BLOG » Understanding Sheet Metal Parts and Fabrication
Understanding Sheet Metal Parts and Fabrication
Sheet metals have evolved beyond its basic definition to encompass the intricate art of shaping metal into various forms. Widely deployed in machinery, electrical enclosures, architectural structures, and beyond, sheet metals play a pivotal role in modern fabrication processes. In this article, we embark on a journey to unravel the fundamental facets of sheet metal—essential knowledge for designers and engineers venturing into the realm of metal fabrication. By grasping the intricacies of sheet metal, readers can navigate the complexities of design and manufacturing with confidence.
What are Sheet Metals?
Sheet metals are thin, flat pieces of metal that are produced through industrial processes such as rolling, pressing, or hammering metal into uniform thicknesses. They are widely used in manufacturing and construction due to their versatility, strength, and lightweight properties. Sheet metals are typically made from materials such as steel, aluminium, brass, copper, or stainless steel, and their thickness can range from thin foils to thicker plates. Beyond rolling and pressing, additional processes like cutting, stamping, and laser cutting are often employed to shape and refine sheet metals for specific applications. Their adaptability makes them essential for a variety of industries, from automotive and aerospace engineering to electronics, appliances, and architectural designs. Thanks to their malleability, sheet metals can be easily shaped, joined, and manipulated, making them a cornerstone material for countless manufacturing needs.
What is Sheet Metal Fabrications?
Sheet metal fabrication involves the art of transforming thin metal sheets through the application of force, a technique that harnesses the plasticity of metals to mold them into desired shapes. Utilizing machinery such as press brakes, craftsmen and manufacturers manipulate metal sheets to bring their visions to life.
At the heart of sheet metal fabrication lies plastic deformation—a process that capitalizes on the malleability of metals. When force is applied to a metal sheet, it undergoes gradual deformation. Initially, the metal exhibits elastic deformation, attempting to revert to its original state once the force is removed. However, surpassing a critical threshold—the yield point—renders the metal incapable of returning to its initial form, resulting in permanent plastic deformation. It is this transformative process that forms the foundation of sheet metal fabrication.
Applications of Sheet Metal Parts
Sheet metal parts find applications in various facets of our lives, including industrial products, consumer goods, internal components of electronics like computers and televisions, buildings, crafts, automotive bodies, and more. They are extensively utilized in industrial settings, factory production equipment, food manufacturing equipment, and others. Whether as brackets, covers, chassis components, or rails, sheet metal parts embody versatility, enabling the fabrication of intricate designs and the realization of innovative concepts.
Sheet Metal Fabrication TechniquesFjo
In the realm of sheet metal fabrication, various techniques come into play, each tailored to specific applications and requirements. Mechanical sheet metal fabrication, conducted with precision machinery and molds, dominates industrial settings, while manual sheet metal techniques, involving handcrafted manipulation, find their niche in traditional craftsmanship and automotive repairs. The architectural domain, on the other hand, presents a fusion of both mechanical and manual processes, where custom-built metal components adorn buildings with bespoke elegance.
Sheet Metal Fabrication Process
The sheet metal fabrication process comprises approximately eight distinct stages, each playing a crucial role. Let’s explore each phase in detail:
Unfolding and Programming
While designs are often crafted using 3D CAD, sheet metal fabrication necessitates transforming these designs into a flat state for single-sheet fabrication. This involves digitally “unfolding” designs and optimizing layouts for efficient material usage, accompanied by the initiation of machining programming.
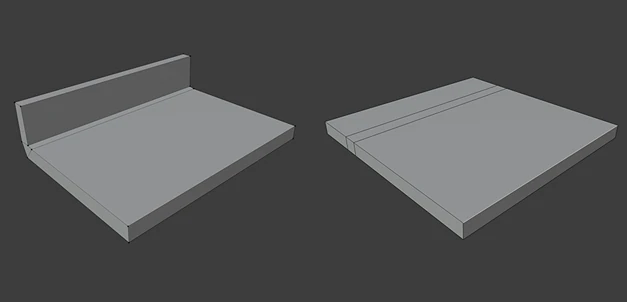
Blanking and Cutting
This stage involves cutting out the perimeter and internal holes of metal sheets, known as blanks, using laser cutting machines or turret punch presses. Laser machines excel at high-speed cutting of outer perimeters and large holes, while turret punch presses handle numerous hole drilling and shaping tasks. Some facilities utilize hybrid “laser-punch press” machines to leverage the advantages of both methods.
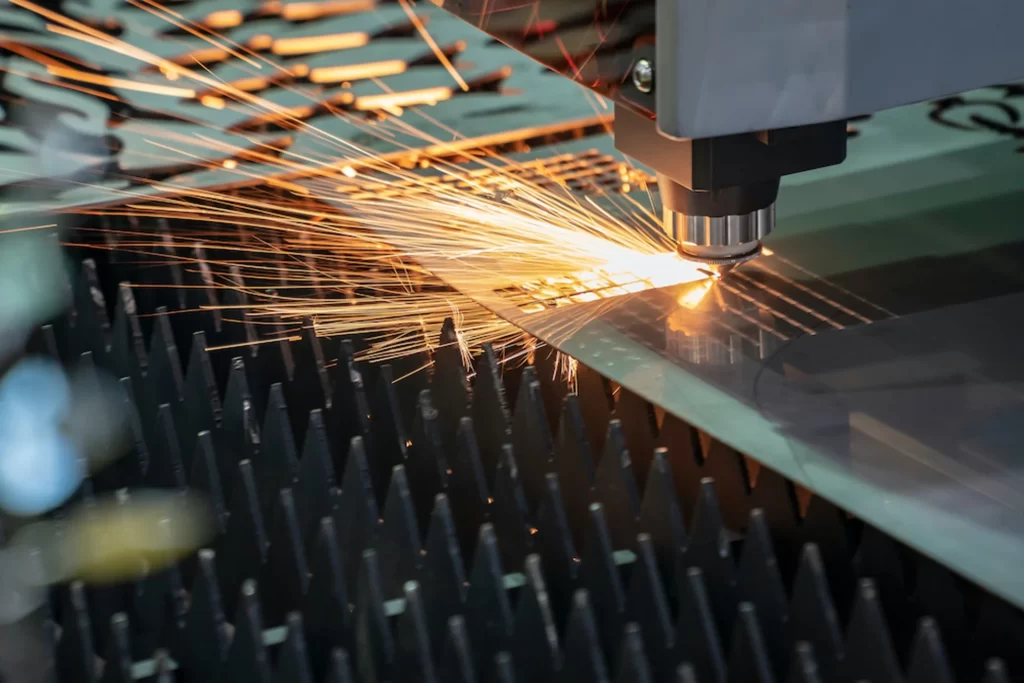
Deburring
Residual burrs, common after cutting processes, require removal to achieve precise dimensions. Deburring ensures the elimination of imperfections, whether through manual methods or automated processes, aligning client expectations with the finished product.
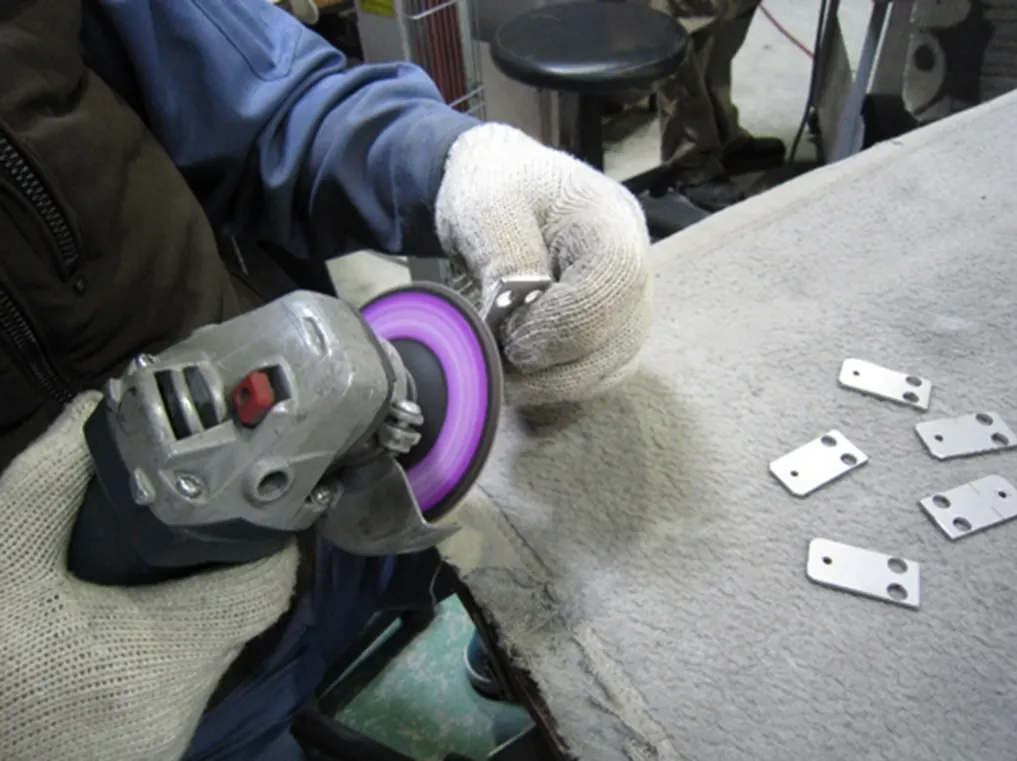
Bending
The bending process, facilitated by a press brake, empowers manufacturers to shape metal sheets with precision and finesse. Whether crafting intricate angles or elegant curves, the press brake – sometimes referred to as a bending machine or bender – is instrumental in achieving desired configurations, bringing designs to life with seamless accuracy.
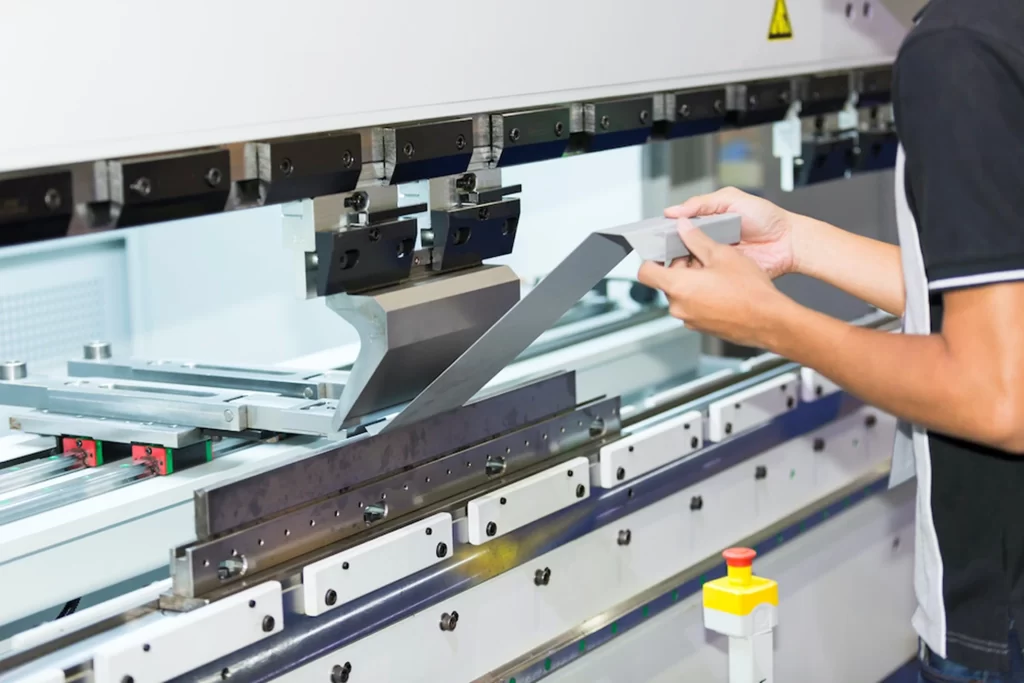
Finishing
In the finishing process of sheet metal fabrication, tasks include removing thermal distortion caused by welding, grinding down raised areas built up by filler welding, electrolytically removing weld burns, and surface polishing treatments (such as polishing and buffing).
Assembly
Assembly involves combining multiple parts, mainly using fastening components such as bolts, nuts, or rivets. This method is often chosen for areas where welding-level strength is not required or where disassembly is necessary later. Assembly work is also known as “assembly,” ranging from small-scale component assembly to medium-scale unit assembly and the final assembly of entire machines or devices. In the sheet metal fabrication industry, some companies refer to the assembly process using welding as “assembly” (welding assembly).
Inspenction
Pre-shipment inspection of sheet metal products typically involves visual inspections for dimensional accuracy and appearance. Dimensional inspections primarily use tools such as calipers, scales, and angle gauges to compare dimensions, hole positions, and accuracy between the drawing and the finished product. Visual inspection checks for scratches or burrs on the product. Some factories may use image measuring machines or coordinate measuring machines for inspection.
Selecting the Right Materials for Sheet Metal Components
A wide array of materials finds application in sheet metal fabrication, each with its unique properties and advantages:
1. Steel
Renowned for its versatility and affordability, steel materials such as SGCC and SECC are staples in sheet metal fabrication. While SPCC offers ease of processing, it requires additional surface treatments like painting or plating to enhance corrosion resistance. SECC boasts superior paint adhesion properties, making it an ideal choice for applications requiring pristine finishes. Additionally, SGCC steel offers enhanced corrosion resistance, making it indispensable for outdoor applications where rust prevention is paramount.
2. Stainless Steel
Stainless steel sheet metals are highly valued for their exceptional corrosion resistance, durability, and sleek aesthetic appeal. These properties make them a preferred choice for applications in industries such as food processing, medical devices, and architecture, where hygiene and visual allure are paramount. One of the most commonly used grades is EN 1.4301 (equivalent to SUS304), which features excellent machinability and is suitable for complex processing such as cutting, bending, and welding. It provides good corrosion resistance and is often used for general-purpose applications.
For specialised applications, other stainless steel grades offer unique advantages. EN 1.4305 (equivalent to SUS303) is an austenitic stainless steel that boasts excellent machinability due to the addition of sulfur, making it a prime choice for precision components requiring extensive machining. However, it has slightly reduced corrosion resistance compared to SUS304, so it is best suited for applications in low-corrosive environments.
Another notable grade is EN 1.4401 (equivalent to SUS316), which provides enhanced corrosion resistance due to its molybdenum content. This makes it ideal for environments exposed to aggressive chemicals, saltwater, or high levels of humidity. Commonly used in marine, pharmaceutical, and food-processing industries, SUS316 offers durability in highly corrosive conditions, outperforming other grades in demanding applications.
Stainless steel sheet metals provide a reliable and durable solution for various industries. Their versatility, ease of processing, and resistance to oxidation and staining make them suitable for creating components that deliver both functionality and aesthetic appeal, with minimal maintenance requirements.
3. Aluminum
Aluminium sheet metals are prized for their lightweight properties, excellent corrosion resistance, and impressive thermal and electrical conductivity. These qualities make aluminium an indispensable material in industries such as aerospace, automotive, and electronics, where weight-sensitive and heat-dissipating components are critical. A5052, one of the most popular aluminium alloys, offers an outstanding balance of strength, formability, and corrosion resistance. However, aluminium sheet metals present unique processing challenges. For example, due to their low absorption of laser light, higher laser power is required for laser cutting. Additionally, bending thicker aluminium sheets can result in cracking if not handled correctly, necessitating careful planning and the use of proper tooling. Aluminium’s high thermal conductivity also demands specialised welding techniques to ensure precise and reliable joints. Despite these challenges, the benefits of aluminium sheet metals—such as reduced weight and high durability—make them a top choice for countless applications, from lightweight structural components to heat-exchange systems.
Surface Treatment for Sheet Metal Components
When it comes to enhancing the functionality, durability, and aesthetics of sheet metal components, surface treatments play a crucial role. These treatments, ranging from plating to painting and laser marking, are tailored to meet specific application requirements, offering solutions for corrosion resistance, color customization, and information labeling.
Painting
Painting involves the application of paint coatings to sheet metal surfaces, providing not only color but also durability and protection against corrosion. This specialized form of painting is essential for sheet metal components, with the choice of paint and application method varying based on the intended use and desired properties. Powder coating, a popular option, delivers robust coatings suitable for various applications, such as control panels and machinery covers, offering excellent color retention and weather resistance.
Plating
Plating of sheet metal components is a key method for enhancing corrosion resistance, wear resistance, or decorative appeal. The selection of plating methods depends on the material, with options like electroless nickel plating for SPCC and trivalent chromate plating for aluminum. Consulting specialized surface treatment companies ensures optimal corrosion resistance and surface finish, particularly for materials where plating may present challenges.
Anodising
Anodising is a specialized surface treatment for aluminum, providing enhanced corrosion and wear resistance by forming an artificial oxide film on the surface. This method offers various color options, including white and black anodising, with specialized providers offering additional color choices to suit specific aesthetic preferences.
Laser Marking
Laser marking is a versatile method for decorating surfaces and adding essential information like part numbers or barcodes to sheet metal components. This process, categorized under surface modification, ensures permanent markings unless intentionally removed, making it ideal for traceability and identification purposes.
Tips for Designing Sheet Metal Components
Designing sheet metal components requires careful consideration of manufacturability and processing capabilities to ensure successful fabrication. Here are three primary considerations to keep in mind during the design phase:
1. Ensure Designs can be Unfolded Into a Single Sheet for Processing
Sheet metal components are formed from a single sheet through cutting and bending processes. Designs that cannot be unfolded into a single sheet are impractical for fabrication, highlighting the importance of considering unfolding during the design phase.
2. Consider Processing Limitations
Sheet metal components are subject to limitations based on bending and forming capabilities, which can vary depending on factors like bending proximity to holes or minimum distances from edges. Consulting processing partners to confirm processing capabilities upfront can help avoid costly rework post-order placement.
3. Beware of Interference During Bending
Interference between the component and bending tools may occur during processing, especially in cases where bent edges exceed shorter edges. Considering potential interference during the design phase can help prevent processing issues or errors.
Summary
In conclusion, the process of sheet metal fabrication stands as a versatile technique, vital in the fabrication of industrial components, factory infrastructure, and food processing equipment, among other applications. From machine sheet metal to handcrafted pieces and architectural installations, this method offers a diverse range of solutions. Blanking and bending are the cornerstone of sheet metal processing at meviy, while materials like steel, stainless steel, and aluminum are common choices. Moreover, surface treatments such as painting, plating, and anodising enhance both aesthetics and functionality. With its myriad applications and flexible methodologies, sheet metal processing remains an indispensable aspect of modern manufacturing.