BLOG » Wie man die besten korrosionsbeständigen Metalle auswählt
Wie man die besten korrosionsbeständigen Metalle auswählt
Achten Sie bei der Materialauswahl für Bauteile, die in korrosionsanfälligen Umgebungen eingesetzt werden, immer darauf, dass Sie dasselbe Metall verwenden? Wenn ja, könnte es Zeit sein, Ihre Entscheidung zu überdenken. Eine hohe Korrosionsbeständigkeit ist entscheidend, um Wartungskosten zu senken und die Haltbarkeit Ihrer Produkte zu gewährleisten. Andernfalls riskieren Sie, dass die Lebensdauer erheblich verkürzt wird.
Es gibt verschiedene Ansätze, um Korrosion zu verhindern. Dazu gehört die Verwendung von Metallen, die von Natur aus rostbeständig sind, oder der Einsatz von Oberflächenbehandlungen, die eine schützende Schicht auf dem Material bilden.
In diesem Leitfaden stellen wir Ihnen neun verschiedene Metalle vor – sowohl mit als auch ohne Oberflächenbehandlung. Dabei gehen wir auf ihre besonderen Eigenschaften, Vorteile und wichtige Aspekte ein. Vielleicht entdecken Sie dabei Materialien mit überraschenden Eigenschaften, die Ihr nächstes Projekt entscheidend verbessern könnten.
Rostende Metalle vs. korrosionsbeständige Metalle
Alle Metalle können rosten, doch wie stark dies geschieht, hängt von der Metallart und den Umgebungsbedingungen ab. Besonders schnell korrodieren Metalle, die Feuchtigkeit oder Salzwasser ausgesetzt sind.
Rostbildung
Rost entsteht, wenn Metall mit Sauerstoff aus der Luft reagiert und dabei Oxide bildet. Kommt Metall mit Wasser in Kontakt, wird es ionisiert, was die Oxidation begünstigt. Wie anfällig ein Metall für Rost ist, hängt von seiner sogenannten Ionisierungstendenz ab. Einfach gesagt: Metalle mit hoher Ionisierungstendenz, wie Lithium oder Kalium, rosten schneller. Dagegen sind Metalle wie Gold oder Platin, die eine niedrige Ionisierungstendenz haben, deutlich korrosionsbeständiger.
3 Arten korrosionsbeständiger Metalle
Obwohl die meisten Metalle rosten, gibt es einige, die aufgrund ihrer natürlichen Eigenschaften korrosionsbeständiger sind. Diese lassen sich in drei Kategorien einteilen:
- Metalle, die nicht rosten (z. B. Gold, Platin)
Diese Metalle haben eine sehr geringe Ionisierungstendenz und sind von Natur aus widerstandsfähig gegen Rost. Allerdings sind sie teuer, weshalb ihr Einsatz gut abgewogen werden sollte.
- Metalle mit passiver Oxidschicht (z. B. Aluminium, Titan, Nickel, Edelstahl)
Metalle wie Aluminium und Titan bilden bei Kontakt mit Sauerstoff eine schützende Oxidschicht auf ihrer Oberfläche. Diese Schicht verhindert weitere Oxidation und schützt das darunterliegende Material. Edelstahl enthält Chrom, das diese schützende Oxidschicht bildet, wodurch er besonders korrosionsbeständig ist.
- Metalle, bei denen Rost als Schutzschicht dient (z. B. Kupfer, Zink)
Bei diesen Metallen wirkt die entstandene Rost- oder Oxidschicht als Schutz für die darunterliegenden Schichten. Diese Schicht ist jedoch nicht so robust wie eine passive Oxidschicht und kann durch säurehaltige Substanzen wie Essig leicht entfernt werden.
Arten von korrosionsbeständigen Oberflächenbehandlungen
Um Korrosion bei anfälligen Metallen zu vermeiden, werden Oberflächenbehandlungen eingesetzt. Die häufigste Methode ist das Auftragen einer Schutzschicht, die das Metall vor Luft und Feuchtigkeit abschirmt. Diese Oberflächenbehandlungen lassen sich in zwei Hauptarten unterteilen: organische Beschichtungen und anorganische Beschichtungen.
Organische Oberflächenbehandlungen (Lackierung, Öl)
Die Lackierung ist ein klassisches Beispiel für eine organische Beschichtung. Das Auftragen von Ölen oder das Umwickeln von Bauteilen mit Gummi oder Kunststoff sind weitere gängige organische Methoden zum Schutz von Metalloberflächen.
Anorganische Obeflächenbehandlungen (Galvanisieren, Chemische Behandlung)
Beim Galvanisieren wird eine dünne Metallschicht, z. B. Chrom oder Zink, zum Schutz des Grundmetalls aufgebracht. Bei diesen Beschichtungen handelt es sich entweder um passivierende Metalle (wie Chrom) oder um Opfermetalle (wie Zink), die zuerst korrodieren und das darunter liegende Metall schützen. Chemische Behandlungen wie Chromatieren oder Eloxieren (bei Aluminium) sind ebenfalls üblich, um die Korrosionsbeständigkeit zu erhöhen.
5 Oberflächenbehandlungen für Korrosionsbeständigkeit und 4 hochkorrosionsbeständige Metalle
In diesem Leitfaden bewerten wir die Korrosionsbeständigkeit von neun Metallen – von der höchsten bis zur niedrigsten – und vergleichen dabei ihre Festigkeit, Verschleißfestigkeit und magnetischen Eigenschaften. Klicken Sie auf „Oberflächenbehandlung“ oder „Materialien“, um detaillierte Informationen zu jedem Material zu erhalten. Verwenden Sie diesen Leitfaden, um eine gut informierte Entscheidung für Ihre nächste Materialauswahl zu treffen.
- Oberflächenbehandlungen zur Korrosionsbeständigkeit
- Oberflächenbehandlungen schützen Metalle wirksam vor Oxidation, die auftritt, wenn sie mit Sauerstoff in Berührung kommen. Beachten Sie, dass Oberflächenbehandlungen zusätzliche Kosten verursachen und die Produktionszeit verlängern.
Material | Oberflächenbehandlung | Korrosionsbeständigkeit | Beschichtungsstärke | Abriebfestigkeit | Magnetisch |
---|---|---|---|---|---|
Stahl (SPCC/SPHC/SS400) | Chromatiert (III-wertig) | Stark | Stark | Stark | Gut |
Chemisch vernickelt | Stark | Gut | Stark | Ok | |
Lackiert | Stark | Ok | Ok | Gut | |
Aluminium (A5052) | Eloxiert (Weiß, Schwarz) | Stark | Ok | Nicht gut | Nicht gut |
Stahl (SPCC/SPHC/SS400) | Brüniert | Ok | Nicht gut | Ok | Stark |
Korrosionsresistente Metalle
Metalle, die nicht oberflächenbehandelt werden müssen, senken sowohl die Kosten als auch die Produktionszeit. Sie bieten jedoch in der Regel eine geringere Korrosionsbeständigkeit als behandelte Metalle.
Material | Oberflächenbehandlung | Korrosionsbeständigkeit | Festigkeit | Abriebfestigkeit | Magnetisch | Eigenschaften |
---|---|---|---|---|---|---|
Edelstahl EN 1.4301 equiv. | – | Gut | Stark | Gut | Ok | Es ist robust und kann in einer Vielzahl von Anwendungen eingesetzt werden. |
Aluminium A5052 | – | Gut | Nicht gut | Nicht gut | Nicht gut | Höchst resistent gegen Salzwasser |
Edelstahl EN 1.4016 equiv. | – | Ok | Stark | Gut | Gut | Schlechter verarbeitbar als EN 1.4301 equiv. |
Stahl SECC (Elektrolytisch verzinkt) | Elektrolytisch verzinkt | Ok | Gut | Gut | Gut | Je nach Art lässt er sich gut mit Lackierung kombinieren. |
Beispiel: Brüniert
- Material: Stahl
- Maße: L150 x B150 × H4.5
- Oberflächenbehandlung: Brüniert
- Korrosionsbeständigkeit: Ok
- Magnetisch: Stark
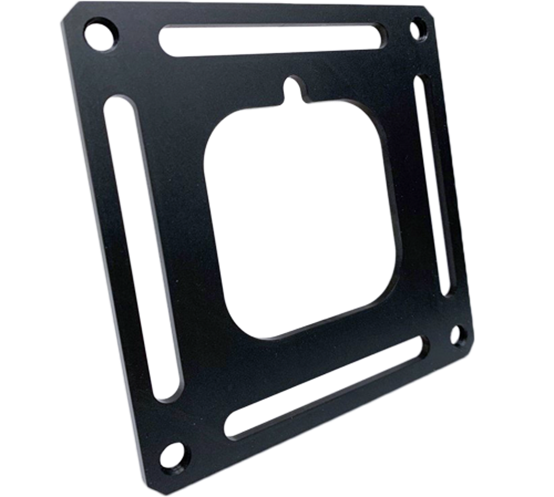
Dieses brünierte Stahl ist günstig und wird üblicherweise für den vorübergehenden Schutz während der Montage verwendet. Durch Zugabe von Öl kann die Korrosionsbeständigkeit weiter erhöht werden, so dass sich diese Methode für Automobil- und Industrieanwendungen eignet. Allerdings kann es aufgrund von Oberflächenfehlern zu Farbabweichungen kommen, und es wird nur für den Innenbereich empfohlen, da es im Vergleich zu anderen Behandlungen eine geringere Korrosionsbeständigkeit aufweist.
Beispiel: Edelstahl (SUS304)

- Material: EN 1.4301 equiv. (SUS304)
- Maße: L48 × B117 × H53
- Oberflächenbehandlung: Unbehandelt
- Korrosionsbeständigkeit: Gut
- Magnetic Properties: Ok
Der Edelstahl EN 1.4301 (SUS304) wird wegen seiner hervorragenden Korrosionsbeständigkeit und Festigkeit häufig verwendet. Aufgrund seiner halbglänzenden Oberfläche eignet er sich für Produkte, die sowohl ästhetisch ansprechend als auch haltbar sein müssen, wie z. B. Küchengeräte und Dekorationsartikel. Allerdings neigt er dazu, Fingerabdrücke anzuziehen und kann korrodieren, wenn er mit rostigen Eisenpartikeln in Berührung kommt.
Fazit
Bei der Auswahl des richtigen Materials für die Korrosionsbeständigkeit geht es um mehr als nur um Kosten und Lieferzeiten. Das Wissen um die Eigenschaften verschiedener Metalle und Oberflächenbehandlungen kann Ihnen helfen, fundierte Entscheidungen zu treffen, die die Lebensdauer Ihrer Produkte verlängern und gleichzeitig deren Leistungsfähigkeit erhalten. Um sofortige Angebote für Oberflächenbehandlungen oder Materialien zu erhalten, laden Sie Ihre 3D-CAD-Daten noch heute bei meviy hoch!