BLOG » What is Moulding Process? An Overview
What is Moulding Process? An Overview
In the realm of manufacturing, creating products involves transforming various materials through diverse techniques. Among these methods, moulding processes—such as forging, casting, pressing, and resin moulding—play a pivotal role. This article analyzes the fundamentals of these moulding processes and techniques, offering a clear understanding of their applications and benefits.
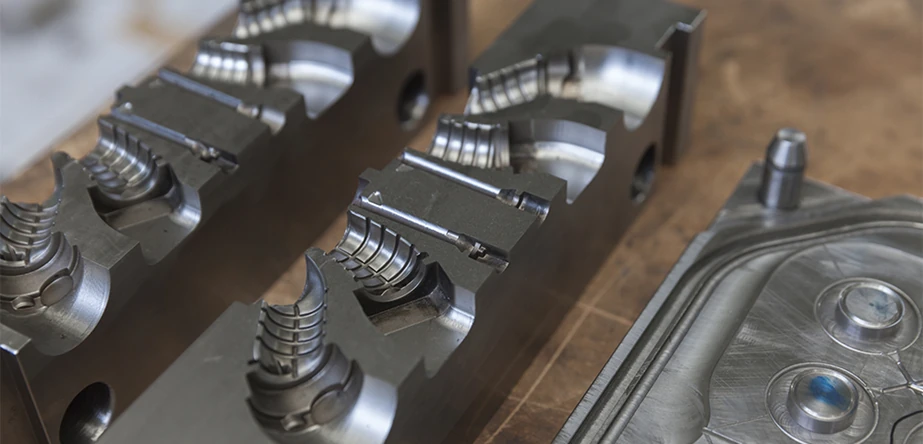
What is Moulding Process?
Moulding is a manufacturing process that uses a mold, typically made of metal or sand, to shape materials like metal or resin into desired forms. Various moulding techniques exist, including compressing materials within a mold, pouring heated and liquefied materials into molds, and more. The choice of method depends on the material properties and the intended product shape.
Key Features of Moulding
The defining characteristic of moulding is the use of molds to shape materials. Products created through moulding are typically designed to be easily separated from the mold. However, shapes with side holes or indentations can be challenging to produce without special considerations. Creating hollow shapes within the mold also requires specific techniques to ensure proper material filling and structural integrity.
Advantages and Disadvantages of Moulding
Every manufacturing method has its pros and cons, and moulding process is no exception. Here are some key points:
Advanatages
- Suitable for Mass Production: Moulding is ideal for producing large quantities of identical items, maintaining consistent quality across batches.
- High Precision for Complex Shapes: Moulding excels in creating intricate curves and designs, making it perfect for products like fan blades or car bodies.
Disadvantages
- High Initial Cost and Time: Creating molds, especially metal ones, requires significant time and financial investment, making it less suitable for small-scale production.
- Limited Flexibility Post-Production: Once a mold is made, altering its design is challenging, which can be a drawback if design changes are needed after production starts.
- Shape Constraints: Moulding is generally restricted to shapes that allow easy removal from the mold, limiting the creation of certain complex geometries.
Types of Moulding Process
Forging Process
Forging involves heating materials until they are red-hot and then hammering them into shape. In industrial applications, instead of a hammer, mould is used to shape the material.
Forging utilizes the plasticity of metals like steel and aluminium alloys. A metal ingot or cylinder is hammered or pressed with significant force, causing plastic deformation to achieve the desired shape. There are two main types of forging: hot forging and cold forging. Hot forging involves heating the material to around 1,100°C–1,250°C for iron-based materials and approximately 400°C for aluminium-based materials. Cold forging, on the other hand, is performed at room temperature, although the material may heat up due to deformation.
The key benefit of forging is that it refines the internal structure of the metal, aligning the crystal grains and enhancing material strength. This process is crucial for producing components that require high durability, such as automotive parts, aerospace components, and tools.
Main Applications of Forging
Forged products are commonly used in:
- Automotive Parts: Crankshafts, connecting rods, and other critical components.
- Aerospace Parts: Engine turbines and landing gear.
- Power Plant Components: Turbine main shafts.
- Tools: Knives, pliers, and other hand tools.
Casting Process
Casting, another method for processing metals like iron and aluminium, is one of the oldest known metalworking techniques. It involves pouring molten metal into a mold and allowing it to cool and solidify into the desired shape.
Casting entails melting metal and pouring it into molds made from materials like metal, sand, or plaster. This method allows for the creation of complex shapes more easily than forging. While metal molds can be costly, sand and plaster molds are more affordable and suitable for producing unique, low-volume items. However, casting requires extensive heating equipment and handling facilities, making it less flexible and sometimes resulting in internal cavities, known as “pores,” within the final product. Cast iron, commonly used in casting, is relatively brittle due to its higher carbon content, compared to forged products.
Main Applications of Casting
Casting is ideal for mass production of complex shapes, such as:
- Automotive Parts: Engine blocks, transmission cases, and wheel rims.
- Consumer Electronics: Housings for computers and cameras.
- Household Items: Kettles, frying pans, and manhole covers.
Pressing Process
Pressing involves using a mold to shape materials by applying pressure. This method, widely used for processing thin metal sheets, also finds applications in other materials like paper and plastic.
In pressing, thin metal sheets, such as SPCC, are deformed by pressing them into a mold. This method utilizes the plastic deformation properties of metals and is distinct from forging, which typically uses bulkier materials. Common metals used in pressing include steel and aluminum alloys. Unlike forging, pressing generally requires less force and is conducted at room temperature.
Pressing is closely related to sheet metal processing. Both methods involve deforming thin metal sheets using molds, but pressing is better suited for mass production of identical parts, such as car body panels or rocket components.
Main Applications of Pressing
Pressing is mainly used for manufacturing lightweight and thin products, such as:
- Aerospace Parts: Outer shells of rockets and aircraft.
- Automotive Parts: Body panels and doors.
- Consumer Electronics: Washing machine drums and fluorescent light fixtures.
- Household Items: Spoons, coins, and other everyday items.
Injection Moulding
Moving on from metal processing, injection moulding is a key technique used for shaping plastics, as well as some rubber materials. This section will focus on plastic injection moulding.
Injection moulding involves melting plastic resin and injecting it under pressure into a mold. The material then cools and solidifies into the final product shape. The raw materials, typically in pellet or powder form, can include various additives and colorants to enhance product functionality. The molds are usually made from stainless steel or specialized metals, equipped with heating and cooling systems to maintain precise temperature control.
Injection moulding shares similarities with casting in that it involves pouring a liquid material into a mold. However, the materials used differ, and injection moulding can accommodate complex processes like two-shot moulding, where two different plastics are injected to form a single part, or insert moulding, where metal components are placed in the mold before injection to create a composite product.
Main Applications of Injection Moulding
Plastic products, known for their lightweight and durability, are widely produced through injection moulding. Applications include:
- Household Items: Dishes, stationery, etc.
- Containers: Bottles for detergents, beverages, etc.
- Toys: Casings and internal components.
- Electronics: Casings and decorative parts.
Conclusion
Moulding processes, including forging, casting, pressing, and injection moulding, utilize molds to shape materials. They are ideal for mass-producing identical, high-quality products. However, the initial cost and time investment for mold creation can be substantial, making these methods less suitable for low-volume, high-variety production. Understanding these techniques is essential for selecting the right manufacturing process based on material properties and production requirements.