuten (′) | Dezimalgrade | Minuten (′) | Dezimalgrade | Minuten (′) | Dezimalgrade | Minute (′) | Dezimalgrade |
1′ | 0.0167° | 16′ | 0.2667° | 31′ | 0.5167° | 46′ | 0.7667° |
2′ | 0.0333° | 17′ | 0.2833° | 32′ | 0.5333° | 47′ | 0.7833° |
3′ | 0.0500° | 18′ | 0.3000° | 33′ | 0.5500° | 48′ | 0.8000° |
4′ | 0.0667° | 19′ | 0.3167° | 34′ | 0.5667° | 49′ | 0.8167° |
5′ | 0.0833° | 20′ | 0.3333° | 35′ | 0.5833° | 50′ | 0.8333° |
6′ | 0.1000° | 21′ | 0.3500° | 36′ | 0.6000° | 51′ | 0.8500° |
7′ | 0.1167° | 22′ | 0.3667° | 37′ | 0.6167° | 52′ | 0.8667° |
8′ | 0.1333° | 23′ | 0.3833° | 38′ | 0.6333° | 53′ | 0.8833° |
9′ | 0.1500° | 24′ | 0.4000° | 39′ | 0.6500° | 54′ | 0.9000° |
10′ | 0.1667° | 25′ | 0.4167° | 40′ | 0.6667° | 55′ | 0.9167° |
11′ | 0.1833° | 26′ | 0.4333° | 41′ | 0.6833° | 56′ | 0.9333° |
12′ | 0.2000° | 27′ | 0.4500° | 42′ | 0.7000° | 57′ | 0.9500° |
13′ | 0.2167° | 28′ | 0.4667° | 43′ | 0.7167° | 58′ | 0.9667° |
14′ | 0.2333° | 29′ | 0.4833° | 44′ | 0.7333° | 59′ | 0.9833° |
15′ | 0.2500° | 30′ | 0.5000° | 45′ | 0.7500° | 60′ | 1.0000° |
Bei der Angabe von Winkeltoleranzen liegt die Wahl zwischen Dezimalnotation und sexagesimaler Notation in der Regel im Ermessen des Konstrukteurs.
Ansammlung von Toleranzen
Um zu untersuchen, wie sich Dimensionierungsmethoden auf die Abweichung auswirken, wurden serielle und parallele Maßangaben unter Verwendung allgemeiner Toleranzen (mittlerer Grad) veranschaulicht (siehe Abbildungen 5-3 und 5-4).
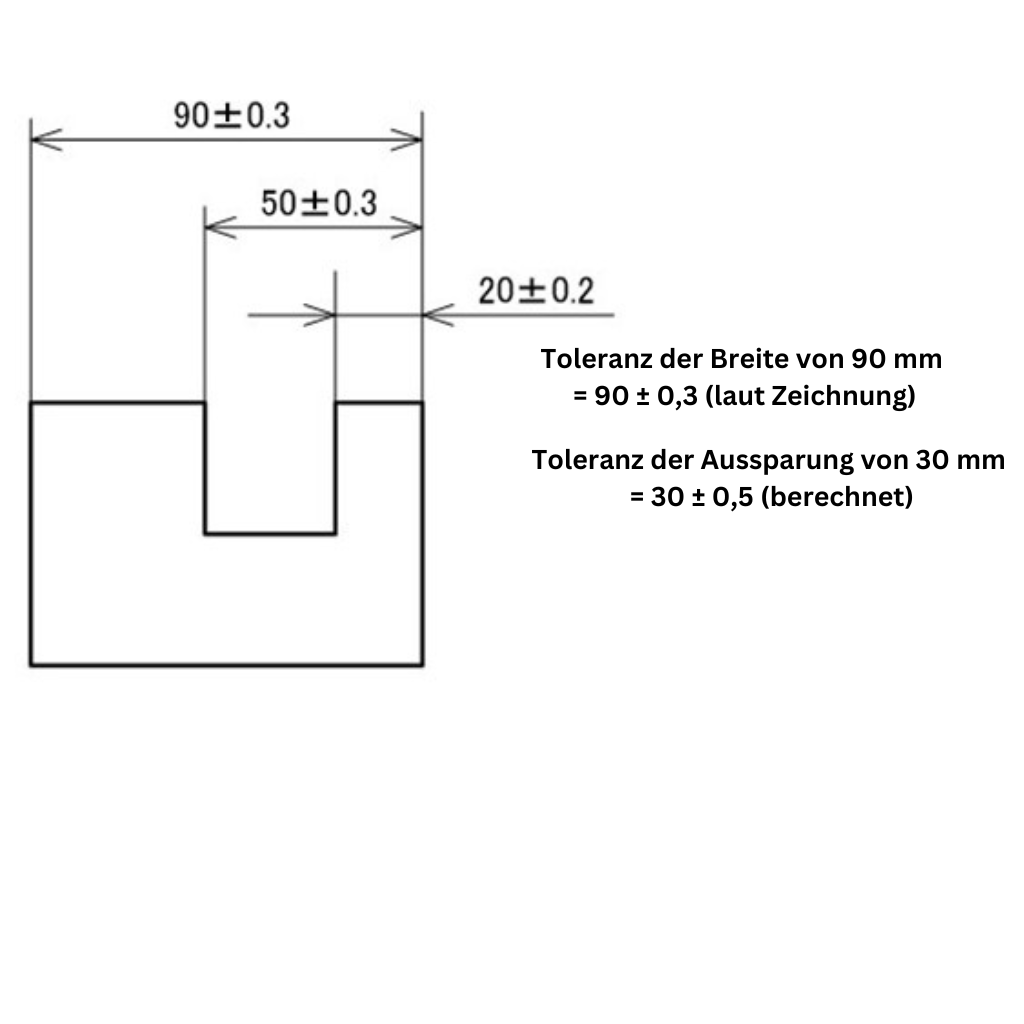
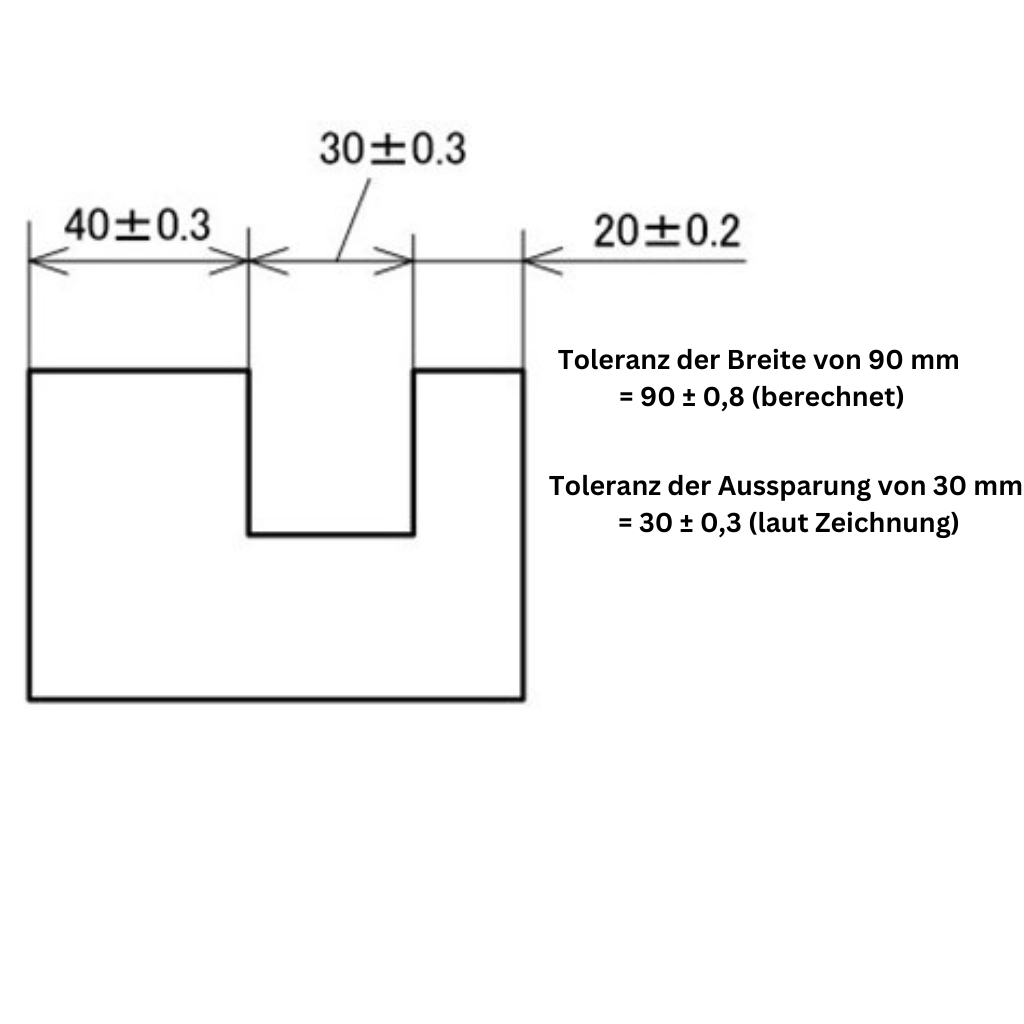
Lassen Sie uns zwei wichtige Maße untersuchen – die Gesamtbreite (90 mm) und die Nutbreite (30 mm) –, um die Abweichungen der Maße nach der Bearbeitung zu bewerten.
Gesamtbreite
- Serielle Maßangabe: 90 ± 0,8 mm
- Kumulative Toleranzberechnung: [±0,3] + [±0,3] + [±0,2] = ±0,8
- Parallele Maßangabe: 90 ± 0,3 mm (direkt aus der Maßnotation ablesbar)
Daraus geht hervor, dass die Maßabweichung bei der seriellen Maßangabe um 0,5 mm größer ist als bei der parallelen Maßangabe.
Nutbreite
- Serielle Maßangabe: 30 ± 0,3 mm (direkt aus der Maßnotation ablesbar)
- Parallele Maßangabe: 30 ± 0,5 mm
- Kumulative Toleranzberechnung: [±0,3] + [±0,2] = ±0,5
Hinweis: Während die Basisdimension durch Subtraktion bestimmt wird, sind die Toleranzen kumulativ und müssen addiert werden. Daher ist die Abweichung der Nutbreite bei der parallelen Maßangabe um 0,2 mm größer als bei der seriellen Maßangabe.
Dieses Beispiel zeigt, dass beide Maßangabemethoden je nach spezifischem Bauteilmerkmal Vor- und Nachteile haben.
Es gilt jedoch eine allgemeine Regel:
- Kritische funktionale Maße sollten immer direkt angegeben werden, um Abweichungen zu minimieren.
- Vermeiden Sie es, für wichtige Maße auf additive oder subtraktive Berechnungen zu setzen.
Mit anderen Worten, wenn die genauen Größen der Auswölbung und der Nut wichtiger sind als die Gesamtlänge von 90 mm, ist die Maßangabemethode in Abbildung 5-3 vorzuziehen. Umgekehrt, wenn die Gesamtlänge von 90 mm oder die Position der Nut vom rechten Rand wichtiger ist als die Nutbreite von 30 mm, ist die Maßangabemethode in Abbildung 5-4 besser geeignet.
Verstehen der Passungsarten: Essentielles Wissen für die Präzisionsbearbeitung
Bei der Montage von Bauteilen ist eine präzise Ausrichtung oder kontrollierte Bewegung von entscheidender Bedeutung. Hier kommen die Passungen ins Spiel.
Eine Passung bezieht sich auf die dimensionalen Beziehungen zwischen einem Loch und einer Welle vor der Montage. Es gibt drei Hauptarten, die jeweils für unterschiedliche Anwendungen geeignet sind:
- Lagerspielpassung: Wird verwendet, um stationäre Bauteile zu positionieren oder Bewegung in drehenden/gleitenden Bauteilen zu ermöglichen.
- Presspassung: Wird verwendet, wenn Bauteile presssitzend eingebaut und dauerhaft gesichert werden müssen.
- Übergangspassung: Eine variable Passung, die je nach Toleranzabweichungen entweder als Lagerspiel- oder Presspassung fungieren kann. Aufgrund dieser Unvorhersehbarkeit bevorzugen Konstrukteure Übergangspassungen nur selten, es sei denn, es ist absolut notwendig.
Wie man Passungen in technischen Zeichnungen angibt
Passungsklassifikationen verwenden ein standardisiertes Notationssystem, das einen Groß- oder Kleinbuchstaben mit einer numerischen Stufe kombiniert, um Toleranzklassen zu definieren. Diese Notation ist international anerkannt.
- Für Löcher (interne Merkmale wie Nuten) wird ein Großbuchstabe verwendet → Beispiel: φ10H7
- Für Wellen (externe Merkmale wie Auswölbungen) wird ein Kleinbuchstabe verwendet → Beispiel: φ10h7
Das alphabetische Symbol stellt die Position der Toleranzzone relativ zum nominalen Maß dar (ob diese eher auf der positiven oder negativen Seite liegt). Die untenstehende Abbildung zeigt eine visuelle Darstellung dieses Konzepts.
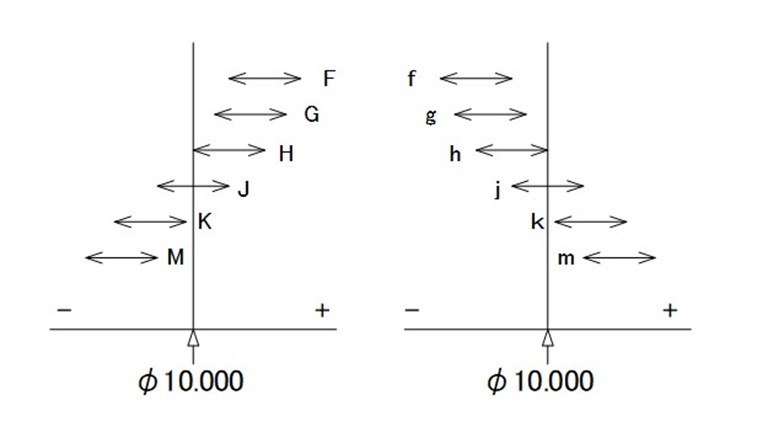
Fazit
In dieser Sitzung haben wir allgemeine Toleranzen, Maßtoleranzen und Passungstoleranzklassen-Symbole behandelt. Diese Symbole folgen international anerkannten Standards, wodurch sie weltweit in der Fertigung anwendbar sind. Als Konstrukteur ist es wichtig, die folgenden Punkte zu beachten:
- Verstehen Sie die Existenz und Werte der allgemeinen Toleranzen, bevor Sie eine spezifische Toleranz festlegen.
- Toleranzen, die sich auf die Größe beziehen, werden als „Maßtoleranzen“ bezeichnet.
- Zu strenge Toleranzen erhöhen die Bearbeitungsschwierigkeiten und führen zu höheren Kosten.
- Die Anordnung der Maße kann zwischen kritischen und nicht-kritischen Merkmalen unterscheiden.
- Für hochpräzise Passungen sollten die Toleranzklassen unter Verwendung der Standardnotation ausgedrückt werden.