- HELP
- Technical Information
- CNC Turning
- Design Guidelines
- Difference in Shapes Between the 3D Model and the Finished Product
Difference in Shapes Between the 3D Model and the Finished Product
- Points to Note on the Finished Shape of Internal and External Corners of Turning parts
- Points to Note on Center Holes
- Points to Note on the Bottom of Holes (Machined and Cut)
- Points to note regarding cylinder corners
- Points to Note on Incomplete Threads
- Points to Note on the Tapered Thread (ISO)
- Points to note for the finished shape of the end-face groove inner corners
- Points to Note for the Finished Shape of Pocket Internal Corners
- Points to Note for Sliting processing
- Hexagonal Hole Notes
Points to Note on the Finished Shape of Internal and External Corners of Turning parts
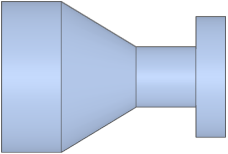
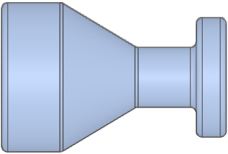
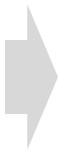
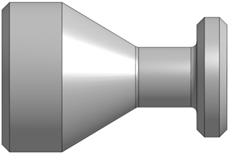
Tip
The finish conditions are as follows.- Models with external edges of less than C/R0.5 will have C/R 0.1 to 0.4 mm or slight chamfer.
- If the internal corners of the cylinder are less than 0.5 and there is no relief groove in the model, the tool edge will leave a corner of R0-R0.4mm.
→Click here to specify “Corner R0” without modeling a relief groove.
Caution
- When modelled with ≥C0.5 mm or more, machining will be in accordance with the 3D data.
- When modelled with ≥R0.5 mm or more, machining will be in accordance with the 3D data.
Caution
Specification of “no chamfer” is not supported.Notes
-
- A standard retaining ring grooving tool has corner R0.2
- For retaining ring standards, click here.>>>Specifications for External Thread and Internal Thread, Keyways, Holes and Pockets
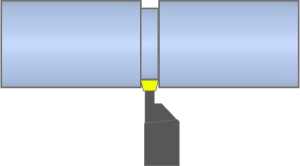
Outer diameter grooving
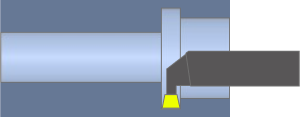
Inner diameter grooving
Points to Note on Center Holes
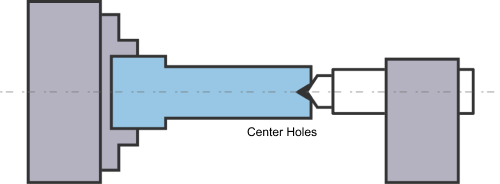
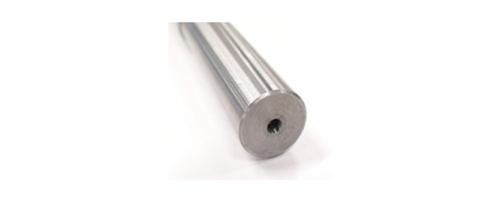
Caution
- 「”Center hole cannot be left” can be selected, but there may be restrictions on the shapes that can be machined that make the option unavailable. When this occurs, check the “Precaution” in the upper-left corner of the 3D Viewer.
Notes
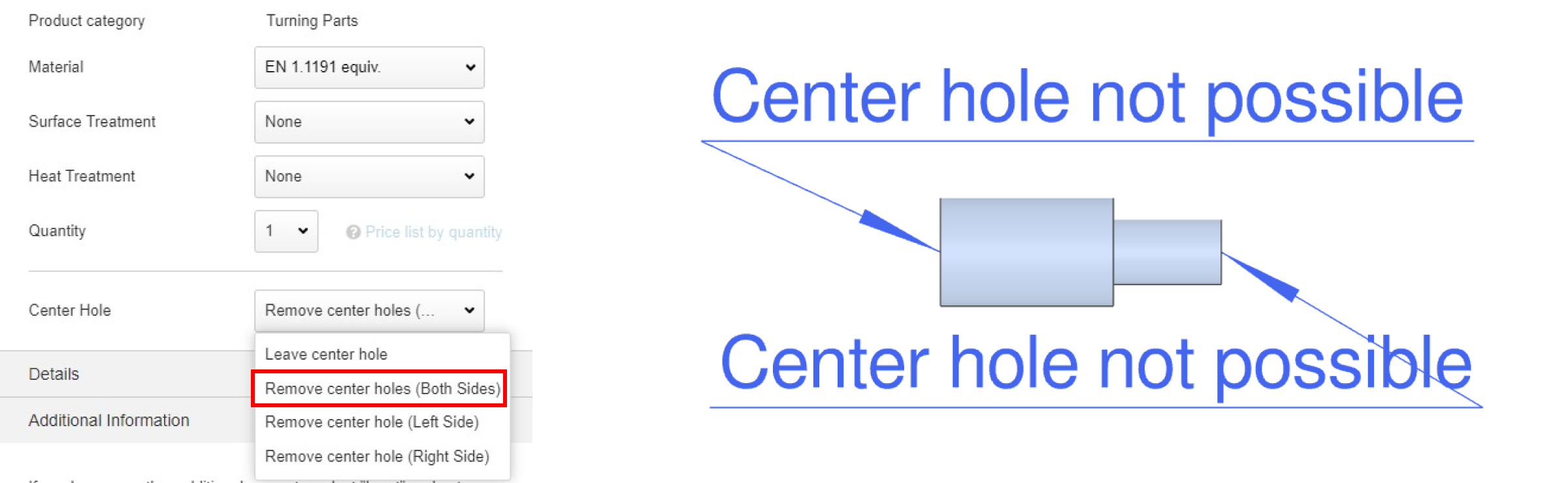
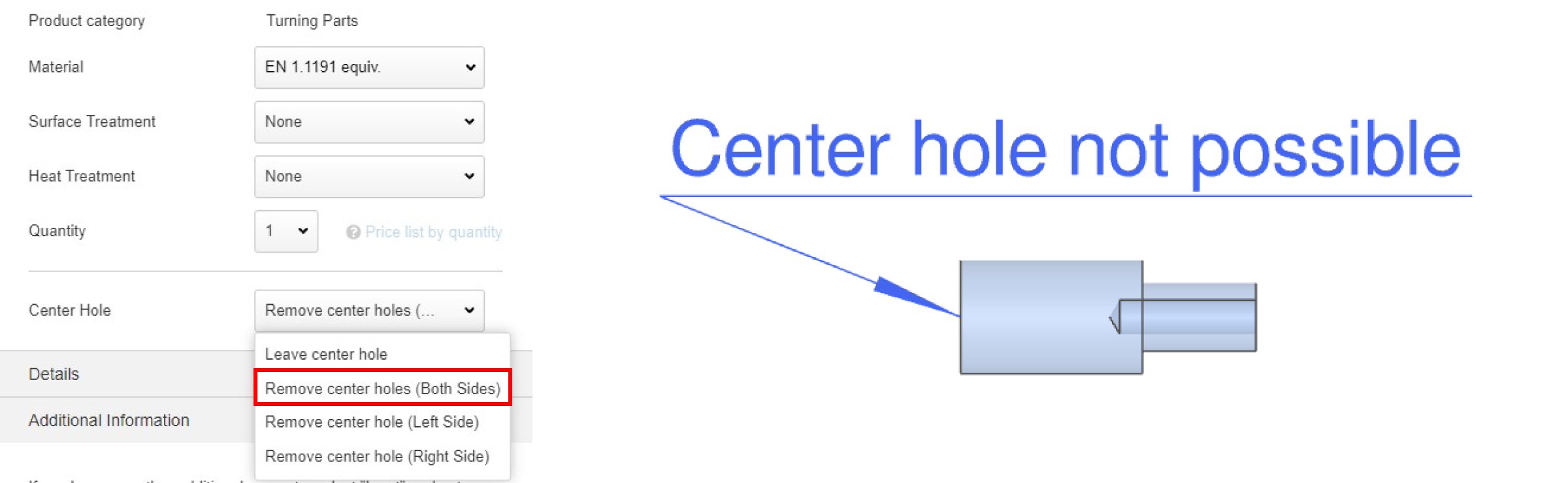
Points to Note on the Bottom of Holes (Machined and Cut)
Shape patterns | Inner diameter hole does not have a step | Inner diameter hole has a step |
---|---|---|
A | ![]() |
![]() |
Drill tip shape remains (flat bottom will be 1mm or more) | ||
B | ![]() |
![]() |
Drill tip shape remains, no flat bottom |
- The type of the bottom of the hole will depend on the diameter and depth of the hole.
- Example: If the inner diameter (D) is 10mm and the hole depth is 35mm, the depth of 35mm ÷ inner diameter of 10mm = 3.5D, so the bottom of the hole type will be B.
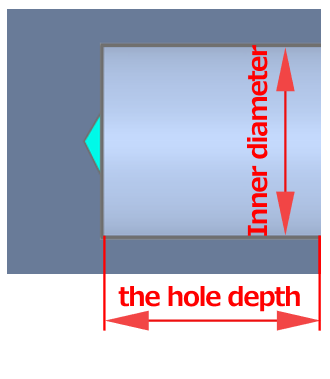
Inner diameter(D) | the hole depth | ||
---|---|---|---|
to 3D | 3D to 5D | 5D to 10D | |
D≦⌀6 | B | B | B |
⌀6 <D≦⌀30 | A | B | B |
⌀30<D | A | A | A |
If a flat bottom hole is required, please request it in “Additional Information”. We will confirm whether or not we can accommodate your request and reply.
Points to note regarding cylinder corners
Outer diameter
- When you want to minimize the corner R or specify the relief groove
- → Select “Corner R0”
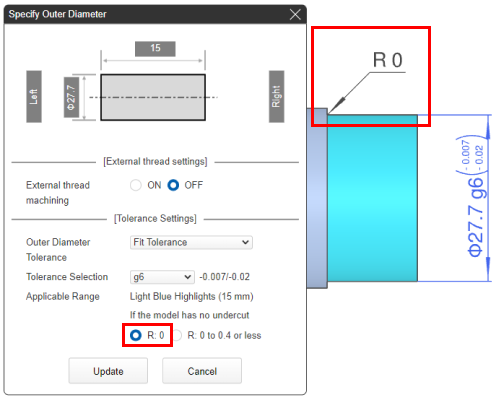
Tip
Corner R0 has a width of less than corner R0.2 to R0.4, so the depth may be less than 0.5mm. You cannot choose.
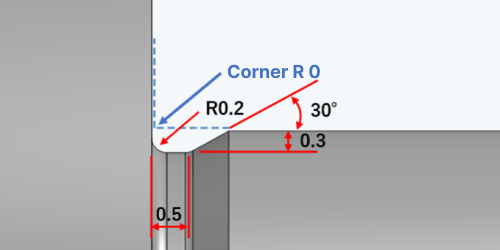
③ If the length of the shaft is short, it may be machined with a tool with a 0.1mm radius on the end face that contacts the shaft.
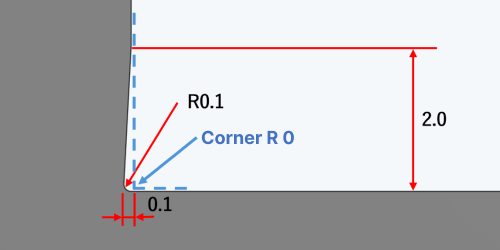
Notes
(1) The model has corner R0.5 or greater | (2) The model has a relief groove |
![]() |
![]() |
- When the cylindrical corner can be any shape
- → Select “Corner Radius between R0 to R0.4”.
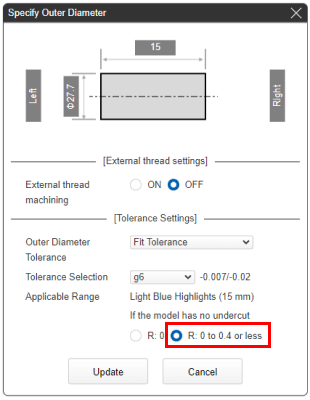
Tip
- Arbitrary R shape of cylindrical corner
- ① Machining R remains
- ② Relief groove (1) Minimum clearance only at the cylindrical corner
-
Finished shape after
Detailed figure
- ③ Relief groove (2) Relief shape on cylindrical part + flange part
-
Finished shape after machining
Detailed figure
Modeling of R0.5 or higher in corners
Finished shape after machining
Detailed figure
Inner diameter
Cross section
①Detailed figure
②Detailed figure
Notes

Points to Note on Incomplete Threads
[mm]
External Thread | Internal Thread | ||
---|---|---|---|
Modelling | Without undercut | ![]() |
![]() |
With undercut | ![]() |
![]() |
|
(1) Lower limit for the length of the incomplete thread and the width of the undercut. | Pitch × 2.0 | Pitch × 2.5 + 2 | |
(2) Lower limit of the length of the threaded (external thread) and the depth of the threaded (internal thread). | Pitch × 2.0 | Pitch × 2.0 | |
(3) Chamfered edge | Chamfered to prevent burr | Chamfered to prevent burr | |
(4) Minimum undercut depth value | Pitch × 0.75 | Pitch × 0.75 |
Caution
Parts with “Pitch × 0.75” or less set to the minimum value for the undercut depth(4) can be machined, but thread marks may occur.Reference model
Actual finished shape after machining
Tip
- The [Notes] shown in the red box below describe the applicable thread length/thread depth.
Example 1) Outer diameter specification: male thread thread length 44.6mm – 4.0 (pitch) x 2.0 = 36.6mm | Example 2) Inner diameter specification: female screw thread depth 15.5mm – (1.0(pitch) × 2.5 + 2.0) = 11.0mm |
![]() |
![]() |
Caution
- The thread shape cannot be identified. Set the outer and inner threads.
Points to Note on the Tapered Thread (ISO)
- Although there are multiple methods for modeling tapered pipe threads, the diameter and depth of the tapered pilot hole will be machined in accordance with ISO standards (or JIS B 0203). The modeled shape and depth of the hole are for reference only.
- Other areas of the part that are not threaded, such as the area beyond the pilot hole, will be machined to the model.
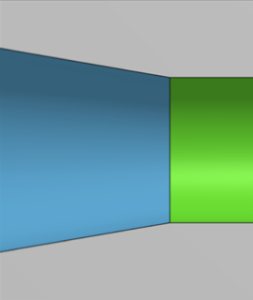
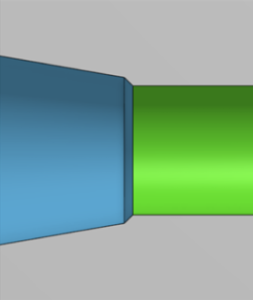
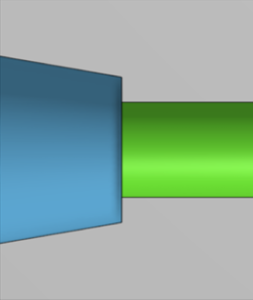
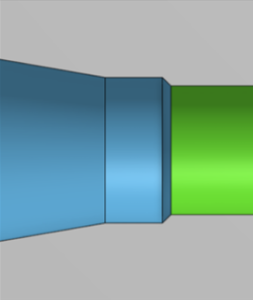
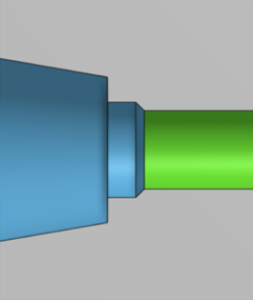
Machined according to ISO standards (or JIS B 0203)
Machined according to the model
Points to note for the finished shape of the end-face groove inner corners
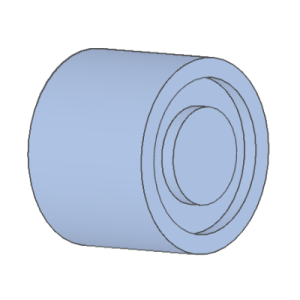
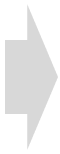
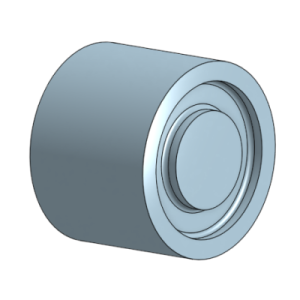
Notes
Since the shape is finished to R0.1 to 0.5, no modelling is required. Design with sharp edges.Points to Note for the Finished Shape of Pocket Internal Corners
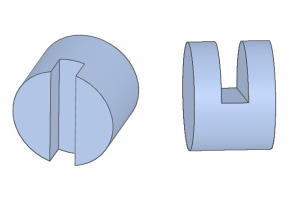

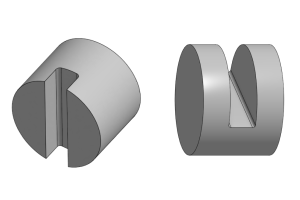
Caution
- The machined curve on the sides of the pocket depends on the tool diameter, which is chosen as small as possible.
- If there are any discrepancies between the model and the finished form, please feel free to let us know.
Points to Note for Sliting processing
The dimensions of the parts may change as a result of the slitting process. Therefore, the dimensions of the following shapes are guaranteed based on the measurements taken before slitting.
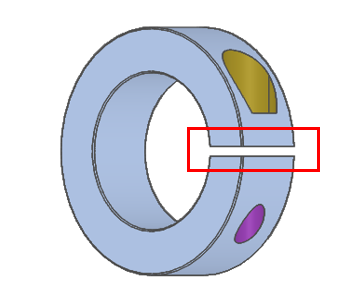
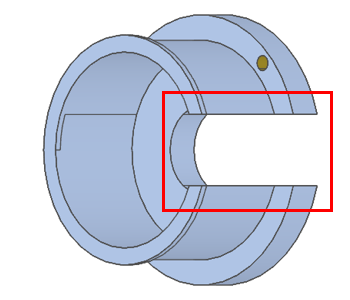
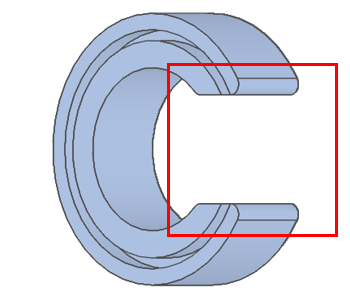
Hexagonal Hole Notes
Information and examples of differences between the model and the finished part.
- The shape of the finished hexagonal hole will vary depending on the distance across the flats.
- The modeled depth is used as a reference, and the shape of the bottom of the hole will vary.
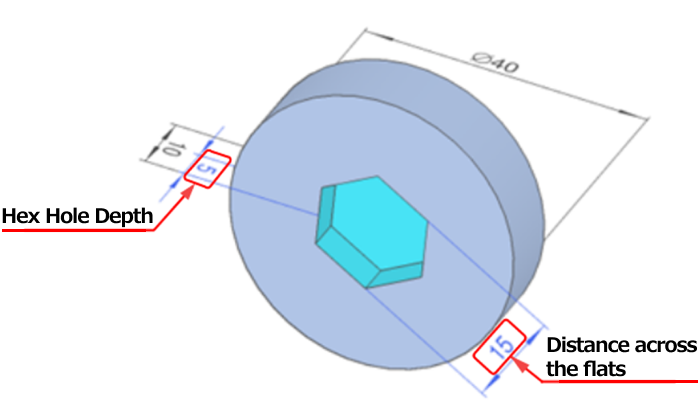
Hexagonal Hole corresponding shapes and sizes
Distance across the flats | Metal | Resin |
---|---|---|
2 | Finished Shape① | |
2.5 | ||
3 | ||
4 | ||
5 | ||
6 | Finished Shape② | |
8 |
Caution
The roughness specified for the surface does not apply to the internal hexagon.
Finished Shape①
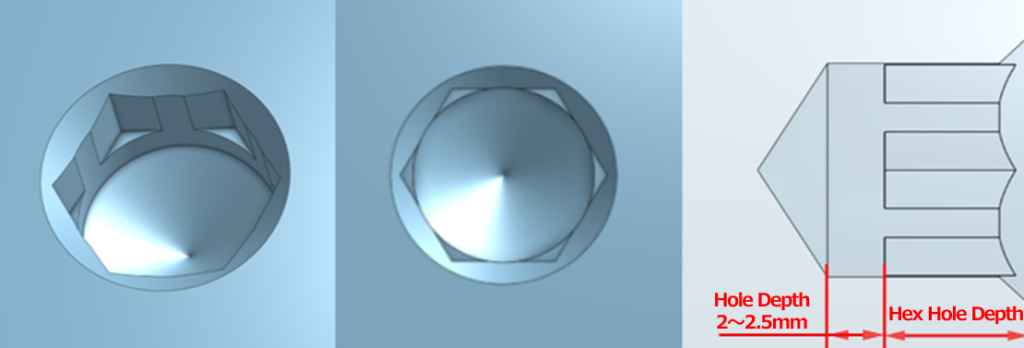
Distance across the flats | Metal | Resin |
---|---|---|
Other | Finished Shape② |
Notes
The tolerance for the distance across the flats meets to the JIS B 1176.
Finished Shape②
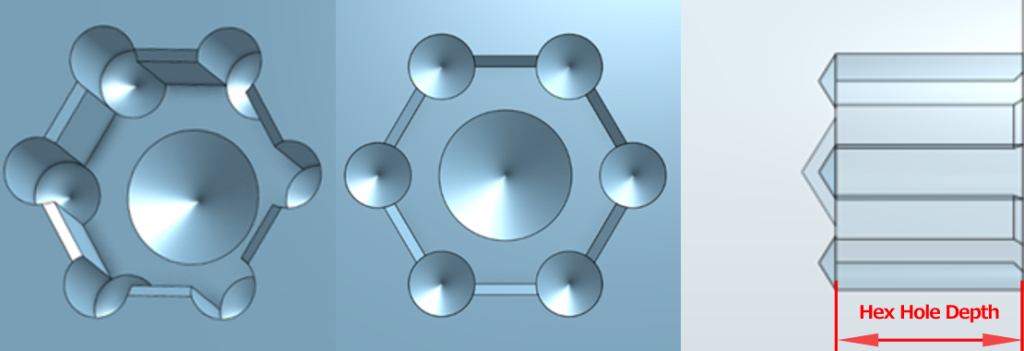