BLOG » What is Rolling Process – Process Overview
What is Rolling Process – Process Overview
Rolling process is a subset of metalworking process that leverages the plasticity of metals. Rather than creating final products, this method is typically used to produce materials like sheets and rods. The primary advantage of rolling process is its ability to mass-produce uniform metal materials at a relatively low cost. In this article, we will delve into the different types of rolling processing and the machinery used.
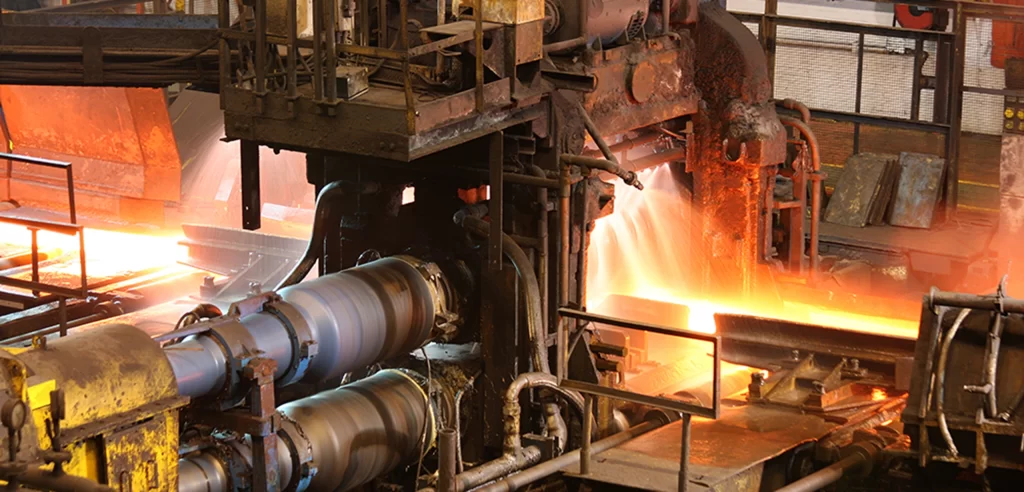
What is Rolling Process?
Rolling process involves passing metal through rotating rolls to compress and elongate it. This technique of plastic deformation is known for its efficiency in producing with uniform cross-sections at high speeds. Products range from metal sheets and rods to longer components and even square or round tubular materials.
These rolled parts find extensive use in construction and manufacturing industries. Notably, metal sheets produced through rolling are commonly applied as beverage cans, batteries, and automotive parts.
Rolling processes can be categorized into three types based on the temperature during processing: hot rolling, cold rolling, and warm rolling.
Hot Rolling
Hot rolling involves heating metal to make it malleable before processing. For steel, this means working at temperatures between 900°C and 1,200°C, where the metal becomes red-hot and passes through rolls. Here are the pros and cons of hot rolling:
Advantages
– Improved Workability: The metal’s resistance to deformation decreases at high temperatures, enhancing its workability.
– Enhanced Material Properties: The process strengthens the crystal structure, resulting in a tougher material.
– No Work Hardening: Since the processing temperature is above the metal’s recrystallization point, work hardening does not occur.
DISADVANTAGES
– Dimensional Precision: Significant temperature changes during and after processing can lead to lower dimensional accuracy.
– Surface Quality: Oxidation in the presence of air results in a scale (oxide layer) on the surface, leading to a less aesthetically pleasing finish.
– Energy and Cost: Heating the material requires substantial energy and incurs higher costs.
Cold Rolling
Cold rolling is a metalworking process performed at room temperature. Unlike hot rolling, the material is not heated before processing. However, as the material deforms, it generates heat, causing its temperature to rise. For steel, cold rolling is typically done below 600°C. Here are the key advantages and disadvantages of cold rolling:
Advantages
– No Heating Equipment Required: Since the material is processed at room temperature, there’s no need for heating equipment, making the material easier to handle.
-High Dimensional Precision: Cold rolling offers higher dimensional accuracy compared to hot rolling.
– Pleasing Finish: The process produces a glossy surface, resulting in an aesthetically pleasing finish.
Disadvantages
-High Deformation Resistance: The metal’s resistance to deformation is greater at lower temperatures, requiring more force for processing.
– Work Hardening: Cold rolling can cause work hardening, necessitating subsequent heat treatment, such as annealing, to relieve residual stresses.
Warm Rolling
Warm rolling sits between hot and cold rolling processes. For steel, it is typically conducted at temperatures ranging from 600°C to 900°C. This method mitigates some disadvantages of both hot and cold rolling and is commonly used in the production of aluminum foil.
Key Rolling Machines in Metalworking
Rolling machines are specialized equipment used for rolling processing. Their configurations vary based on the desired shape and the number of rolls involved. Here are six commonly used rolling machines in manufacturing:
Two-High Rolling Mill
The two-high rolling mill consists of two opposing rolls that compress the metal. This simple configuration is used for rough rolling, such as converting ingots into slabs with thicknesses ranging from 20mm to 30mm, and for thin sheet rolling.
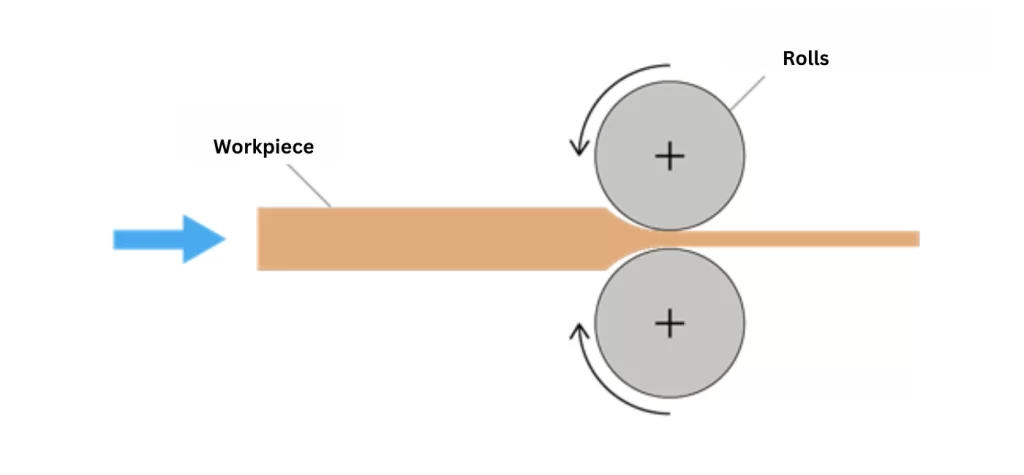
Four-High Rolling Mill
A four-high rolling mill features two work rolls and two backup rolls, supporting each work roll from behind. This design allows for high-precision processing by reducing work roll deflection. It is used for rolling not only steel but also copper and aluminum.
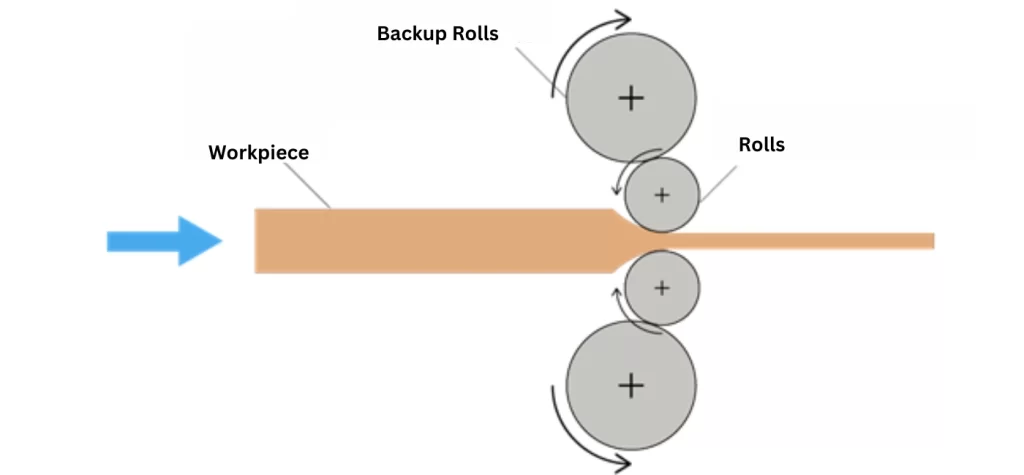
Multi-Roll Mills (Cluster Mills)
Multi-roll mills, also known as cluster mills, feature more backup rolls than four-high rolling mills. The name “cluster” comes from the numerous backup rolls that support the work roll, enabling higher pressure application. This design allows for the processing of hard metals like stainless steel. Additionally, the small diameter of the work roll, combined with robust support, prevents deflection, making it ideal for cold rolling extremely thin materials such as copper foil.
Planetary Rolling Mills
Planetary rolling mills are characterized by the arrangement of several small work rolls around the circumference of a larger backup roll. These small work rolls roll over the material in a planetary motion, allowing for substantial reduction and high rolling efficiency. This setup is particularly effective for heavy reductions and processing large quantities of metal.
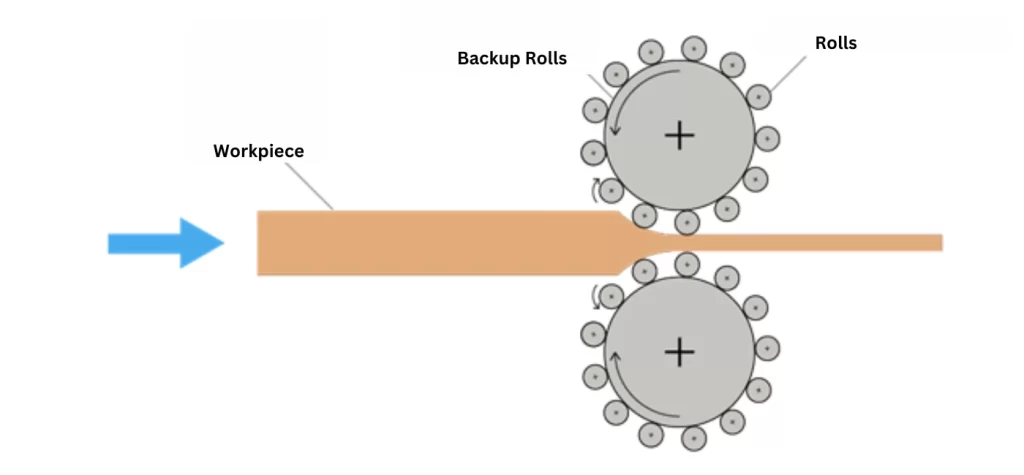
Universal Rolling Mills
Universal rolling mills are distinctive because they include rolls positioned horizontally and vertically. This configuration allows the mill to apply pressure in multiple directions simultaneously. It is particularly suited for creating complex cross-sectional shapes, such as H-beams, from initially simple rod-shaped materials.
Piercing Mills (Mannesmann Mills)
Piercing mills, or Mannesmann mills, are specialized for producing seamless steel tubes. They use a piercing plug inside the hollow metal and external conical rolls to shape the tube. The absence of seams makes these tubes ideal for high-pressure applications such as oil pipelines, boilers, and other critical infrastructure where the transport of liquids or gases is involved.
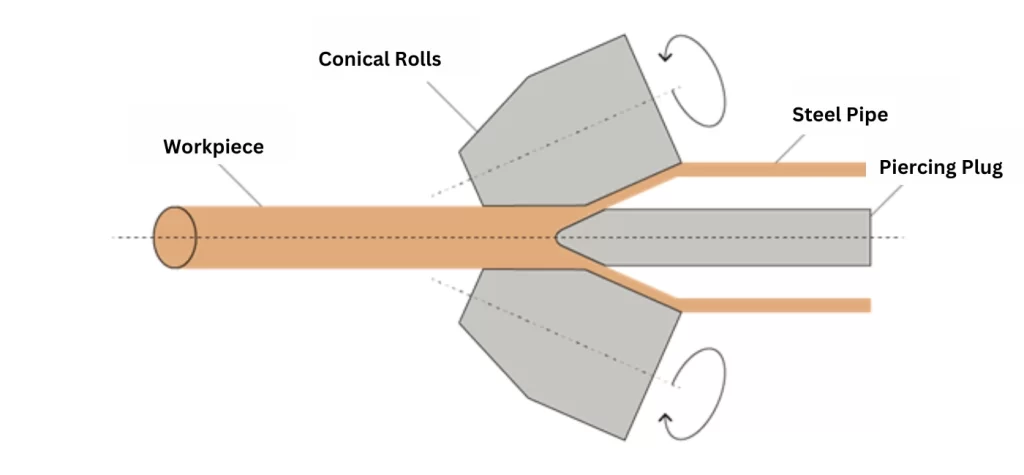
Conclusion
Rolling process is a type of plastic deformation method that involves passing metal through rollers to create sheets, rods, or tubes. Based on the processing temperature, rolling can be classified into hot rolling, cold rolling, and warm rolling. The machines used for rolling vary widely depending on the intended application. For sheet materials, two-high and four-high mills, as well as cluster mills, are common. Universal rolling mills are used for producing complex shapes like H-beams, while piercing mills are used for creating seamless tubes.
At meviy, we provide quotations and processing for sheet metal parts and CNC milling parts required for factory equipment and machinery. We offer a variety of materials, surface treatments, and coatings for sheet metal parts, including SPHC (hot-rolled steel sheet) and SPCC (cold-rolled steel sheet).