BLOG » Wie man die beste Wärmebehandlung auswählt – Prozessleitfaden
Wie man die beste Wärmebehandlung auswählt – Prozessleitfaden
Bei der Konstruktion von Bauteilen spielen Faktoren wie Härte und Schlagfestigkeit eine entscheidende Rolle bei der Bestimmung ihrer Funktionalität. Bestimmte Bauteile erfordern eine bestimmte Härte oder Widerstandsfähigkeit, insbesondere solche, die mit anderen Bauteilen gleiten oder Stoßkräften ausgesetzt sind.
In Fällen, in denen besondere Eigenschaften erforderlich sind, kann es unzureichend sein, sich allein auf die inhärenten Eigenschaften des Materials zu verlassen. In solchen Fällen ist die Wärmebehandlung die Lösung, mit der die für die kundenspezifischen Bauteile erforderlichen Eigenschaften erreicht werden können. Die Auswahl des geeigneten Materials und der Wärmebehandlungsmethode zur Erzielung der gewünschten Eigenschaften kann jedoch aufgrund der Vielfalt und Komplexität der verfügbaren Wärmebehandlungsoptionen eine Herausforderung darstellen.
Es gibt verschiedene Arten der Wärmebehandlung, die auf unterschiedliche Materialien und Zwecke zugeschnitten sind. Daher sind viele Konstrukteure damit nicht vertraut, es sei denn, sie haben spezifische Anforderungen.
In diesem Artikel haben wir grundlegende Informationen und Eckpunkte für die Auswahl und Anwendung von Wärmebehandlungen zusammengestellt, die üblicherweise bei Bauteilen von Anlagen eingesetzt werden.
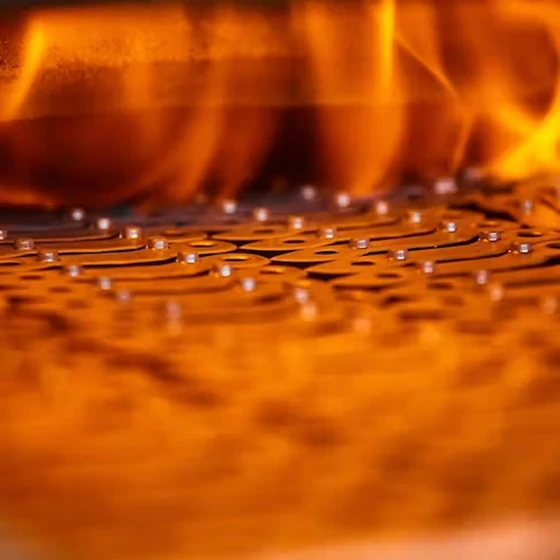
Gängige Wärmebehandlungen
Bei der Wärmebehandlung werden Bauteile kontrollierten Erwärmungs- und Abkühlungsprozessen unterzogen, um Veränderungen in ihrer Gesamt- oder Oberflächenstruktur zu bewirken. Insbesondere bei kohlenstoffhaltigen Stählen können durch die Wärmebehandlung Eigenschaften wie Härte, Korrosionsbeständigkeit, Verschleißfestigkeit und Schlagzähigkeit erheblich verändert werden.
Diese Verfahren werden grob unterteilt in die „Massenwärmebehandlung“, bei der das gesamte Bauteil behandelt wird, und die „Oberflächenwärmebehandlung“, bei der in erster Linie die Oberfläche des Bauteils behandelt wird. Die Massenwärmebehandlung umfasst Verfahren wie Vergüten, Glühen und Normalisieren, während die Oberflächenwärmebehandlung das Induktionshärten, Aufkohlen und Nitrieren umfasst.
Die Auswirkungen der Wärmebehandlung hängen von Faktoren wie der Erwärmungstemperatur, der Abkühlgeschwindigkeit und dem verwendeten Kühlmedium ab. Eine schnelle Abkühlung, wie sie beim Abschrecken auftritt, führt im Allgemeinen zu einer höheren Härte, allerdings auch zu einer höheren Sprödigkeit. Langsamere Abkühlungsmethoden wie das Glühen und Normalisieren zielen dagegen auf eine Verfeinerung der Struktur des Materials ab.
Je nach dem gewünschten Ergebnis der Wärmebehandlung werden verschiedene Kühltechniken wie Wasserabschrecken, Ölabschrecken, Luftkühlung und Ofenkühlung gewählt.
Es ist unbedingt erforderlich, die nachfolgenden Inhalte sorgfältig zu berücksichtigen, um die optimale Kombination aus Material und Wärmebehandlung zu bestimmen, damit die gewünschte Funktionalität und Leistung Ihrer Bauteile erreicht wird.
Grundlagen Massenwärmebehandlung von Bauteilen
Stahlzusammensetzungen mit unterschiedlichem Kohlenstoffgehalt weisen unterschiedliche Umwandlungstemperaturen auf, insbesondere um die kritische Schwelle von 0,8 % Kohlenstoffgehalt. Stähle mit einem Kohlenstoffgehalt von genau 0,8 % fallen in die Kategorie der eutektoiden Stähle, während diejenigen, die unter diesem Schwellenwert liegen, als untereutektoide Stähle und diejenigen, die ihn überschreiten, als übereutektoide Stähle bezeichnet werden.
Arten und Verfahren der Wärmebehandlung
Bei der Wärmebehandlung werden Bauteile aus Stahl einer kontrollierten Erwärmung und anschließenden Abkühlung unterzogen, wodurch ihre Gesamt- oder Oberflächenstruktur verändert wird. Dieser Umwandlungsprozess beeinflusst entscheidende Eigenschaften des Stahls, darunter Härte, Korrosionsbeständigkeit, Verschleißfestigkeit und Schlagfestigkeit.
Die Wärmebehandlungsverfahren lassen sich grob in zwei Kategorien einteilen: die Massenwärmebehandlung, die das gesamte Bauteil betrifft, und die Oberflächenwärmebehandlung, die in erster Linie auf die Oberflächenschichten abzielt. Die Massenwärmebehandlung umfasst Verfahren wie Vergüten, Glühen und Normalisieren. Im Gegensatz dazu umfasst die Oberflächenwärmebehandlung Verfahren wie Induktionshärten, Aufkohlen und Nitrieren.
Die Wirksamkeit der Wärmebehandlung hängt von mehreren Faktoren ab, unter anderem von der Temperatur und der Geschwindigkeit der Erwärmung und Abkühlung. Eine schnelle Abkühlung nach dem Erhitzen, wie sie beim Abschrecken zu beobachten ist, erhöht in der Regel die Härte, wenn auch mit einem potenziellen Kompromiss bei der Sprödigkeit. Langsame Abkühlungsmethoden wie das Glühen und Normalisieren zielen dagegen darauf ab, die Struktur des Materials zu verfeinern, ohne seine Integrität zu beeinträchtigen.
Die verschiedenen Kühltechniken, wie z. B. Wasserabschrecken, Ölabschrecken, Luftkühlung und Ofenkühlung, werden auf der Grundlage der gewünschten Ergebnisse des Wärmebehandlungsprozesses sorgfältig ausgewählt.
Die folgenden Abschnitte liefern wertvolle Erkenntnisse zur Bestimmung der optimalen Kombinationen aus Material und Wärmebehandlung, um die gewünschten Eigenschaften und Leistungen zu erzielen.
Abschrecken/Temperieren: Den Prozess verstehen
Wenn Stahl auf Temperaturen um 800 °C erhitzt wird, wandelt er sich in eine Struktur um, die als „Austenit“ bezeichnet wird. Diese Umwandlung ist entscheidend für die Vorbereitung des Materials auf die weitere Verarbeitung. Anschließend wird das Material schnell abgekühlt, ein Prozess, der als „Abschrecken“ bezeichnet wird, um die Bildung einer gehärteten Struktur, die als „Martensit“ bekannt ist, zu bewirken.
Das Abschrecken erhöht zwar die Härte, macht das Material aber häufig spröde und damit für den unmittelbaren Einsatz ungeeignet. Um dem entgegenzuwirken, wird das Material einem „Anlassen“ genannten Prozess unterzogen, bei dem es auf eine niedrigere Temperatur als beim Abschrecken wiedererwärmt und dann langsam abgekühlt wird. Beim Anlassen spielt die Temperatur der Wiedererwärmung eine entscheidende Rolle. Das Wiedererwärmen bei höheren Temperaturen verringert die Härte und erhöht die Duktilität, was als „Hochtemperaturanlassen“ bezeichnet wird. Umgekehrt wird beim Wiedererwärmen bei niedrigeren Temperaturen die Härte gegenüber der Duktilität bevorzugt, was als „Anlassen bei niedriger Temperatur“ bezeichnet wird.
In der Regel werden das Abschrecken und das Anlassen gemeinsam durchgeführt, um ein optimales Gleichgewicht von Härte und Duktilität im Endprodukt zu gewährleisten.
Das Abschrecken umfasst einen sorgfältig kontrollierten Erhitzungs- und anschließenden Abkühlungsprozess.
Das Erhitzen erfolgt in speziellen Öfen, in denen die Temperatur des Materials auf den Punkt erhöht wird, an dem es sich in Austenit umwandelt. Die Temperatur variiert je nach Stahlsorte, wobei für untereutektoide Stähle Temperaturen um A3 und für übereutektoide Stähle Temperaturen etwas über A1 (ca. 30-50°C) erforderlich sind.
Eine sorgfältige Temperaturkontrolle während des Abschreckens ist entscheidend, um eine effektive Umwandlung zu gewährleisten. Eine Über- oder Unterschreitung des optimalen Temperaturbereichs kann zu einer unvollständigen Umwandlung oder unerwünschten Eigenschaften des Endprodukts führen.
Nach dem Erhitzen wird das Material schnell abgekühlt, um die Bildung von Martensit einzuleiten. Je nach gewünschtem Ergebnis und Materialeigenschaften kommen verschiedene Kühlmethoden zum Einsatz, z. B. Wasserabschrecken, Ölabschrecken, Luftkühlung, Wasserlösungen und Salzbadkühlung.
Jede Kühlmethode bietet einzigartige Vorteile und Herausforderungen. Die Wasserabschreckung beispielsweise bietet schnelle Abkühlungsraten zu geringen Kosten, kann aber bei unsachgemäßer Ausführung zu Verformungen führen. Im Gegensatz dazu bietet die Ölabschreckung eine gleichmäßigere Abkühlung, allerdings mit einer langsameren Geschwindigkeit.
Die Wahl der geeigneten Abkühlungsmethode hängt von Faktoren wie dem Materialtyp, den gewünschten Eigenschaften und den Fertigungseinschränkungen ab.
Weichglühen
Weichglühen ist eine Wärmebehandlung, bei der Metalle nach dem Erhitzen allmählich abgekühlt werden, was zu einer gleichmäßigen und weicheren Struktur führt. Durch diese Technik werden innere Spannungen abgebaut und die Bearbeitbarkeit verbessert. Das Weichglühen umfasst verschiedene Verfahren wie das Vollglühen, das Erweichungsglühen, das Spannungsarmglühen, das Diffusionsglühen und das Kugelglühen, die je nach gewünschtem Ergebnis auf bestimmte Temperaturbereiche zugeschnitten sind. Weichglühen wird in der Regel bei Kohlenstoffstahl angewendet, aber auch bei Edelstahl, Aluminiumlegierungen und anderen Materialien.
Weichglühen wird oft mit dem Konzept der „Erweichung“ des Materials in Verbindung gebracht, wodurch es sich besser bearbeiten lässt.
Darüber hinaus werden durch das Weichglühen Eigenspannungen in den Bauteilen beseitigt und deren Bearbeitbarkeit durch Wärmezufuhr verbessert. Bei der spanabhebenden Bearbeitung von dünnwandigen Produkten kann eine rechtzeitige Behandlung durch Weichglühen die Genauigkeit des Endprodukts verbessern.
Das Weichglühen kann sowohl an Rohmaterialien als auch an teilweise bearbeiteten Bauteilen durchgeführt werden. Insbesondere bei Materialien wie EN 1.4301 äquivalent (SUS304), die aufgrund von Bearbeitungsspannungen zu Verformungen neigen, bietet das Weichglühen eine verbesserte Genauigkeit, z. B. bei der Ebenheit.
Ein aktiver Informationsaustausch mit den Fertigungsbetrieben kann dazu beitragen, die Durchführbarkeit und den Zeitpunkt des Weichglühens zu bestimmen.
Normalglühen/Normalisieren
Normalglühen ist ein Wärmebehandlungsverfahren zur Homogenisierung und Verfeinerung des Gefüges von Bauteilen aus Stahl, die unter Bedingungen wie Gießen, Schmieden oder Walzen hergestellt werden, bei denen innere Spannungen auftreten können. Durch das Normalglühen wird das Gefüge angeglichen, um die gewünschten mechanischen Eigenschaften zu gewährleisten.
Induktionshärten
Das Induktionshärten im Hochfrequenzbereich ist ein Oberflächenbehandlungsverfahren, bei dem nur die Oberfläche eines Bauteils mithilfe einer Wechselstrom-Induktionserwärmung selektiv auf Temperaturen über 800 °C erhitzt wird. Bei diesem Verfahren, das in erster Linie zur Verbesserung der Härte und Ermüdungsbeständigkeit von wellen- oder zahnradförmigen Bauteilen eingesetzt wird, wird das Bauteil in der Nähe einer elektrischen Heizspule platziert und hochfrequente induzierte Ströme durch die Spule geleitet, um die Oberfläche des Bauteils durch Widerstandserwärmung schnell zu erhitzen. Durch anschließendes Anlassen bei niedrigen Temperaturen wird die Duktilität wiederhergestellt.
Beim Induktionshärten im Hochfrequenzbereich wird nur die Oberfläche behandelt, was zu einer verbesserten Härte und Verschleißfestigkeit führt, während die Zähigkeit im Inneren erhalten bleibt. Da die Erwärmung nur teilweise erfolgt, werden Verformungen und Maßänderungen minimiert.
Bei wellenförmigen Bauteilen kann es nach der Wärmebehandlung zu Verformungen wie z. B. Biegungen kommen, die ein Richten mit Pressen erforderlich machen. Die Oberflächenhärtung durch Induktionshärten im Hochfrequenzbereich induziert Druckeigenspannungen an der Oberfläche, wodurch die Ermüdungsfestigkeit erhöht wird. Außerdem ist die durch Induktionshärten im Hochfrequenzbereich erzielte Oberflächenhärte etwas höher als die durch konventionelles Vergüten erzielte.
Das Induktionshärten im Hochfrequenzbereich gilt aufgrund seiner kurzen Erwärmungszeit als umweltfreundlich und bietet den Vorteil, dass die Bereiche und die Tiefe der Härtung festgelegt werden können. Es handelt sich dabei um eine Form der Oberflächenhärtung, andere Verfahren sind das Flammhärten (HQF), das Elektronenstrahlhärten und das Laserhärten.
Aufkohlen
Um Stahl durch Abschrecken zu härten, ist Kohlenstoff erforderlich. Während Stahl mit hohem Kohlenstoffgehalt, z. B. Kohlenstoffstahl, für das Abschrecken geeignet ist, reagiert Stahl mit niedrigem Kohlenstoffgehalt, z. B. Stahl mit niedrigem Kohlenstoffgehalt, nicht gut auf dieses Verfahren. In solchen Fällen wird eine Aufkohlung durchgeführt, um den Kohlenstoffgehalt an der Oberfläche zu erhöhen und das Abschrecken zu erleichtern.
Stahl mit niedrigem Kohlenstoffgehalt ist zwar kostengünstig und lässt sich im Vergleich zu Stahl mit hohem Kohlenstoffgehalt hervorragend bearbeiten, weist aber oft eine geringere Härte auf. Durch die Aufkohlung wird die Oberflächenhärte selektiv erhöht, wodurch die Stärken des kohlenstoffarmen Stahls genutzt und seine Schwächen verstärkt werden.
Bei der Aufkohlung wird das Bauteil zusammen mit einem Aufkohlungsmittel erhitzt, sodass der Kohlenstoff in die Oberfläche diffundieren und diese durchdringen kann. Es gibt verschiedene Methoden der Aufkohlung: feste Aufkohlung (Holzkohle), flüssige Aufkohlung (Cyanidsalz) und gasförmige Aufkohlung (Kohlenwasserstoffgas), je nach Art des verwendeten Aufkohlungsmittels.
Da die Aufkohlung mit einer längeren Erhitzung bei hohen Temperaturen verbunden ist, wird das Gefüge im zentralen Teil des Bauteils verändert. Daher werden nach der Aufkohlung in der Regel Abschreck- und Anlaßprozesse durchgeführt. Diese Behandlung wird in erster Linie bei kohlenstoffarmen Stählen angewandt und führt zu einer Oberfläche mit erhöhter Härte und Verschleißfestigkeit, während die innere Struktur flexibel bleibt.
Nitrieren
Bei Nitrieren wird die Härte der Oberfläche eines Bauteils durch das Einbringen von Stickstoffverbindungen erhöht. Zu den Verfahren gehören das Gasnitrieren, das Salzbadnitrieren, das Gas-Weichnitrieren und das Ionen-Nitrieren. Indem die Oberfläche einer ammoniak- oder stickstoffhaltigen Atmosphäre bei Temperaturen unterhalb der Austenitisierungstemperatur ausgesetzt wird, dringt Stickstoff in die Oberfläche ein und führt zu einer Härtung.
Beim Nitrieren ist keine Erhöhung der Behandlungstemperatur erforderlich, wodurch eine Wärmebehandlung nach der Behandlung entfällt und die Verformung minimiert wird. Man unterscheidet zwischen Nitrieren, bei der eine Härte von etwa 1000HV erreicht wird, und der Weichnitrierbehandlung, die etwa 600HB erreicht und die Ermüdungsbeständigkeit verbessern soll.
Aufgrund der niedrigen Behandlungstemperatur können selbst vergütete Stähle eine höhere Oberflächenhärte erreichen, während die innere Härte erhalten bleibt. Es ist auch bekannt, dass es für austenitische nichtrostende Stähle wie EN 1.4301 äquiv. (SUS304) und EN 1.4401 äquiv. (SUS316) eingesetzt wird. Die Dicke und Härte der Nitrierschicht variiert mit der Behandlungstemperatur und liegt typischerweise zwischen 0,1 und 0,5 mm.
Schlussfolgerung - Wichtige Punkte, die bei der Konstruktion bezüglich der Wärmebehandlung zu beachten sind
In dieser Diskussion haben wir uns mit den üblichen Wärmebehandlungen von Bauteilen befasst. Es ist offensichtlich, dass die Wärmebehandlung ein äußerst wirksames Mittel zur Härtung von Oberflächen, zur Verbesserung der Verschleißfestigkeit und zur Erhöhung der Schlagfestigkeit von Bauteilen ist. Es ist jedoch wichtig, bei der Anwendung von Wärmebehandlungen bestimmte konstruktive Aspekte zu beachten.
Ein wichtiger Aspekt ist, dass die Wärmebehandlung zu Verformungen und Maßänderungen aufgrund der Wärmeeinwirkung führen kann. In Präzisionsbereichen kann es erforderlich sein, für Nachbearbeitungsprozesse Spielraum zu lassen, um genaue Formen zu erhalten.
Durch Wärmebehandlung gehärtete Bauteile können die Bearbeitung mit Schaftfräsern erschweren, insbesondere wenn die Härte HRC60 übersteigt. Daher ist es wichtig, Umfang und Lage der Freiräume sowie die Nachbearbeitungsmethoden im Voraus zu bestimmen.
Das Schleifen ist bei Flächen und zylindrischen Formen relativ einfach. Bei Formen mit Stufen sind jedoch spezielle Schleifmethoden wie das Hinterschleifen (z. B. Hinterschliff) erforderlich, um den Kontakt zwischen der Schleifscheibe und der Oberfläche zu vermeiden.
Für komplexe Formen, bei denen eine konventionelle Bearbeitung schwierig ist, kann die Endbearbeitung spezielle Schleifmaschinen erfordern, was die Bearbeitungskosten erhöhen kann. Die Minimierung der Bereiche, die nachbearbeitet werden müssen, kann zur Kostensenkung beitragen, daher sollten Sie sich um Konstruktionen bemühen, die nur eine minimale Nachbearbeitung erfordern.
Wenn Verformung ein Problem darstellt, kann Nitrieren eine sinnvolle Alternative sein. Wenn außerdem eine hohe Oberflächenhärte erforderlich ist, sollten Sie Alternativen wie Hartverchromen oder Vernickeln in Betracht ziehen, die bereits vorgestellt wurden.
Der effektive Einsatz der hier besprochenen Wärmebehandlungsmethoden in Ihren Konstruktionen kann zu rationellen und effizienten Konstruktionen führen.