BLOG » Einführung in den Veredelungsprozess: Alles, was Sie wissen müssen
Einführung in den Veredelungsprozess: Alles, was Sie wissen müssen
Veredelung ist eine Oberflächenbehandlungstechnik, bei der die Oberfläche eines Materials mit einer dünnen Schicht eines anderen Metalls überzogen wird. Diese Technik ist in verschiedenen Industrien von entscheidender Bedeutung und bietet je nach Art der Veredelung unterschiedliche Vorteile. Von der Verbesserung der Optik über die Steigerung der Leistung und Haltbarkeit spielt die Veredelung eine wichtige Rolle in der Fertigung und Produktentwicklung. In diesem Artikel werfen wir einen genaueren Blick auf den Veredelungsprozess, seine Arten und die beteiligten Verfahren.
Was ist Veredelung? Anwendung und Vorteile
Veredelung ist eine Oberflächenbehandlungsmethode, bei der eine dünne Metallschicht auf die Oberfläche eines Basismaterials wie Metall oder Kunststoff aufgetragen wird. Es gibt verschiedene Veredelungsverfahren, darunter Trockenveredelung, Nassveredelung und Galvanisieren. Im Gegensatz zu anderen Oberflächenbehandlungen wie Lackieren, thermischem Spritzen oder Härten zeichnet sich die Veredelung durch ihre Fähigkeit aus, eine gleichmäßige und dünne Schicht zu bilden. Sie ist besonders geeignet für Bauteile mit komplexen Formen und findet daher in vielen Industrien Anwendung.
Die Anwendung von Veredelungen lassen sich grob in drei Hauptziele unterteilen:
- Steigerung der ästhetischen Anziehungskraft
Veredelung wird häufig durchgeführt, um das Erscheinungsbild von Produkten zu verbessern, beispielsweise durch die Schaffung einer glänzenden Oberfläche oder das Hinzufügen eines luxuriösen metallischen Finishs. Vergoldung ist ein typisches Beispiel für dekorative Veredelung. - Verbesserung der Korrosionsbeständigkeit
Materialien wie Eisen, die häufig in industriellen Produkten verwendet werden, neigen zur Rostbildung. Die Veredelung mit korrosionsbeständigen Metallen wie Zink schützt die Oberfläche vor Oxidation und Rost. - Verbesserung der funktionalen Eigenschaften
Veredelung kann auch zusätzliche funktionale Vorteile bieten, die über Ästhetik und Korrosionsbeständigkeit hinausgehen. Zum Beispiel kann die Lötfähigkeit durch Nickelveredelung oder durch Veredelung mit Kupfer-Zinn-Legierungen verbessert werden. Weitere Beispiele umfassen die Verbesserung der Gleiteigenschaften oder die Steigerung der elektrischen Leitfähigkeit.
Hauptmerkmale der Veredelung
Die Veredelung bietet mehrere Vorteile, die sie zu einer bevorzugten Oberflächenbehandlungsmethode in verschiedenen Anwendungen machen:
- Gleichmäßige Beschichtungsdicke: Veredelung sorgt für eine gleichmäßige und dünne Metallschicht auf der Oberfläche. Die Dicke der Beschichtung kann jedoch je nach Form des Bauteils variieren.
- Ausgezeichnete Haftung: Veredelte Beschichtungen haften stark am Basismaterial und gewährleisten so langfristige Stabilität und Haltbarkeit.
- Vielseitige Funktionen: Je nach Wahl des Metalls kann Veredelung Eigenschaften wie Korrosionsbeständigkeit, elektrische Leitfähigkeit, Abriebfestigkeit und Lötfähigkeit bieten.
- Kosten-Nutzen-Verhältnis: Veredelung ermöglicht es Herstellern, die gewünschten Eigenschaften zu erzielen, ohne teure Metalle für das gesamte Bauteil verwenden zu müssen.
- Umweltvorteile: Moderne Veredelungstechniken wie hexavalent-chromfreie Veredelung und Dünnschichtveredelung sind darauf ausgelegt, die Umweltauswirkungen zu reduzieren.
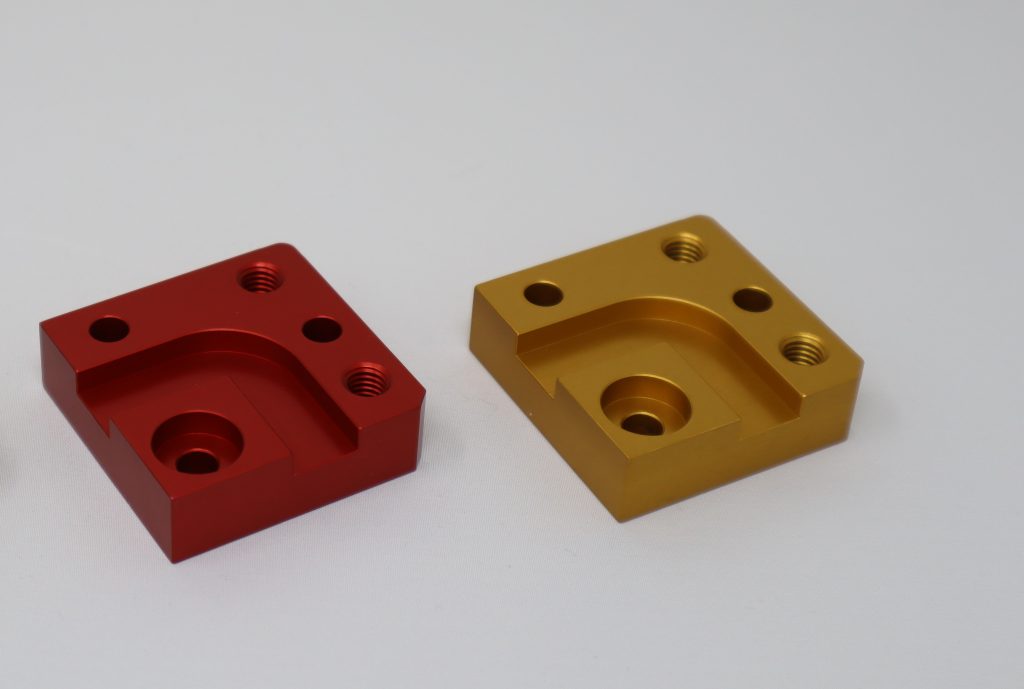
Arten der Veredelung
Veredelungsverfahren können grob in zwei Kategorien unterteilt werden: Trockenveredelung und Nassveredelung.
Trockenveredelung (Vakuumbeschichtung)
Trockenveredelung, auch bekannt als Vakuumabscheidung, umfasst die Ablagerung eines Metallfilms auf der Oberfläche eines Bauteils in einer Vakuumumgebung. Beispiele hierfür sind Physical Vapor Deposition (PVD) und Chemical Vapor Deposition (CVD).
Trockenveredelung wird häufig in der Halbleiterfertigung verwendet und kann nicht nur Metalle, sondern auch Verbindungsfilme abdecken. Sie erfordert jedoch eine Hochtemperaturverarbeitung und ist teurer als Nassveredelung.
Nassveredelung
Bei dieser Methode wird das Werkstück in eine Elektrolytlösung getaucht, und der Großteil der allgemein als „Veredelung“ bezeichneten Verfahren fällt unter die Nassveredelung. Nassveredelung lässt sich weiter in die folgenden drei Arten unterteilen:
Galvanische Veredelung (Elektrolytische Veredelung)
Die galvanische Veredelung erfolgt durch Eintauchen des Bauteils in eine Lösung mit Metallionen und einem Reduktionsmittel, um die Metallschicht ohne den Einsatz von Elektrizität abzusetzen. Dieses Verfahren eignet sich besonders für nichtleitende Materialien wie Kunststoffe.
Elektrolytische Nickelveredelung
Bekannt für ihre gleichmäßige Dicke, Abriebfestigkeit und Korrosionsbeständigkeit, wird diese Methode häufig in industriellen Anwendungen eingesetzt.
Elektroveredelung (Elektrolyse)
Elektroveredelung ist eine der häufigsten und vielseitigsten Veredelungsmethoden, die verwendet wird, um die dekorative Anziehungskraft, Korrosionsbeständigkeit, Abriebfestigkeit und elektrische Leitfähigkeit zu verbessern. Der Prozess umfasst das Eintauchen sowohl des zu veredelnden Metalls als auch des Beschichtungsmetalls in eine Lösung, die Metallionen enthält. Ein Gleichstrom wird angelegt, wobei das zu veredelnde Metall an den positiven Pol (Anode) und das Beschichtungsmetall an den negativen Pol (Kathode) angeschlossen wird. Dies löst eine Reduktionsreaktion in der Lösung aus, bei der das Beschichtungsmetall auf die Oberfläche des veredelten Metalls abgeschieden wird.
Die Dicke der abgeschiedenen Metallschicht hängt von der Stromdichte ab, was bedeutet, dass komplexe Formen zu ungleichmäßiger Veredelung führen können – hervorstehende Bereiche erhalten tendenziell dickere Beschichtungen, während vertiefte Bereiche dünnere Schichten erhalten. Da die Dicke der Elektroveredelung durch Anpassung von Stromstärke und Dauer kontrolliert werden kann, ist es wichtig, die optimale Schichtdicke für jede Anwendung festzulegen.
Verschiedene Arten der Elektroveredelung:
- Vergoldung
Gold ist ein hochglänzendes und chemisch stabiles Metall, aber aufgrund seiner hohen Kosten ist massives Gold für viele Anwendungen unpraktisch. Stattdessen wird die Vergoldung verwendet, um die dekorative Anziehungskraft von Produkten zu erhöhen und gleichzeitig die Korrosionsbeständigkeit und elektrische Leitfähigkeit zu verbessern.
- Versilberung
Wie Gold ist Silber für seine dekorativen Eigenschaften bekannt. Allerdings neigt Silber zur Oxidation, was zu Verfärbungen führen kann. Um dies zu verhindern, werden nach der Versilberung zusätzliche Behandlungen angewendet. Aufgrund seiner hohen elektrischen Leitfähigkeit wird Versilberung häufig in der Oberflächenbehandlung von Präzisionsgerätesteckverbindern verwendet.
- Verzinkung
Verzinkung ist eine der am weitesten verbreiteten Methoden zum Korrosionsschutz. Wenn sie auf Eisenkomponenten angewendet wird, verhindert die Verzinkung Rost durch einen opferanodischen Schutzmechanismus, bei dem die Zinkschicht anstelle des Eisens korrodiert. Um den Schutz weiter zu verbessern, werden verzinkte Oberflächen oft mit zusätzlichen Beschichtungen wie Klarchromat oder dreivalentem Chromat behandelt.
- Verchromung
Verchromung wird hauptsächlich verwendet, um metallische Oberflächen ein hochglänzendes Finish zu verleihen. Ihre Anwendungen gehen jedoch über die Ästhetik hinaus – dank ihrer ausgezeichneten Abrieb- und Korrosionsbeständigkeit wird industrielle Verchromung häufig auf Maschinenteilen und Werkzeugen angewendet.
- Kunststoffveredelung
Kunststoffveredelung ist eine Oberflächenbehandlungstechnik, die Kunststoffen ein metallisches Aussehen und Eigenschaften verleiht. Durch die Veredelung von Kunststoffen können Hersteller ein Premium-Aussehen erzielen und gleichzeitig von Gewichtseinsparungen, Designvielfalt, Fleckenbeständigkeit, Stoßfestigkeit und Kratzfestigkeit profitieren. Kunststoffveredelung nimmt einen erheblichen Anteil an dekorativen Veredelungsanwendungen ein.
Zusätzlich zu den oben genannten gibt es in der Elektroveredelung auch spezialisierte Typen wie Rhodiumveredelung, Palladiumveredelung und Platinveredelung, die jeweils auf spezifische Leistungs- und ästhetische Anforderungen zugeschnitten sind.
Zusätzliche Veredelungsmethoden
Neben der Elektroveredelung und der galvanischen Veredelung gibt es auch andere Verfahren:
- Brünieren: Brünieren wird verwendet, um einen dünnen schwarzen Film auf Metalloberflächen zu erzeugen, der sich ideal für Bauteile mit strengen Maßtoleranzen eignet. Diese Methode bietet einen gewissen Korrosionsschutz und wird häufig in der Maschinenbau- und Automobilindustrie verwendet.
- Eloxieren: Eloxieren ist eine Oberflächenbehandlung für Aluminium, bei der eine Oxidschicht auf der Oberfläche des Metalls gebildet wird. Diese Schicht erhöht die Härte und Korrosionsbeständigkeit des Materials und wird häufig in der Luft- und Raumfahrtindustrie, der Architektur und bei technischen Geräten verwendet.
- Heißverzinken: Bei diesem Verfahren werden Bauteile in geschmolzenes Zink getaucht, um eine schützende Zinkschicht zu bilden. Diese Methode wird häufig für Drahtprodukte und Baustellenmaterialien verwendet, um sie vor Rost und Korrosion zu schützen.
Fazit
Veredelung ist eine vielseitige Oberflächenbehandlungsmethode, die das Erscheinungsbild, die Haltbarkeit und die Funktionalität von Metall- und Kunststoffkomponenten verbessert. Vom dekorativen Vergolden bis hin zur funktionalen chemischen Vernickelung gibt es zahlreiche Verfahren, die auf spezifische Zwecke abgestimmt sind.
Bei meviy bieten wir sofortige Angebote und Bearbeitung für Veredelungsbehandlungen an. Indem Sie einfach Ihre 3D-CAD-Daten bei meviy hochladen, können Sie schnell maßgeschneiderte Bauteile arrangieren, selbst für Artikel, die nicht im umfassenden Webkatalog von MISUMI aufgeführt sind.