BLOG » What is Aluminium? Material Overview and Design Considerations
What is Aluminium? Material Overview and Design Considerations
Aluminium (Al) stands as one of the most common materials among non-ferrous metals, boasting numerous unique features absent in iron-based alloys, rendering it versatile across various applications. To devise effective product designs, a deep understanding of material characteristics is crucial, guiding the selection of suitable alloys, processing methods, and heat treatments. Today, we delve into the properties and types of aluminium.
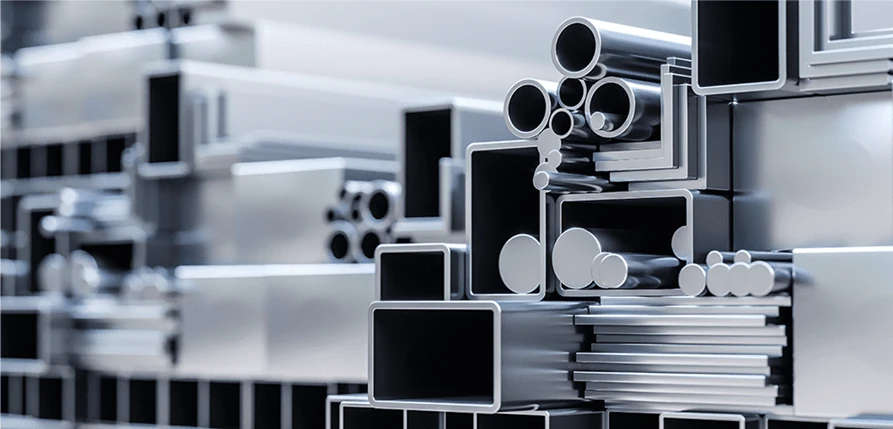
Key Advantages of Aluminium
Lightweight
With a specific gravity of approximately 2.7, aluminium weighs roughly one-third of steel. Leveraging its lightweight nature, aluminium finds utility in transportation vehicles, architectural materials, and mobile electronics, among other diverse fields.
Strenght
Aluminium alloys, formed by adding other metals to pure aluminium, enhance tensile strength. Notably, alloys fortified with zinc and magnesium additives followed by heat treatment, exhibit exceptional strength. The renowned A7075 (ultra-duralumin) is widely employed in aircraft components.
Corrosion Reisistance
Aluminium readily reacts with oxygen, forming a dense oxide film on its surface. This oxide film acts as a protective barrier, shielding against corrosion. Capitalizing on its high corrosion resistance, aluminium finds applications in marine development, shipbuilding, and architecture. Reports even attest to its problem-free use for up to 30 years in seaside environments.
Ease of Processing
Aluminium lends itself to various processing methods. Its excellent ductility makes it suitable for plastic forming, while its low melting point and good fluidity render it conducive to casting. It’s also easily machined and weldable. The versatility of aluminium processing enables fabrication into a myriad of shapes, from thin sheets (aluminium foil) to intricate forms.
Thermal Conductivity
Aluminium exhibits thermal conductivity approximately three times that of iron. This property makes it conducive to heat transfer, finding application in automotive radiators, various heat exchangers, and electronic heat sinks.
Electrical Conductivity
Compared to copper of the same weight, aluminium conducts double the electrical current. Given its lightweight and cost-efficient transmission line materials, replacing copper wires with aluminium wires can widen tower spacing, reducing costs.
Resiliance to Low Temperatures
Even at extremely low temperatures, such as liquid nitrogen (-196°C) or liquid oxygen (-183°C), aluminium maintains its strength or even becomes stronger. Consequently, it’s utilized in low-temperature plants, LNG (liquefied natural gas) tanks, space exploration, and biotechnology.
Design Considerations for Aluminium Components
Strength Considerations
When designing mechanical parts with aluminium, it’s crucial to acknowledge its lower strength compared to steel. Designers must meticulously evaluate load-bearing requirements and structural integrity, considering the specific forces the part will encounter during its lifecycle. To compensate for aluminium’s lower strength, reinforcement strategies become pivotal. Incorporating thicker sections, ribs, or gussets in critical areas can effectively enhance strength where necessary, ensuring the part can withstand anticipated loads without compromising safety or performance.
Thermal Expansion Management
Aluminium’s lower thermal conductivity compared to steel necessitates careful management of thermal expansion issues, especially in applications subjected to high temperatures. Designers must address the potential for thermal stress by incorporating allowances for expansion or employing thermal breaks to mitigate adverse effects. By accounting for thermal expansion in the design phase, such as incorporating gaps or slots, designers can prevent deformation or structural failures caused by excessive thermal stress, ensuring the part’s dimensional stability and longevity.
Corrosion Resistance Strategies
Given aluminium’s susceptibility to corrosion, particularly in harsh environments, implementing effective corrosion resistance strategies is paramount. Designers should select appropriate surface treatments like anodising or applying protective coatings to create a barrier against corrosive agents. Additionally, designing parts with features that minimize moisture retention, such as smooth surfaces and rounded edges, can further reduce the risk of corrosion. By prioritizing corrosion resistance in the design phase, designers can prolong the part’s lifespan and maintain its structural integrity, even in challenging operating conditions.
Challanges with Welding
The melting point of the oxide film formed on the surface of aluminium is approximately 2000°C, necessitating the removal of this oxide film before welding. Moreover, aluminium’s high thermal conductivity and low melting point mean that heat during welding quickly transfers to the base material, increasing the risk of material dropout. To prevent this, the welding torch speed must be gradually adjusted. Given these challenges, outsourcing aluminium welding to experienced professionals is advisable.
Joining Methods and Compatibility
When joining aluminium components, designers must consider compatibility between materials and the selected joining method to ensure optimal strength, durability, and resistance to corrosion. Welding and adhesive bonding are commonly used techniques for joining aluminium parts, offering excellent performance when executed correctly. However, it’s crucial to select compatible materials and appropriate joining processes to avoid galvanic corrosion and ensure the longevity of the assembly. By carefully evaluating joining options and considering material compatibility, designers can create robust and reliable assemblies that meet performance requirements while minimizing the risk of corrosion-related issues.
Optimization for Machinability and Waste Reduction
Optimizing part geometry for efficient machining and minimizing waste during fabrication is essential to maximize cost-effectiveness and sustainability. Designers should consider factors such as tool access, material removal rates, and surface finish requirements when designing aluminium parts for machining. By designing parts with features that facilitate efficient machining, such as uniform wall thicknesses and avoiding intricate geometries, designers can streamline the manufacturing process, reduce production costs, and minimize material waste, contributing to overall sustainability goals.
Wrought Alloys:
A1050: A representative pure aluminum alloy known for its low strength but excellent workability and corrosion resistance, often used in decorative items and power transmission lines.
EN AW−2017 equiv.: Known as duralumin, EN AW−2017 equiv. (A2017) offers high strength despite lower corrosion resistance, making it suitable for aircraft, automobiles, and mechanical components.
EN AW−5052 equiv.: A widely circulated aluminum alloy prized for its corrosion resistance, workability, and weldability, commonly used in frame materials and sheet metal parts.
EN AW-6061 equiv. (A6061): A6061 is an aluminum alloy known for its excellent corrosion resistance, further enhanced through T6 heat treatment.
EN AW-6063 equiv (A6063): Boasting superior corrosion resistance and surface processability, EN AW-6063 equiv is the most widely used aluminum alloy in extruded products, used in aluminum sashes and electrical materials.
EN AW−7075 equiv. (A7075): Known as ultra-duralumin, EN AW−7075 equiv. (A7075) offers the highest strength among aluminum alloys. Developed by Japan before WWII, it was used in the Zero fighter and remains widely utilized in aircraft materials.
Casting Alloys:
AC2B: Exhibiting excellent castability, AC2B is commonly used as a general aluminum casting alloy in engine cylinder heads and valve bodies.
AC4C: AC4C offers corrosion resistance, mechanical properties, and castability, making it suitable for mission cases and compressor casings.
ACD10: A suitable die-casting material, ACD10 boasts excellent castability, machinability, and mechanical properties, widely used in engine cylinder blocks.
Conclusion
Designing mechanical parts made of aluminium requires careful consideration of various factors to ensure optimal performance and functionality. By adhering to the design considerations outlined above, engineers and designers can leverage the unique properties of aluminium to create lightweight, durable, and cost-effective components for a wide range of applications. Additionally, it’s important to note that aluminium is one of the most widely used materials in mechanical engineering due to its excellent strength-to-weight ratio, corrosion resistance, and versatility. With its ability to be easily machined, formed, and joined, aluminium offers unparalleled design flexibility, making it a preferred choice for numerous industries, including automotive, aerospace, and consumer electronics. By understanding and implementing the key design considerations for aluminium parts, engineers can unlock the full potential of this remarkable material and achieve superior results in their designs.